Schläuche dienen zum Fördern verschiedener Medien in vielen Industriebereichen. Je nach Anwendung zum Beispiel als Kraftstoffschläuche, Medizinschläuche, Industrieschläuche, Chemikalienschläuche, Vakuumschläuche, Druckluftschläuche oder einfach nur als Gartenschläuche sind unterschiedliche Eigenschaften gefordert. Zur Auswahl der geeigneten Schlauchsorte helfen Kenngrößen wie das Schlauchmaterial, das Temperatur-, Chemikalien- und UV-Beständigkeit bestimmt, Innen- und Außendurchmesser, Wandstärke, Betriebs- und Berstdruck, Biegeradius sowie die Leitfähigkeit.
Welche Schlauchwerkstoffe werden eingesetzt?
Die Kunststoffe Polyamid (PA), Polyethylen (PE), Polytetrafluorethylen (PTFE), Polyurethan (PUR), Polyvinylchlorid (PVC), thermoplastische Elastomere (TPE) und Fluorkunststoffe werden häufig als Schlauchmaterialien verwendet.
Kunststoffschläuche werden vor allem dann eingesetzt, wenn Eigenschaften wie geringes Gewicht, chemische Beständigkeit oder Transparenz gefragt sind. Sie sind UV-beständig, druckbeständig und können in einem breiten Temperaturbereich eingesetzt werden – dafür sind sie jedoch recht starr und nicht elastisch.
Gummischläuche aus Elastomeren wie Naturkautschuk oder Synthesekautschuken sind – wie der Name bereits preisgibt – gummielastisch und flexibel. Ohne zusätzliche Verstärkung durch Außenmantel, Gewebe oder Spirale sind sie jedoch nicht sonderlich druckbeständig. Ihre Temperaturbeständigkeit und chemische Beständigkeit ist im Vergleich zu harten Kunststoffschläuchen, beispielsweise PTFE-Schläuche, reduziert. Sie finden Anwendung bei der Wasserförderung, bei der Förderung abrasiver und aggressiver Medien sowie als Schweißschläuche.
Einen Sonderfall stellen Kapillare und Wellschläuche aus Edelstahl dar. Sie sind sowohl für Vakuum- wie auch Hochdruckanwendungen konzipiert und trotz selbst den widrigsten Temperaturbedingungen bis +550 °C.
Der Schlauchaufbau: Verstärkungen, Ummantelungen & mehr
Neben dem Schlauchmaterial spielt auch der Schlauchaufbau eine wichtige Rolle für die Eigenschaften.
Einfache Kunststoff- und Elastomerschläuche bestehen lediglich aus einer Schicht. Solche Schläuche kommen beispielsweise als Pumpenschläuche, Mikroschläuche und Kapillaren zum Einsatz. Ihre Druckbeständigkeit ist – je nach Werkstoff und Wandstärke – mehr oder minder eingeschränkt.
Viele Schläuche bestehen jedoch aus mehreren Schichten: aus einem Innenschlauch, der Seele, einer Verstärkung und einer Ummantelung, der Decke. Das Material des Innenschlauchs muss mit dem Fördermedium kompatibel sein.
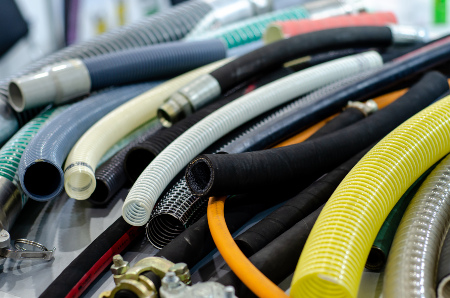
Die Schlauchverstärkung dient der Formstabilität und Druckfestigkeit und kann aus mehreren Schichten bestehen. Abhängig von der Anwendung können Stahl- oder Kunststoffdrähte oder Metall-, Textil- oder Kunststoffgeflechte als Verstärkung verwendet werden. Die Ummantelung dieser Doppelmantelschläuche sorgt für den Schutz vor Witterung, äußeren Beanspruchungen wie Abrieb oder Scheuern und für die Isolation.
Kenngrößen Innendurchmesser, Wandstärke und Außendurchmesser
Der Innendurchmesser wird auch als Nennweite, abgekürzt NW oder DN aus dem Französischen „diamètre nominal“, bezeichnet. Die Maßangabe erfolgt häufig aus historischen Gründen in Zoll, korrekt ist jedoch die Angabe in mm nach DIN EN ISO 6708 „Rohrleitungsteile – Definition und Auswahl von DN (Nennweite)“. Der Außendurchmesser ergibt sich aus der Summe des Innendurchmessers und der zweifachen Wandstärke.
Bei weichen Schläuchen, die auf Schlauchtüllen oder Schlauchstutzen aufgeschoben werden, ist vor allem der Innen-Ø von Relevanz. Aber auch der Außen-Ø kann von Bedeutung sein, wenn die Fixierung zusätzlich durch eine Schlauchschelle gesichert werden soll.
Bei harten Schläuchen und Kapillaren, die mittels Schneidringverschraubungen oder Ferrulen adaptiert werden sollen, ist der Außen-Ø das entscheidende Maß. Der Schneidring liegt außen auf dem Schlauch auf und wird mittels Überwurfmutter fixiert.
Bei Klemmringverschraubungen, die sowohl für harte wie auch weiche Schläuche eingesetzt werden, sind sowohl das innere wie auch das äußere Maß von Bedeutung. Das Schlauchende wird dabei auf eine Stützhülse geschoben und anschließend mittels außen aufliegendem Klemmring und Überwurfmutter fixiert.
Die Verbinder aus Kunststoff und Metall werden in zahlreichen Bauformen und gefertigt aus unterschiedlichen Werkstoffen angeboten.
Was ist der Unterschied zwischen Betriebsdruck und Berstdruck?
Der Berstdruck ist die Druckbelastung, bei der ein Schlauch platzt. Die Prüfung des Berstdrucks erfolgt nach der Norm DIN EN ISO 1402:2021-08 „Gummi- und Kunststoffschläuche und Schlauchleitungen – Hydrostatische Prüfung“. Durch den Berstdruck wird der Betriebsdruck nach der Norm DIN EN ISO 7751:2017-06 „Gummi- und Kunststoffschläuche und -schlauchleitungen – Verhältnisse von Prüf- und Berstdruck zur Auslegung des maximalen Betriebsdruckes“ festgelegt.
Bei einem Wasserschlauch oder Heißwasserschlauch mit einem Betriebsdruck von 10 bar beträgt das Verhältnis Betriebsdruck: Berstdruck 1:3, für andere Flüssigkeiten und Druckluft 1:4. Schlauchsysteme, die Flüssigkeiten fördern, die beim Ablassen in die Atmosphäre verdampfen, beträgt der Berstdruck das Fünffache des Betriebsdrucks. Dampfschläuche müssen sogar dem zehnfachen Betriebsdruck standhalten.
Der Prüfdruck dient dem Nachweis eines funktionsfähigen Schlauchsystems. Über eine festgelegte Zeitdauer wird das Schlauchsystem dem Prüfdruck ausgesetzt, der bis zu 50% über dem Betriebsdruck liegen kann. Das Schlauchsystem darf beim Prüfdruck keine Leckagen oder dauerhafte Veränderungen aufzeigen.
Kenngröße Biegeradius
Jedes Schlauchsystem hat einen bestimmten Mindestbiegeradius, der von dem Material, dem Innendurchmesser, der Wandstärke, der Verstärkung sowie der Temperatur, dem transportierten Medium und dem Mediendruck abhängt. Verstärkte Schläuche haben meist einen größeren Biegeradius als einfache Gummischläuche.
Bei niedrigen Temperaturen wird der Schlauchmantel häufig steif, was zu einem größeren Biegeradius führt. Ein mit Wasser gefüllter Schlauch lässt sich enger biegen als einer, der mit Luft gefüllter ist, da der Wasserdruck den Schlauchmantel stabilisiert. Wird der Biegeradius unterschritten, kann es zu Leckagen oder sogar Brüchen kommen. Durch Unterstützung oder Führung von Schlauchleitungen können solche Schäden vermieden werden.
Kenngröße Shore-Härte
Die Härte ist ein Indiz für das Verformungsverhalten und die mechanische Belastbarkeit. Härtere Materialien besitzen eine geringere Flexibilität, jedoch eine höhere mechanische Belastbarkeit als weichere.
Die Eigenschaft Härte wird durch die Härteprüfung nach Shore mit einem Härteprüfer, auch Durometer genannt, bestimmt. Dabei wird ein dünner, kegelförmiger Stift aus gehärtetem Stahl, der als Intender bezeichnet wird, mit definierter Federkraft für eine definierte Zeit in das Testmaterial gedrückt und die Eindringtiefe des Intenders gemessen. Die Eindringtiefe wird auf einer Skala von 0 bis 100 Shore angegeben, wobei eine Tiefe von 0 mm 100 Shore entsprechen und eine Tiefe von 2,5 mm 0 Shore entsprechen.
Je nach Materialhärte werden unterschiedliche Intender eingesetzt. Für weiche Materialien wie Gummimatten und Silikonschläuche wird ein Prüfkörper mit flacher Spitze und einem Gewicht von 1 kg verwendet. Die Härte wird als Shore-Härte A bezeichnet.
Härte Materialien wie Polyethylen (PE) oder Polyamid (PA) werden mit einem 5 kg schweren Intender mit abgerundeter Spitze untersucht. Ihre Härte wird in Shore-Härte D angegeben. Ausführliche Informationen zur Härteprüfung nach Shore sind in unserem Magazinartikel „Die Shore-Härten A und D“ zu finden.
Kenngröße Leitfähigkeit
Bei der Förderung von Flüssigkeiten und Feststoffen wie Pulver oder Granulaten durch Schlauchsysteme entsteht Reibung, die zur elektrostatischen Aufladung der Schlauchwand und zur Funkenfreisetzung führen kann. Um dies zu vermeiden, werden leitfähige oder ableitfähige Schlauchsysteme eingesetzt, sogenannte Antistatikschläuche.
Nach den Berufsgenossenschaftlichen Regeln für Sicherheit und Gesundheit bei der Arbeit (BGR) gilt ein Material mit einem spezifischen Widerstand kleiner oder gleich 104 Ωm als leitfähig. Liegt der spezifische Widerstand zwischen 104 und 109 Ωm wird das Material als ableitfähig bezeichnet. Die Leitfähigkeit des Schlauchmaterials kann durch leitfähige Additive wie zum Beispiel Graphitpulver erhöht werden. Alternativ kann eine integrierte Drahtspirale oder ein Metallgeflecht für die Ableitung möglicher Aufladungen genutzt werden.
Dimensionierung von Schlauchsystemen
Für die Dimensionierung sind die Kenngrößen Volumenstrom, Innendurchmesser und Strömungsgeschwindigkeit ausschlaggebend. Mit Hilfe eines Diagramms, auch Nomogramm genannt, das diese drei Kenngrößen enthält, kann der Schlauchinnendurchmesser bei bekanntem Volumenstrom abgelesen werden. Für die Strömungsgeschwindigkeit wird die aus der Praxis abgeleitete die 6-3-1-Regel herangezogen. Diese gibt die folgenden Richtwerte vor: 6 m/s in Druckleitungen, 3 m/s in Rücklaufleitungen und 1 m/s in Saugleitungen.
Wird der Schlauchinnendurchmesser zu klein gewählt, steigt die Strömungsgeschwindigkeit an, was eine erhöhte innere Reibung zur Folge hat. Diese führt zu einem Druckverlust und einer Wärmeentwicklung im Schlauchsystem. Dadurch können in bestimmten Elastomer-Schläuchen Weichmacher entweichen, die Schlauchleitungen verlieren an Flexibilität und härten schneller aus.
Um einen sicheren Betrieb von Chemieschläuchen zu gewährleisten, müssen diese in regelmäßigen Intervallen überprüft werden. Bei einer optischen Sichtprüfung werden Risse, Verformungen, Abrieb- oder Knickstellen erfasst. Mit Druckprüfungen werden Funktionsfähigkeit der Schlauchseele und Verstärkung getestet. Bei leitfähigen und ableitfähigen Schlauchsystemen muss auch die Leitfähigkeit überprüft werden. Dokumentierte Prüfergebnisse und Prüfbänder dienen dem Betreiber von Schlauchsystemen als Nachweis für seine Sorgfaltspflicht.
Bild-Quellen: Beitragsbild | ©79mtk – stock.adobe.com Schläuche und Wellrohre in verschiedenen Ausführungen | © Олександр Луценко – stock.adobe.com