Mit Formpressen zum komplexen Produkt in einem Schritt: Formpressen und Spritzgießen sind wichtige Kunststoffverarbeitungsverfahren, um Halbzeuge und Formteile herzustellen. Beide Fertigungsverfahren beinhalten das Erhitzen und Umformen von Kunststoffen, unterscheiden sich jedoch in der Prozessführung, dem Produktdesign und den Kosten.
So funktioniert Formpressen
Wie der Name schon sagt, wird beim kunststoffverarbeitenden Formpressverfahren Kunststoff in eine Form gepresst. Die Form wie auch das Presswerkzeug werden durch maschinelle Bearbeitung, Druckguss oder 3D-Druck hergestellt. Anfangs wird die benötigte Kunststoffmenge bestimmt, um zu vermeiden, dass überschüssiges Material aus der Form austritt und einen Grat bildet, der manuell entfernt werden muss. Sodann werden die Pressform und/oder der Kunststoff vorgeheizt und das Material in der Form platziert.
Die Form wird geschlossen, und die beiden Pressformen werden mechanisch verpresst. Dadurch erhält die Kunststoffmasse die durch das Presswerkzeug vorgegebene Form. Durch die erhöhte Temperatur beim Formpressen schmelzen thermoplastische Kunststoffe, duroplastische hingegen härten aus. Nach dem Abkühlen durch Luft- oder Wasserkühlung wird das Formteil entnommen, gereinigt und Grate an den Kanten händisch entfernt.
Vor- und Nachteile von Formpressen
Vorteile von Formpressen sind niedrige Investitionskosten sowie die Möglichkeiten, große und dicke Formteile herzustellen.
Nachteile von Formpressen liegen in der relativ langen Zykluszeit, die aufgrund des Aufheizens und Abkühlens zwischen einigen Minuten bis zu einigen Stunden dauern kann, je nach Material und Bauteilgröße. Um der langen Zykluszeit entgegenzuwirken, werden Pressformen mit mehreren Hohlräumen verwendet, sodass in einem Zyklus mehrere Teile gleichzeitig produziert werden können.
Wie funktioniert Spritzguss?
Beim Spritzgießen wird flüssiger Kunststoff unter hohem Druck in den Hohlraum einer Form gespritzt. Spritzgießmaschinen bestehen aus einer Spritz- und einer Schließeinheit. Über einen Einfülltrichter wird das Rohmaterial in die Spritzeinheit gefüllt, wo es durch eine rotierende Schnecke durch Hitze und Reibung aufgeschmolzen und zu einer Düse befördert wird.
Unter hohem Druck von 500 bis 2.000 bar wird die Schmelze durch die Düse in die Schließeinheit gespritzt. Die Temperatur der Werkzeuge in der Schließeinheit beträgt zwischen +20 °C und +120 °C, wodurch die Schmelze, deren Temperatur meist zwischen +200 °C und +300 °C liegt, in der Form abkühlt und erstarrt.
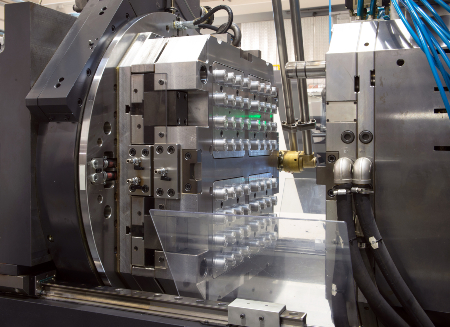
Spritz- und Schließeinheit werden getrennt, um einen Wärmeübergang von der Spritzeinheit auf die Schließeinheit zu verhindern. In der Spritzeinheit wird neues Rohmaterial für den nächsten Zyklus vorbereitet.
Ist das Formteil vollständig abgekühlt, wird es aus der Schließeinheit ausgeworfen oder entnommen. Beide Einheiten werden geschlossen, und der nächste Zyklus startet. Zykluszeiten betragen beim Spritgießen typischerweise weniger als eine Minute.
Vor- und Nachteile von Kunststoffspritzguss
Spritzgussverfahren zeigen auch einige Nachteile: Die hohen Drücke während des Fertigungsprozesses stellen höhere Anforderungen an die Werkzeuge, was die Kosten erhöht. Bei diesem Kunststoffverarbeitungsverfahren ist die Dicke zwischen 15 und 20 mm limitiert. Daher eignet sich Kunststoffspritzguss nicht, um große Bauteile dünner Wandstärke herzustellen, wie Verkleidungen oder Paneele.
Welche Kunststoffe werden eingesetzt?
Beide Verfahren der Kunststoffverarbeitung eignen sich prinzipiell für die Umformung von thermoplastischen Kunststoffen, Duroplasten, Elastomeren und Verbundwerkstoffen. Mit Spritzguss werden überwiegend thermoplastische Kunststoffe verarbeitet, während beim Formpressen hauptsächlich duroplastische Kunststoffe, Elastomere und Verbundwerkstoffe umgeformt werden.
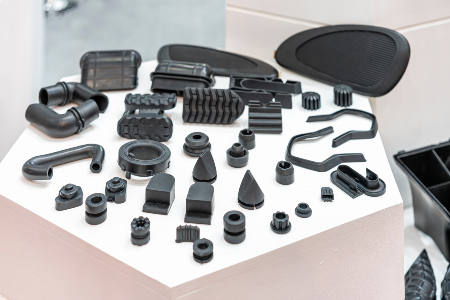
Da Thermoplaste in einem bestimmten Temperaturbereich reversibel erhitzt und abgekühlt werden können, lassen sich diese Kunststoffe mehrfach umformen. Für transparente Produkte wie etwa Reagenzglas-Gestelle, Petrischalen oder Kunststoffplatten werden Polycarbonat (PC) und Polymethylmethacrylat (PMMA) verwendet, für Haushaltsgeräte und Spielzeug Polyethylen (PE), Polypropylen (PP) und Acryl-Butadien-Styrol (ABS). Polystyrol (PS) wird häufig auch für Verbrauchsmaterialien in der Laboranalytik eingesetzt, etwa für Laborröhrchen und Küvetten. Technische Kunststoffe wie Polyamid (PA) oder Polyoxymethylen (POM) finden Anwendung im Maschinenbau und der Elektrotechnik.
Wenn es um thermisch und chemisch anspruchsvolle Anwendungen geht, wird der Fluorkunststoff Perfluoralkoxy (PFA) eingesetzt, beispielsweise als Kunststoffschlauch. PFA kann im Spritzgussverfahren auch zu Schlauchverbindern und Gewindeadaptern verarbeitet werden.
Beim duroplastischen Formpressen werden Harz und Additive in die Pressform gefüllt. Während des Formpress-Prozesses findet die Vernetzung und Aushärtung statt. Da duroplastische Kunststoffe nach der Aushärtung nicht mehr schmelzbar sind, müssen Formgebung und Vernetzung gleichzeitig ablaufen, was beim Formpressen gegeben ist. Epoxid-, Phenol-, Polyester- und Vinylharze sowie vernetzbare Polyurethane können mit dieser Kunststofftechnik geformt werden. Die Harze können auch mit anderen Materialien wie Glas-, Kohle- oder Polyamid-Fasern gemischt werden, um hochfeste Verbundwerkstoffe mittels Formpressen herzustellen.
Elastomere wie Naturkautschuk (NR), Nitrilkautschuk (NBR), Butylkautschuk (IIR), Styrol-Butadien-Kautschuk (SBR) und Ethylen-Propylen-Dien-Kautschuk (EPDM) sind als Schlauchwerkstoffe für Gummischläuche bekannt. Sie werden auch beim Formpressen eingesetzt und dort in unvernetzter Form in das Presswerkzeug gebracht. Unter Druck und bei Temperaturen zwischen +140 °C und +200 °C erfolgt die Vulkanisation des Rohkautschuks.
Formpressen vs. Spritzguss: Welches Verfahren wird bevorzugt?
Anwendungsbeispiele: Formpressen
OEM und Zulieferer der Automobilindustrie fertigen mit Formpressverfahren große Teile wie Verkleidungen für Autos und Traktoren, Stoßfänger, Motorhauben, Türen, Heckklappen, Kotflügel sowie Motorkomponenten und Armaturenbretter.
Haushaltsgegenstände wie große Möbelteile, Aufbewahrungs- und Wäschekörbe, Regale und Kunststoffgeschirr wie Teller, Tassen, Schüsseln, Besteck und Aufbewahrungsbehälter werden formgepresst. Im medizinischen Bereich wird Formpressen zur Herstellung von großen Geräteplatten, Krankenhausbettkomponenten, Gehäuse für Diagnosegeräte, Kolbenstopfen von Spritzen, Beatmungsmasken, Silikon-Atemschutzmasken und Prothesenkomponenten eingesetzt. Auch elektrische Komponenten wie Steckdosen, Schalter, Frontplatten und Gehäuse von Motoren und Messgeräten, Computertürme und Lautsprechergitter werden mit diesem Kunststoffverarbeitungsverfahren hergestellt. Zudem werden formgepresste Gummiteile als Dichtungen, Schläuche und Isolierung in vielen Bereichen verwendet.
Anwendungsbeispiele: Spritzgießen
Zu den Spritzgussanwendungen in der Automobilindustrie zählen Armaturenbrettkomponenten, Lichtabdeckungen, Türgriffe, Motorteile, Scheinwerfer und Rückleuchten. Im Alltag gehören Verpackungen von Reinigungsmitteln und Pflegeprodukten, Flaschenverschlüsse, Küchenutensilien, Vorratsbehälter, Toilettensitze, Mülleimer und Kindersitze, um nur einige zu nennen, zu den im Spritzguss gefertigten Produkten.
In der Medizintechnik werden Einwegspritzen, Infusionsanschlüsse wie Luer-Lock-Verbinder, chirurgische Instrumente, Prothesen, Zahnimplantate und Griffe mit dieser Kunststofftechnik hergestellt. Spritzguss-Teile werden in Bewässerungsanlagen in der Landwirtschaft, in öffentlichen sowie in privaten Bereichen eingesetzt. In der Fluidtechnik werden Schlauchtüllen und andere Verbinder aus Kunststoffen im Spritzgussverfahren hergestellt. In der Elektronikindustrie werden Gehäuse von Fernbedienungen, Computern, Fernsehern und anderen Elektrogeräten mit dieser Kunststofftechnik produziert.
Sowohl Formpressen als auch Spritzgießen sind wichtige Verfahren in der Kunststoffverarbeitung mit Stärken und Schwächen. Welches der beiden Fertigungsverfahren zum Einsatz kommt, hängt ab vom Produktionsvolumen, der Komplexität der Formteile, dem Material und nicht zuletzt von den Kosten.
Bildquellen: Beitragsbild | © Sergey Ryzhov – stock.adobe.com Spritzgussmaschine | © Moreno Soppelsa – stock.adobe.com Im Formpress-Verfahren hergestellte Bauteile | © Surasak – stock.adobe.com