Die Verwendung von natürlichen Materialien sowie von Werkstoffen anthropogener Herkunft ist fast immer mit der Notwendigkeit verbunden, sie durch mechanische Bearbeitung in die erforderliche Form zu bringen. Zu den grundlegenden Bearbeitungstechniken, die dafür entwickelt wurden, gehören Schneidverfahren.
Die Anfänge des Werkstoffschneidens
Es gibt Anzeichen dafür, dass Vorfahren des Homo Sapiens schon vor über 3 Millionen Jahren einfache Werkzeuge aus Stein nutzten, um beispielsweise Fleisch, Holz und andere Dinge zuzuschneiden. Dafür wurden hauptsächlich Feuerstein und Obsidian, ein schwarzes, glasartiges Gestein vulkanischen Ursprungs, verwendet.
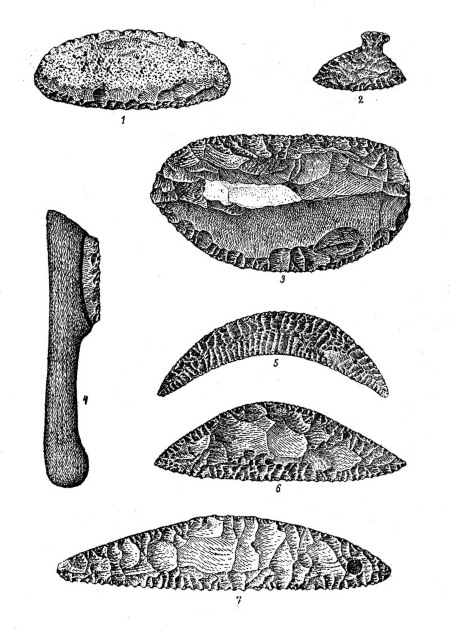
Trotz der mit der Zeit wachsenden Kunstfertigkeit bei der Herstellung von Steinwerkzeugen konnten ihre Gebrauchseigenschaften letztlich nicht mit Werkzeugen aus Metall mithalten, die am Ende der Steinzeit, vor etwa 7000 Jahren, erstmalig in größerer Zahl hergestellt werden konnten und damit die Kupferzeit einleiteten. Dennoch wurden Steinwerkzeuge nicht sofort durch Metallwerkzeuge ersetzt.
Steinblöcke aus Kalkstein wie auch aus Granit, die unter anderem als Baumaterial für die in der Zeit von etwa 2700 bis 2500 vor unserer Zeitrechnung erbauten Pyramiden Verwendung fanden, wurden hauptsächlich mit Steinwerkzeugen in ihre Form gebracht.
Die Härte als wichtige Kenngröße für Schneidverfahren
Eine wesentliche Materialeigenschaft, die für Schneidverfahren eine Bedeutung hat, ist die Härte des zu trennenden Materials. Die Härte basiert auf der Stärke der Bindungen zwischen den Atomen, aus denen das Material besteht. Diese Bindungsstärke wirkt einer Veränderung der relativen Positionen der Atome durch mechanische Krafteinwirkung entgegen.
Größer wird damit allerdings auch die Sprödigkeit des Materials, die Neigung unter Krafteinwirkung zu zerbrechen, statt sich plastisch oder elastisch zu verformen. Die 1812 von dem deutschen Mineralogen Friedrich Mohs (1773 – 1839) veröffentlichte, zehnstufige Härteskala gibt die relative Härte verschiedener Materialien zueinander an: dasjenige Material, das ein anderes Material zu ritzen vermag, erhält eine höhere Mohs-Zahl als das geritzte Material. Das härteste, natürliche Material ist der Diamant mit der Mohs-Härte von 10.
Die Mohs’sche Härteskala stellt die tatsächliche Härte eines Materials allerdings nur unzureichend dar. Sie veranschaulicht jedoch, dass das Material, aus dem der Schneidstoff besteht und mit dem ein Werkstück geschnitten wird, härter sein muss als das Material des schneidend zu bearbeiteten Werkstücks. Anderenfalls würde mehr Material vom Schneidwerkzeug als vom Werkstück abgetragen.
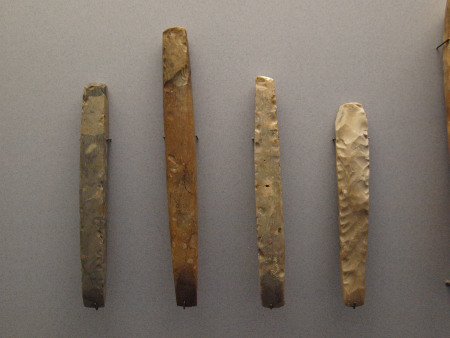
Somit überrascht es auf den ersten Blick, dass die Ägypter dennoch in der Lage waren, mit kupfernen Sägen und Hohlbohrern Granit zu bearbeiten, dessen Mohs-Härte etwa 7 beträgt, während Kupfer eine Mohs-Härte von lediglich 3 aufweist. Tatsächlich war es nicht das Kupfer, welches den Stein schnitt, sondern Quarzsand, der ebenfalls eine Mohs-Härte von 7 aufweist. Über den zu sägenden Stein, entlang des hin- und herbewegten glatten Sägeblattes eingestreuter Sand trug den Stein unterhalb der Schneidkante ab und erzeugte so eine Schnittfuge. Dementsprechend waren die Schneidkanten der verwendeten kupfernen Steinsägen zahnlos, im Gegensatz zu den damals ebenfalls schon verfügbaren kupfernen Sägen für Holz. Dasselbe Schneidverfahren, allerdings mit einer durch einen Bogen erzeugten, oszillierenden Drehbewegung, wurde verwendet, um mit kupfernen Hohlbohrern Steingefäße auszuhöhlen oder Sarkophage aus Steinblöcken zu schneiden.
Schneidwerkstoffe und Verfahren – von der Kupferzeit bis ins 19. Jahrhundert
Die Kupferzeit ging vor etwa 5000 Jahren in die Bronzezeit über. Bronze, eine Legierung aus Kupfer und bis zu 10 Massenprozent Zinn, weist eine höhere Härte als Kupfer auf, die mit der Härte einfacher Stahlsorten vergleichbar ist. Das seit etwa 3000 Jahren in größeren Mengen verhüttete Eisen brachte bezüglich der Härte, das mit einem Wert von 4 auf der Mohs-Skala nur wenig härter als Kupfer ist, gegenüber Bronze keine Vorteile. Deshalb wurden auch Waffen, wie Schwerter und Speerspitzen, weiterhin aus Bronze und nicht aus Eisen gefertigt.
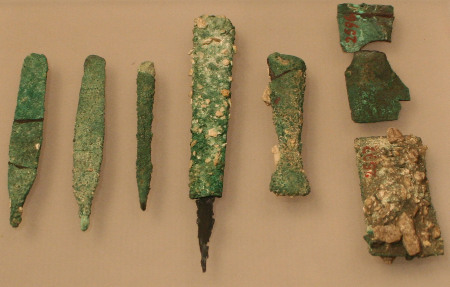
Auch mit Sägeblättern aus Eisen wurde weiterhin Sand benötigt, um Stein zu sägen, wie Plinius der Ältere (23 – 79) berichtete. Selbst in der ersten bekannten, durch Wasserkraft angetriebenen Steinsägemühle, die sich im antiken Griechenland in der Stadt Hierapolis befand und dort in der zweiten Hälfte des 3. Jahrhunderts vermutlich zum Sägen von Marmor verwendet wurde, kamen wahrscheinlich Eisenklingen und Sand zum Einsatz. Auch die später errichteten Steinsägemühlen benötigten weiterhin Sand als Schneidstoff.
Zum Sägen von Stein mithilfe von Sand oder anderen Abrasiven eignet sich jedoch weiches Eisen besser als Stahl, da sich die Schneidpartikel darin einbetten können und das Sägeblatt dadurch eine ausreichend stabile Schneidkante erhält. Derartige Schneidverfahren werden mancherorts auch heute noch genutzt.
Die erste gezielte und reproduzierbare Herstellung von Stahl gelang nach derzeitigem Erkenntnisstand vor etwa 2300 Jahren den Indern. Sie stellten einen Stahl mit einem Kohlenstoffgehalt von 1,3 bis 1,5 % her, den sogenannten Wootz-Stahl, aus dem unter anderem die Damaszenerklingen hergestellt wurden. Auch die Römer stellten Stahl her und nutzen diesen unter anderem für Nägel, Rüstungen und Waffen.
Stahl kann durch Abschrecken gehärtet werden. Wird er erhitzt, bis er rotglühend ist und dann in Wasser schnell abgekühlt, bildet sich anstelle des zuvor vorhandenen Austenits eine kohlenstoffhaltige, metastabile Eisenphase, das als Martensit bezeichnet wird und dem Metall eine größere Härte verleiht. In dem Maße, wie durch Tempern bei mehr als +200 °C der Martensitanteil abnimmt, verringert sich auch wieder die Härte des Stahls.
Bis in das 18. Jahrhundert hinein waren die hauptsächlich verwendeten und durch Schneiden zu bearbeitenden Werkstoffe im wesentlichen Holz und Stein, die keine sehr hohen Ansprüche an die Schneidverfahren stellten. Metalle wurden bis dahin meist in die gewünschte Form gegossen und vom Schmied mit dem Hammer auf dem Amboss nachbearbeitet, aber nur selten „in Form“ geschnitten.
Als Konstruktionsmaterial wurden Metalle erst in der zweiten Hälfte des 18. Jahrhunderts interessant, etwa zum Bau der ersten Dampfmaschinen. Große Mengen an Stahl wurden bald auch für den Bau von Brücken, Hochhäusern und anderen Bauwerken benötigt, wie beispielsweise für die Errichtung des Eiffelturms in den Jahren 1887 bis 1889. Er ist eine reine Stahlkonstruktion.
Durch die beim Schneidprozess auftretende Reibung steigt die Temperatur des Schneidstoffs, was beim gehärteten Stahl ab einer Temperatur von etwa +200 °C zur Umwandlung der inneren Struktur von Martensit zu Austenit führt. Dadurch wird der Stahl dauerhaft weicher, so dass er weniger gut schneidet und schneller verschleißt.
Stähle, die schon bei Temperaturen von +200 bis +300 °C ihre Härte verlieren, werden als Kaltarbeitsstähle bezeichnet. Sie finden heute nur noch für Handwerkzeuge und für die Holzbearbeitung Anwendung. Durch niedrigere Schnittgeschwindigkeiten wird die Erwärmung begrenzt und die Lebensdauer des Schneidstoffs erhöht, was aber die Produktivität begrenzt.
Stähle für anspruchsvolle Schneidanwendungen
1868 entdeckte der britische Metallurge Robert Mushet (1811 – 1891) eine Stahllegierung, welche neben Eisen und Kohlenstoff etwa 6 bis 10 % Wolfram, 1,2 bis 2 % Mangan und in einer weiterentwickelten Version zudem noch etwa 0,5 % Chrom enthielt. Dieser Stahl muss zur Härtung nicht in Wasser abgeschreckt werden. Er besitzt zudem bei höheren Temperaturen eine größere Härte als unlegierter Stahl, sodass damit höhere Schneidgeschwindigkeiten möglich wurden.
Im Jahr 1906 präsentierte der US-amerikanische Ingenieur Frederick W. Taylor (1856 – 1915) in einem Artikel mit dem Titel „On the Art of Cutting Metals“ die Ergebnisse systematischer Studien über Verfahren zum Metallschneiden während eines Zeitraums von 26 Jahren. Unter anderem berichtete er über die Entwicklung eines Schnellarbeitsstahls, der, wie der Name schon nahelegt, durch seine höhere Warmhärte deutlich höhere Schneidgeschwindigkeiten ermöglichte. Die hohe Härte bei Temperaturen bis etwa +600 °C ist auf die Ausscheidung sehr vieler kleiner Carbidkristalle in der Größenordnung von 50 nm im Stahl zurückzuführen, wodurch die relative Beweglichkeit der Atome in dem Stahl stark eingeschränkt wird. Der in dem Artikel vorgestellte Schnellarbeitsstahlstahl enthielt neben Eisen und etwa 2% Kohlenstoff, etwa 19 % Wolfram und 5 % Chrom, dazu noch Mangan und Vanadium. Später zeigte sich, dass die Hälfte des Wolframs durch das leichtere Molybdän ersetzt werden konnte, ohne die für den Einsatz als Schneidstoff wichtigen Eigenschaften des Materials zu verändern.
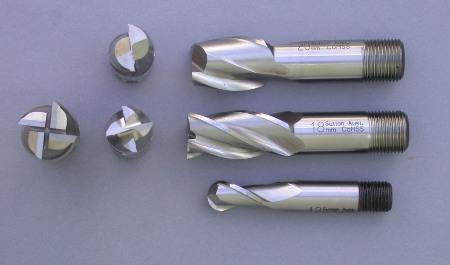
Bereits im Jahre 1900 erhielten Frederick W. Taylor und der amerikanische Metallurge J. Maunsel White III (1856 – 1912) die ersten Patente für Schnellarbeitsstähle. Im Laufe der Zeit wurde die Legierung weiter optimiert, wodurch die Härte und Kantenfestigkeit noch weiter verbessert werden konnten.
Moderne Schneidstoffe und Schneidverfahren
Schnellarbeitsstahl (engl.: High Speed Steel; HSS) wird noch bis heute als Schneidstoff für die Metallbearbeitung verwendet, wobei er oft mit einem mittels Gasphasenabscheidung aufgebrachten Hartstoff, wie Titannitrid oder Titancarbid, beschichtet ist, um den Verschleiß des Schneidstoffs zu verringern und die Qualität der Schnittflächen zu erhöhen.
Edelstähle, mit und ohne Beschichtung, finden auch Einsatz als Schneider, Sägen und Rohrtrenner. Mit solchen Schlauchabschneidern, Rohrsägen und Kapillar-Cuttern können Schläuche, Kunststoffrohre und sogar Kapillaren aus Edelstahl und Titan im Handumdrehen auf die jeweils benötigte Länge zugeschnitten werden. Sie dienen somit als wertvolles Hilfsmittel in der Fluidtechnik.
Um eine Überhitzung des Schneidstoffs und damit den Verlust von Härte und Festigkeit zu verhindern, werden bei mechanischen Schneidverfahren meist Kühlschmierstoffe eingesetzt, mit denen die Schneidwerkzeuge umspült werden. Sie führen die Wärme ab und verringern die Reibung, die zusätzliche Wärme und Verschleiß generiert.
Ein sehr effektives Kühlmittel ist Wasser, allerdings fördert es die Korrosion von Schneid- wie Werkstoff und ist auch kein guter Schmierstoff. Daher werden Emulsionen aus Wasser und Öl verwendet. Hinzu kommen noch Additive, um Schaumbildung, Korrosion, Benetzung und andere Eigenschaften einzustellen. Bei Schneidprozessen, bei denen eine effektive Schmierwirkung wichtiger ist als die Kühlwirkung, werden Kühlschmierstoffe auf der Basis von Mineralöl verwendet. Bei der Zuleitung und automatischen Dosierung von Kühlschmiermitteln ist darauf zu achten, ein chemisch beständiges Schlauchmaterial für die Leitungen zu wählen. Für Schmiermittel auf Mineralöl-Basis empfehlen sich Schläuche aus NBR (Acrylnitril-Butadien-Kautschuk).
Kühlschmiermittel, von denen sich einige als gesundheitsgefährdend herausgestellt haben, müssen nach längerer Verwendung entsorgt werden. Der Verzicht auf solche Schmiermittel oder zumindest eine Verringerung ihres Verbrauchs sind somit wünschenswert. Ein Weg, um dieses Ziel zu erreichen, ist das trockene Schneiden von Werkstoffen, wofür jedoch Schneidstoffe benötigt werden, die auch bei hohen Temperaturen ihre Festigkeit und Härte beibehalten. Hierfür kommen Hartmetalle, keramische Schneidstoffe oder Diamant in Frage. Dabei sind nicht das gesamte Sägeblatt oder der Bohrer aus diesem Material, sondern nur die Schneidklingen, die in Kontakt mit dem Werkstück kommen. Alle übrigen Teile des Werkzeugs bestehen aus Stahl.
Hartmetalle bestehen aus sehr festen und chemisch stabilen Carbiden, wie beispielsweise Wolframcarbid oder Titan- und Tantalcarbid, die in einer weichen Metallmatrix, meist aus Kobalt oder Nickel, eingebettet sind. Der Volumenanteil der Carbide liegt bei 80 bis 95 %. Ein solches Gefüge wurde 1923 vom deutschen Chemiker Karl Schroeter (1885 – ?) zum Patent angemeldet. Hartmetalle fanden bereits seit Anfang der 1930er Jahre ihre Anwendung als Schneidstoff und waren im Bereich der Schneidverfahren für Metalle ähnlich revolutionär wie zuvor die Einführung des Schnellarbeitsstahls.
Auch bei Hartmetallschneidstoffen kann eine mittels Gasphasenabscheidung aufgebrachte Beschichtung aus Titancarbid oder Titannitrid die Oberflächenhärte erhöhen, ohne die Zähigkeit des Werkstoffs zu mindern, so dass ein geringerer Verschleiß erreicht wird. Wie auch beim Schnellarbeitsstahl ist die Verkleinerung der Kristallitgröße ein Weg zu größerer Härte und Erhöhung der Zähigkeit des Materials.
Keramische Schneidstoffe und andere Hochtemperatur-Schneidstoffe
Die besonders harten keramische Schneidstoffe, wie Korund, werden hauptsächlich zum Schneiden sehr harter und hochschmelzender Materialien verwendet, etwa von hochwarmfesten Superlegierungen. Dem Korund wird meist noch etwas Zirkondioxid beigemischt, um ein feinkörnigeres und damit homogeneres und stabileres Material zu erhalten.
Korund behält seine Härte bis +2000 °C bei. Durch Zumischung von Titancarbid oder Titannitrid kann damit sogar bis +2500 °C gearbeitet werden. Andere Keramiken, wie Siliziumnitrid, bleiben bei noch höheren Temperaturen einsatzfähig. Die höchste Härte besitzt mit einer Mohshärte von 10 zwar der Diamant, der in Luft jedoch bei Temperaturen über +600 °C verbrennt. Bei Abwesenheit von Sauerstoff und Temperaturen über +1500 °C wandelt er sich in den thermodynamisch stabileren, weichen Graphit um. Zudem würde beim Schneiden von Eisenwerkstoffen eine Übertragung von Kohlenstoff auf das Werkstück erfolgen und der Diamantschneidstoff schnell verbraucht sein. Eine etwas geringere Härte, welche allerdings bis zu einer Temperatur von +2000 °C erhalten bleibt, besitzt Bornitrid.
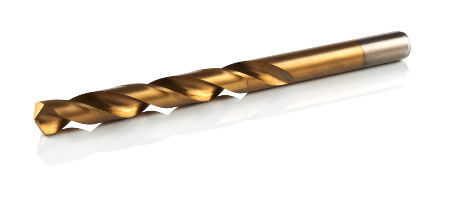
Der Nachteil dieser sehr harten Materialien ist deren große Sprödigkeit, so dass solche Schneidwerkzeuge störanfällig sind. Daher werden heute für die meisten Anwendungen mit Hartkeramik beschichtete Schneidstoffe verwendet. Dank vieler Verbesserungen der Materialkomposition wie auch der Prozessführung beim Schneiden nimmt der Anteil der Schneidkeramiken an den industriell verwendeten Schneidstoffen zu, da sie höhere Arbeitsgeschwindigkeiten und bessere Schnittqualitäten bieten.
Nicht jeder Werkstoff kann mit jedem Schneidstoff bearbeitet werden. Schneidstoffe aus Nitridkeramiken sind für die Bearbeitung von Eisen ungeeignet, während aluminium-, titan- und magnesiumhaltige Werkstoffe nicht mit aluminiumhaltigen Schneidstoffen, wie Korund, geschnitten werden können. Das Schneiden von metallhaltigen Werkstoffen, die hart oder hochschmelzend sind, kann somit eine Herausforderung bei der Wahl des geeigneten Schneidstoffs bedeuten.
Kontaktlose Schneidverfahren: Laserschneiden
Ein gänzlich anderer Verfahrensansatz besteht darin, das Material an der Schneidstelle zu schmelzen oder zu verdampfen, wie das beim Plasmaschneiden realisiert wird. Bei diesem thermischen Schneidverfahren wird ein auf das Werkstück gerichteter, dünner Gasstrahl durch einen Lichtbogen auf Temperaturen von mehreren Tausend Grad Celsius erhitzt, sodass das Material an der getroffenen Stelle schmilzt und sogleich auch verdampft. Durch die sehr hohe Temperatur ist die Trennung jeglichen Materials möglich.
Ein anderes, deutlich präziseres thermisches Schneidverfahren ist das Laserschneiden. Hiermit werden Schneidfugen erreicht, die schmaler als ein Millimeter sind. Die Wärmebelastung des Werkstücks bleibt dabei gering, sodass es kaum zu thermisch induzierten Veränderungen kommt.
Dadurch kann Laserstrahlung, anders als das Licht polychromer Lichtquellen, vollständig auf einen Punkt fokussiert werden. Somit kann sehr viel Strahlungsenergie auf eine sehr kleine Fläche gerichtet werden, wodurch es unter der Voraussetzung, dass das Material die Strahlung absorbiert, zu einer extrem schnellen und starken Erwärmung an der betreffenden Stelle kommt.
Üblicherweise werden zum Schneiden CO2-Laser verwendet, die sehr hohe Energien bereitstellen und zudem besonders wirtschaftlich sind. Diese Art Laser emittiert Infrarotlaserstrahlung mit einer Wellenlänge von 10,6 Mikrometern (oder 10600 nm). Zunehmend finden aber auch Festkörperlaser, wie Nedoydm- oder Ytterbium-dotierte Yttrium-Aluminium-Granat-Laser (Nd:YAG- oder Yb:YAG-Laser) Anwendung, die eine Laserstrahlung mit Wellenlängen von 1064 nm und 1030 nm emittieren. Diese Festkörperlaser sind, sofern sie mit Diodenlasern gepumpt werden, energieeffizienter als CO2-Laser.
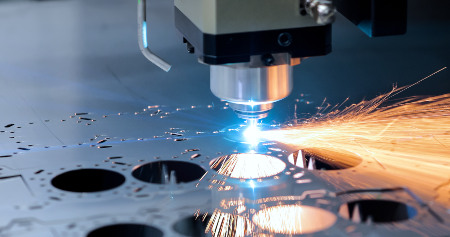
Um mit Laserstrahlung ein Material zu schmelzen, muss es die Strahlungsenergie möglichst vollständig aufnehmen. Während viele Materialien, wie Keramiken und Kunststoffe, die Infrarotstrahlung von CO2– und Nd:YAG-Lasern stark absorbieren, zeigen Metalle dafür meist nur ein geringes Absorptionsvermögen. Metalle absorbieren vor allem im kurzwelligen Bereich, so dass Excimer-Laser zum Schmelzen von Metallen geeigneter zu sein scheinen. Excimer-Laser haben jedoch einen deutlich geringeren Wirkungsgrad als Nd:YAG, Yb:YAG- und CO2-Laser und können zudem auch nur gepulst betrieben werden, was durch die niedrigere Energiedeposition pro Zeiteinheit zu niedrigeren Arbeitsgeschwindigkeiten führt. Wegen des geringeren Wirkungsgrads der Excimer-Laser werden CO2-Laser und Nd:YAK-Laser nach wie vor zum Schneiden von Metallen eingesetzt. In der HPLC- und Analysentechnik findet das Verfahren Einsatz, um Edelstahl-Kapillaren und Titan-Kapillaren gratfrei und sauber zuzuschneiden.
Eisen und Stahl weisen auch bei 10,6 Mikrometern Wellenlänge immer noch eine Absorption im Bereich von 5 bis 10 % auf, so dass die Verwendung von CO2-Lasern weitgehend unproblematisch ist, während beispielsweise Kupfer die Strahlung nahezu vollständig reflektiert. Deshalb werden für das Schneiden von Kupfer meist die kurzwelligeren Nd:YAG-Laser eingesetzt.
Die Absorption von Laserstrahlung hängt stark von der Intensität der Strahlung ab. Bei hohen Intensitäten steigt die Absorption, wobei auch bei nur geringer Absorption Oberflächenmaterial verdampft wird. Mit der Verdampfung werden Elektronen freigesetzt, die die Laserstrahlung über den Prozess der „Inversen Bremsstrahlung“ besonders gut absorbieren und die Energie auf den Werkstoff übertragen. Dies führt zu einem schnellen und starken Temperaturanstieg, bis sich letztlich ein Plasma bildet, welches nahezu 100 % der Strahlung absorbiert. Die Verwendung hochintensiver Laser ermöglicht somit das Schmelzen von Materialien mit Lichtwellenlängen, die bei niedrigen Intensitäten nahezu vollständig reflektiert werden.
Der Laserschneidkopf besteht aus einer Linsen- oder Spiegelanordnung, die den Laserstrahl fokussiert, und einer Gasdüse, welche koaxial zur Ausbreitungsrichtung des Laserstrahls angeordnet ist. Durch die Gasdüse wird beim Schmelzschneiden ein Intertgas gedrückt, welches das durch den Laser geschmolzene Material heraus bläst.
Beim Brennschneiden wird Sauerstoff statt des Inertgases verwendet, wodurch die Oxidation des zu schneidenden Materials zu seiner Erwärmung beiträgt, sofern dieses, wie es für die meisten Metalle der Fall ist, mit Sauerstoff exotherm reagiert. Auf diese Weise ermöglicht dieses Schneidverfahren bei geringerer Laserleistung trotzdem höhere Schneidgeschwindigkeiten, allerdings zu dem Preis, dass die Schnittkanten des Materials dabei oxidiert werden.
Das Laserschneiden wird vor allem für Metallplatten und Bleche sowie andere flächige Materialien verwendet. Das mechanische Schneiden derartiger Werkstücke führt leicht zu unvorhersehbaren Verformungen, Rissbildung, dem Aufbau mechanischer Spannungen und thermisch bedingten Veränderungen der Materialeigenschaften, was mittels Laserschneidens meist vermieden werden kann.
Beim Laserschmelzschneiden kann zudem oftmals die Nachbearbeitung der Schnittkanten entfallen, da diese hinreichend glatt und sauber sind. Trotzdem kann auch Laserschneiden durch die starke Erhitzung Materialschäden verursachen, außerdem stellt das verdampfte Material ein erhebliches Gesundheitsrisiko für die Bearbeiter dar, das besondere Arbeitsschutzmaßnahmen erfordert.
Wasserstrahlschneiden
Eine schlechte Strahlenabsorption kann den Schneidprozess mit Lasern ineffizient machen. Für derartige Fälle bietet sich ein anderes kontaktloses Schneidverfahren an: das Wasserstrahlschneiden.
Da diese Düse extremen Belastungen standhalten muss, besteht sie aus sehr harten Materialien, wie Rubin oder Diamant. Die hohe Geschwindigkeit des Wasserstrahls wird durch den Aufbau von Wasserdrücken von mehreren tausend Bar ermöglicht, wofür spezielle Pumpen und Druckverstärker verwendet werden.
Das erste Patent für das Wasserstrahlschneiden wurde 1956 von Carl O. Johnson eingereicht, dessen Biographie nicht überliefert ist. Das Verfahren sollte gemäß der Patentschrift dem Trennen von noch nicht ausgehärteten Porenbetonblöcken dienen. 1958 reichte Billie G. Schwacha, für den ebenfalls keine biographischen Daten überliefert sind, ein Patent zum abrasiven Flüssigkeitsstrahlschneiden ein. Sein Patent beschreibt ein Verfahren für besonders harte, mechanisch schwer zu schneidende Metalllegierungen, die mittels eines überschallschnellen Flüssigkeitsstrahls aus Mineralöl oder Wasser und einem Abrasiv, wie Korundpulver, geschnitten werden können. Das Wasserstrahlschneiden fand jedoch erst Anfang der 1970er Jahre Anwendung in der Industrie.
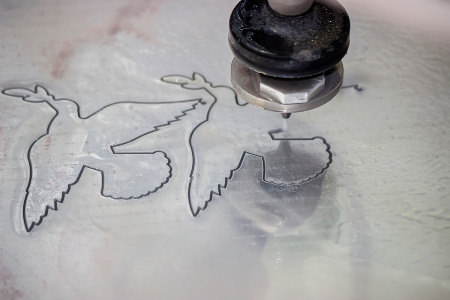
Mit reinem Wasser lassen sich unter anderem Pappe, Holz, Kunststoffe und Faserverbundstoffe schneiden. Halbzeuge aus Kunststoffen, wie Kunststoff-Platten und Gummimatten, werden mit diesem Verfahren zugeschnitten. Auch andere Kunststoff-Fertigteile, wie Flachdichtungen und andere Dichtungen nach Zeichnung, werden mittels Wasserstrahl in Form gebracht.
Für höhere Schneidgeschwindigkeiten oder schmalere Schnittfugen kann dem Wasser ein langkettiges Polymer, wie Polyethlyenglycol, zugefügt werden, welches zu einer schärferen Bündelung des Wasserstrahls nach Austritt aus der Düse führt. Der Schneidmechanismus ist bisher nur teilweise verstanden. Als gesichert gilt, dass die stark lokalisierte, hohe Auftreffgeschwindigkeit des Wassers zu hohen Drücken auf der Werkstückoberfläche führt, was zu dessen Deformation und schließlich zur lokalen Abtragung oder direkt zur Perforation führt.
Zum Wasserstrahlschneiden von Metallen, Glas, hartem Gestein und Keramik müssen dem Wasserstrahl noch Abrasive beigemischt werden. Als Abrasive werden feine Partikel aus Glas, Gesteinen, Metallen oder Hartkeramiken eingesetzt. Dabei kann das Abrasiv entweder vor dem Austritt aus der Düse dem Wasser beigefügt werden oder nach dessen Austritt in einer Mischkammer mit Luft vermischt vom Wasserstrahl aufgenommen werden.
Das ASWJ ist effizienter und benötigt weniger hohe Drücke als das AWJ, da die Partikel direkt mit dem Wasser beschleunigt werden und damit höhere Endgeschwindigkeiten als im Falle des AWJs erreichen. Allerdings verschleißt bei diesem Verfahren die Düse schneller und die Schaltzeiten sind erheblich länger als beim AWJ, was dessen Anwendungsmöglichkeiten einschränkt. Deshalb werden zumeist AWJ-Systeme genutzt.
ASWJ-Systeme werden für Schneidarbeiten eingesetzt, bei denen sehr lange Schnitte ausgeführt werden oder für Arbeiten, bei denen der Ausschluss von Luft erforderlich ist, wie beispielsweise dem Schneiden von Explosivstoffen.
Der Schneidprozess basiert beim abrasiven Wasserstrahlschneiden auf dem Aufprall der Abrasivpartikel mit extrem hoher Geschwindigkeit, der zu einer schnellen Erosion des Werkstoffes führt. Mittels Wasserstrahlschneiden ist das Trennen von Werkstoffen fast jeglichen Materials mit hoher Präzision möglich, ohne dass es sich dabei erhitzt, was insbesondere beim Schneiden von Kunststoffen, Papier, Pappe und Holz vorteilhaft ist. Empfindliche Bauteile, wie beispielsweise Leiterplatten, werden mittels Wasserstrahl schonend geschnitten. Mechanische Verfahren würden hier leicht zu Mikrorissen, Abblätterungen der Kupferkaschierungen oder anderen Beschädigungen führen. Das Wasserstrahlschneiden ist zudem ein sehr staubarmer Schneidprozess, was besonders beim Schneiden von faserverstärkten Kunststoffen, Keramiken und Gesteinen dem Gesundheitsschutz dienlich ist.
Zukunftstrends
Bei mechanischen Trenn- und Schneidverfahren werden absehbar verstärkt Hartkeramiken eingesetzt, um die Standzeit der Schneidstoffe und die Qualität der Schnittflächen zu erhöhen. Damit scheint allmählich das Zeitalter der metallischen Schneidstoffe zu enden.
Beim Laserschneiden sind insbesondere die Energieeffizienz und die Anschaffungskosten wichtige Faktoren, da hier mechanische Systeme oftmals günstiger sein können. Bezüglich des Lasertyps versprechen Hochleistungsdiodenlaser, die zunehmend verfügbar werden, in der Zukunft die gängigen Lasersysteme abzulösen. Bei diesem sehr kompakten Lasertyp kann die Wellenlänge mit hoher Präzision eingestellt und somit auf das zu bearbeitende Material abgestimmt werden.
Um die thermische Belastung des Werkstücks weiter zu verringern und die Entwicklung giftiger Dämpfe zu reduzieren, gibt es erste Versuche, Schneidlaser mit einem Wasserstrahl zu kombinieren. Der Wasserstrahl dient dabei zudem als Leitmedium für das Laserlicht, das wie in einer Glasfaser durch Totalreflektion innerhalb des Wasserstrahls zum Werkstück geleitet wird.
Beim Wasserstrahlschneiden wird versucht, durch höhere Drücke und somit höheren Strahlgeschwindigkeiten sowie der Verwendung von beschleunigten Tropfen statt eines kontinuierlichen Wasserstrahls auf Abrasive verzichten zu können. Darüber hinaus wäre der Umstieg auf ASWJ-Systeme durch die niedrigeren Arbeitsdrücke vorteilhaft.
An Lösungen zur Reduzierung der langen Schaltzeiten sowie zur Erhöhung der Düsenstandzeiten wird gearbeitet. Denkbar ist, dass langfristig der 3D-Druck die trennende Materialbearbeitung zumindest in einigen Bereichen ersetzen könnte, indem komplizierte Bauteile direkt und maßgerecht generiert werden – so, wie es uns die Natur zeigt, die imstande ist, komplexe Systeme, wie Knochen, Federn oder Blätter und Blüten Molekül für Molekül passgenau aufzubauen.
Quellen: Florian Neukirchen, Von der Kupfersteinzeit zu den Seltenen Erden: Eine kurze Geschichte der Metalle, Springer-Verlag, Berlin Heidelberg, 2016 Klaus Grewe, Die Reliefdastellung einer antiken Steinsägemaschine aus Hierapolis in Phrygien und ihre Bedeutung für die Technikgeschichte in: M. Bachmann, Hrsg., Bautechnik im antiken und vorantiken Kleinasien, BYZAS 9, 2009 Edward Trent, Paul Wright, Metal Cutting, 4th Edition, Butterworkt-Heinemann, 2000 Birgit Awiszus, Jürgen Bast, Thomas Hänel, Mario Kusch (Hrsg.), Grundlagen der Fertigungstechnik, Carl Hanser Verlag, München, 2020 W. Taylor, On The Art Of Cutting Metals, The American Society of Mechanical Engineers, New York, 1906 Herbert Schönherr, Spanende Fertigung, Oldenbourg, München, Wien, 2002 F. C. Sousa, F. J. G. Silva, Recent Advances on Coated Milling Tool Technology - A Comprehensive Review, Coatings 10, 235, 2020 N. Grigoriev, S. V. Fedorov, K. Hamdy, Materials, properties, manufacturing methods and cutting performance of innovative ceramic cutting tools - a review, Manuf. Rev. 6, 19, 2019 Bernd K. Engemann, Schneiden mit Laserstrahlung und Wasserstrahl: Anwendungen, Erfahrungen, Ausblick, expert Verlag, Ehningen bei Böblingen, 1993 Helmut Hügel, Thomas Graf, Laser in der Fertigung: Grundlagen der Strahlquellen, Systeme, Fertigungsverfahren, Springer Fachmedien, Wiesbaden, 2014 David A. Summers, Waterjetting Technology, Alden Press, Oxford, 1995 Molitoris, J. Pitel, A. Hosovky, M. Tothova, K. Zidek, A Review of Research on Water Jet with Slurry Injection, Procedia Eng. 149, 333, 2016 M. Tabie, M. O. Koranteng, A. Yunus, F. Kuuyine, Water-Jet Guided Laser Cutting Technology- an Overview, Lasers Manuf. Mater. Process. 6, 189, 2019 R. Mitchell, S. A. R. Demian, Y. P. Korkolis, B. L. Kinsey, Experimental comparison of material removal rates in abrasive waterjet cutting and a novel droplet stream technique, Proceida Manuf. 48, 586, 2020
Bildquellen: Beitragsbild | © romankrykh – stock.adobe.com Steinzeitliche Sägewerkzeuge | © public domain (PD) via Wikimedia Commons Neolithische Meißel aus Stein | © Bullenwächter, CC BY 3.0 <https://creativecommons.org/licenses/by/3.0>, via Wikimedia Commons, Dateigröße geändert Undatierte Kupferwerkzeuge, Fundort Gizeh | © Einsamer Schütze, CC BY-SA 3.0 <https://creativecommons.org/licenses/by-sa/3.0>, via Wikimedia Commons, Dateigröße geändert Schaftfräser aus unbeschichtetem Schnellarbeitsstah | © Photograph taken by Glenn McKechnie on the 26th March 2005. <https://creativecommons.org/licenses/by-sa/2.0/deed.de>, via Wikimedia Commons Bohrer mit Beschichtung aus Titannitrid (TiN) | © Олег – stock.adobe.com Metallblech wird mittels CNC-Laser zugeschnitten | © rul8let – stock.adobe.com Aluminium-Platte bei der Bearbeitung mittels Wasserstrahlschneiden | © kalpis – stock.adobe.com