Der Anteil der Kunststoffe, die in der Medizinbranche eingesetzt wird, beträgt nur etwa 2 Prozent der gesamten produzierten Kunststoffmenge. Trotz des niedrigen Anteils am Gesamtverbrauch haben sich Kunststoffe in der Medizin und Medizintechnik als wichtige Materialien etabliert. Sie besitzen ein geringes Gewicht, sind Röntgen- und MRT-tauglich, physiologisch unbedenklich, sterilisierbar, preisgünstig, stabil und bruchsicher. Zudem können sie präzise, in großer Stückzahl und hoher Qualität in verschiedenen Farben und komplexen Geometrien gefertigt werden.
Geeignete Kunststoffe werden beispielsweise zu Löffeln und Spatel, Probenbehältern und Präparatedosen, Einweg-Spritzen und Luer-Lock-Verbindern verarbeitet und in der Medizintechnik eingesetzt. Auch weiche Schläuche, beispielsweise Silikonschläuche oder Schläuche aus thermoplastischen Elastomeren, kommen als Schlauchleitungen zum Einsatz, sei es für Infusionen oder zur künstlichen Beatmung.
Anforderungen an medizinische Kunststoffe
Kunststoffe in der Medizin und Medizintechnik müssen in reinster Form, oft unter Reinraumbedingungen zum Medizinprodukt verarbeitet und anschließend sterilisiert werden.
Medizinische Kunststoffe werden nach Anwendung und Zeitdauer in jeweils drei Klassen eingeteilt: Medizinprodukte, die nur in Kontakt zur Körperoberfläche kommen wie zum Beispiel Verbandsmaterial oder Kontaktlinsen, solche, die von außen mit dem Körperinneren Kontakt haben wie Einwegspritzen, Nahtmaterial oder Katheter und schließlich Implantate wie künstliche Gelenke, Herzklappen oder Silikonimplantate. Diese Klassen werden weiter unterteilt nach der Verweildauer des Medizinprodukts im Körper. Das kürzeste Intervall beträgt weniger als 24 Stunden, die mittlere Zeitdauer zwischen 24 Stunden und 30 Tagen und dauerhaft, wenn das Medizinprodukt länger als 30 Tage im Körper verbleibt.
Wichtige Regelwerke für Kunststoffprodukte in der Medizin
Kunststoffproduzenten müssen die Norm USP Class VI oder ISO 10993 erfüllen, um die Biokompatibilität ihrer Produkte zu garantieren. USP ist die Abkürzung für United States Pharmacopeia, eine gemeinnützige Organisation, die Standards für die Qualität und Sicherheit von Medizinprodukten, Arznei- und Lebensmittel festlegt. Die USP Class VI ist die strengste und beinhaltet Tests zur Bestimmung der akuten systemischen Toxizität, der intrakutanen Reaktivität sowie Implantationstests.
Die Norm ISO 10993, in Deutschland als DIN EN ISO 10993 veröffentlicht, stellt strengere Anforderungen an die Zulassung. Sie fordert neben biologischen Tests auch physikalisch-chemische Prüfungen und Analysen von Ausgangsstoffen und gelösten Stoffen und gibt Grenzwerte für herauslösbare Stoffe vor.
Die VDI-Richtlinie 2017 dient ebenfalls als wichtiger Leitfaden Medizinproduktehersteller. Sie beschreibt den Begriff „Medical Grade Plastics“ und welche Eigenschaften und Anforderungen an Kunststoffe für den Einsatz in der Medizin und Medizintechnik gestellt werden. Die Anwendung der Richtlinie unterstützt dabei, die Qualität, Konstanz der Rezeptur, Biokompatibilität und Liefersicherheit zu gewährleisten. Durch die Richtlinie werden die Bereiche Entwicklung, Logistik, Beschaffung und Einkauf gleichermaßen erfasst.[1]
Welche Kunststoffe werden in der Medizin verwendet?
Die Massenkunststoffe PE, PP und PVC
Die Polyolefine Polyethylen (PE) und Polypropylen (PP) gelten als physiologisch unbedenklich und biokompatibel und enthalten keine Weichmacher. Kunststoffschläuche aus PE und PP sind durchsichtig, flexibel und besitzen eine gute Chemikalienbeständigkeit.
Polypropylen findet Anwendung als Verpackungen für feste und flüssige pharmazeutische Produkte, Einwegspritzen, Laborbehälter, Infusionsbesteck, Membrane für Oxygenatoren, Herzklappenprothesen und Nahtmaterial. Netze aus Polypropylen werden in der Hernienchirurgie eingesetzt.
Polyvinylchlorid (PVC) zeichnet sich durch eine hohe Transparenz, glatte Oberfläche, gute Knickbeständigkeit, gute physiologischen Eigenschaften und geringe Produktionskosten aus. Aus weichem Polyvinylchlorid werden Beutel, Handschuhe und weiche Schläuche, beispielsweise für Infusionslösungen, Blut und Urin, gefertigt.
Weich-PVC ist jedoch umstritten, da es Weichmacher wie Diethylhexylphthalat (DEHP) enthält, die nicht chemisch gebunden sind und aus dem Material migrieren können. DEHP gilt als fortpflanzungsschädigend und wurde in Kinderspielzeug und Kosmetika verboten. Für die Medizintechnik wurde Tri-(2-ethylhexyl)trimellitat (TEHTM, TOTM) als Ersatz für DEHP entwickelt. Hart-PVC wird als sterilisierbare Verkleidung von medizinischen Geräten verwendet.
Silikonkautschuk und PTFE
Polysiloxane, organische Silicium-Verbindungen, sind temperaturbeständig in einem Bereich von -70 °C bis +250 °C, manche Formulierungen sogar bis +300 °C. Silikonkautschuke zeichnen sich durch eine sehr gute Biokompatibilität und hervorragende elastische Eigenschaften aus, lassen sich gut sterilisieren und enthalten keine Weichmacher. In der Medizintechnik werden sie zur Herstellung von Pumpenschläuchen und Beatmungsschläuchen, Beatmungsmasken, Dichtungen, Handschienen und Fußeinlagen verwendet. In der Medizin finden sie Anwendung als Implantate, Herzschrittmacher, Herzklappen, Katheter und Drainageschläuche. In der Zahnmedizin dienen sie zur Abformung von Zahnreihen und Kiefer, um Präzisionsmodelle herzustellen.
Polytetrafluorethylen (PTFE), auch unter dem Handelsnamen Teflon® der Fa. DuPont bekannt, besitzt eine außergewöhnlich niedrige Oberflächenspannung und verhindert dadurch die Bildung von Thromben. Aus diesem medizinischen Kunststoff werden Gefäßprothesen, Gehörknöchelchen, Harnleiterprothesen und Medizinschläuche hergestellt. Wegen seiner ausgezeichneten Gleiteigenschaften kommt es auch als Beschichtungsmaterial für Katheter, Kanülen und Injektionsnadeln zum Einsatz.
Polystyrol und PMMA
Polystyrol (PS) wird in der Medizintechnik als transparenter Kunststoff für Zellkultur- und Petrischalen oder Behälter für infektiöse oder toxische Materialien sowie als Verpackungsmaterial geschätzt. Expandiertes Polystyrol (EPS), besser bekannt unter dem Handelsnamen Styropor®, dient als Transportbehälter für gekühlte Medikamente und Impfseren.
In der Zahnheilkunde spielt Polymethylmethacrylat (PMMA), besser bekannt unter dem Handelsnamen Plexiglas® der Fa. Röhm GmbH, eine wichtige Rolle bei der Herstellung von Prothesen, Abdrucklöffeln und Kronen. In der Endoprothetik wird der medizinische Kunststoff als Knochenzement verwendet. In den 1950er Jahren wurden die ersten Kontaktlinsen aus PMMA hergestellt. Da dieses Material für Sauerstoff undurchlässig ist, werden heute für harte Kontaktlinsen Silikonpolymere verwendet.
Biologisch abbaubare Kunststoffe
Eine andere Gruppe von Kunststoffen in der Medizin sind biologisch abbaubare Kunststoffe, auch bioresorbierbar genannt, die nach einer bestimmten Zeit im Körper abgebaut werden. Zu diesen medizinischen Kunststoffen gehören Polymilchsäure (PLA, engl.: Poly lactid acid), Polyglykolsäure und Polydioxanon. Sie sind Ausgangsmaterialien bei der Herstellung von Gefäßwandstützen (Stents), Wundklammern, Implantate wie Platten und Schrauben zur Gewebe- und Knochenfixation sowie Nahtmaterial. Durch den Einsatz dieser Biokunststoffe kann auf eine zweite Operation zur Entfernung der Implantate verzichtet werden.
Welche Sterilisationsverfahren für welche Medizinprodukte
Ob Einweg- oder Mehrwegprodukte, medizinische Kunststoffteile müssen sterilisiert werden. Als Sterilisationsverfahren werden Dampf-, Heißluft, Strahlen-, Plasma und Gassterilisation eingesetzt.
Dampf- und Heißluftsterilisation – Das Autoklavieren von Kunststoffen
Bei der Dampfsterilisation, auch Autoklavieren genannt, werden die zu sterilisierenden Teile bei einem Druck von etwa 2 bar und Temperaturen zwischen +121 °C und +134 °C erhitzt. Die Dampfsterilisation ist für viele medizinische Kunststoffe geeignet.
Bei der Heißluftsterilisation werden die Kunststoffteile über einen definierten Zeitraum auf hohe Temperatur erhitzt. Übliche Intervalle sind 2 Stunden bei +160 °C, 60 Minuten bei +170 °C und 30 Minuten bei +180 °C. Dieses Verfahren kann jedoch nur bei temperaturbeständigen Hochleistungskunststoffen wie zum Beispiel Polyetheretherketon (PEEK), Silikonkautschuk, Polysulfonen, oder Polyetherimide (PEI) angewendet werden.
Strahlen- und Plasmasterilisation
Beim Sterilisieren mit Strahlung wird Beta- oder Gamma-Strahlung eingesetzt. Die Strahlung hinterlässt keine Rückstände, kann jedoch die Polymerstruktur verändern. Dieses Verfahren ist für Polyethylen und Polysiloxane geeignet, andere Kunststoffe wie Polypropylen, Polyvinylchlorid oder Polyoxymethylen können jedoch vergilben und verspröden. Strahlensterilisation wird fast ausschließlich bei Einwegprodukten eingesetzt.
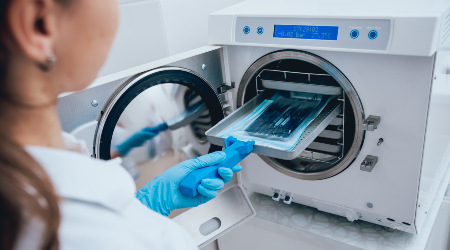
Die Plasmasterilisation erfolgt bei niedrigem Druck in einer Vakuumkammer bei Temperaturen zwischen +50 °C und +60 °C. Zusätzlich kann dampfförmiges Wasserstoffperoxid (H2O2) eingeleitet werden, das ebenfalls eine sterilisierende Wirkung hat. Da dieses Verfahren bei niedrigen Temperaturen durchgeführt wird, ist es für fast alle Polymere geeignet, die vakuumtauglich sind und nicht ausgasen.
Sterilisation mittels Ethylenoxid
Bei der Sterilisation mit Ethylenoxid werden die Medizinprodukte in einer abgedichteten Kammer bei Temperaturen zwischen +45 °C und +55 °C gasförmigem Ethylenoxid ausgesetzt. Überschüssiges Ethylenoxid wird während einer Belüftungsphase entfernt. Da Ethylenoxid toxisch ist, müssen die Produkte nach der Sterilisation auf Rückstände überprüft werden. Aufgrund der niedrigen Prozesstemperatur ist diese Methode für viele Polymere geeignet.
Polymere haben seit den 60er Jahren vor allem als Einwegprodukte Einzug in die Medizin gehalten. Als leichte, stabile, hygienische und preisgünstige Produkte ersetzten sie Glas und Metall. Im Laufe der Zeit etablierten sie sich in vielen verschiedenen Bereichen der Medizin wie zum Beispiel als Orthesen, Prothesen, Implantate und Kapseln zur Dosierung von Medikamenten. Aber auch als Mehrwegprodukte, die mehrfach sterilisiert und wiederverwendet werden können, sind Kunststoffprodukte gefragt.
Quellen: [1]: https://www.vdi.de/richtlinien/details/vdi-2017-medical-grade-plastics-mgp-1
Bild-Quellen: Beitragsbild | © angellodeco – stock.adobe.com Autoklav zur Dampfsterilisation | © romaset – stock.adobe.com