Die Herstellung von Kunststoffen hat das letzte Jahrhundert entscheidend verändert, viele unserer alltäglichen Gegenstände bestehen heute aus polymeren Werkstoffen. Die wirtschaftliche Kunststoffherstellung wurde erst durch die Entwicklung katalytischer Prozesse ermöglicht. In der chemischen Industrie werden mehr als 80 % aller Produkte mit Hilfe von Katalysatoren hergestellt. Katalyse spielt aber auch bei biochemischen Prozessen in lebenden Zellen, der Reduktion von Emissionen und für die Welternährung eine bedeutende Rolle.
Geschichte
Der Begriff Katalysator wurde bereits 1835 von dem schwedischen Mediziner und Chemiker Jöns Jacob Berzelius (1779 – 1848) in die Chemie eingeführt. Berzelius definierte Katalysatoren als verborgene Kraft, deren bloße Gegenwart chemische Tätigkeiten herrufen, die ohne sie nicht stattfinden.
1894 beschäftigte sich der deutschbaltische Wissenschaftler Friedrich Wilhelm Ostwald (1853 – 1932) mit katalytischen Vorgängen und stellte folgende Lehrsätze auf:
Für seine Arbeiten auf dem Gebiet der katalytischen Chemie und seine grundlegenden Untersuchungen über chemische Gleichgewichtsverhältnisse und Reaktionsgeschwindigkeiten erhielt er 1909 den Nobelpreis. Er entwickelte auch ein großtechnisches Verfahren zur Herstellung von Salpetersäure aus Ammoniak, Sauerstoff und Wasser an Platin-Netzen, das als Ostwald-Verfahren benannt wurde.
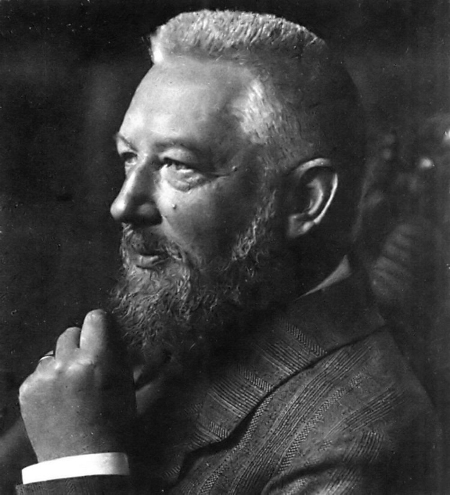
Seine Arbeiten stellten auch die Grundlage dar für das im Jahr 1910 entwickelte Verfahren von Fritz Jakob Haber (1868 – 1934) und Carl Bosch (1874 – 1940) zur Ammoniaksynthese. In dem nach ihnen benannten Haber-Bosch-Verfahren wird Ammoniak aus den Elementen Stickstoff und Wasserstoff an Eisen-Kontakten hergestellt. Ein Verfahren mit dem auch heute noch der größte Teil der weltweiten Ammoniakmenge produziert wird. Ammoniak ist ein wichtiges Ausgangsprodukt für die Herstellung von Harnstoff, Ammoniumnitrat, -sulfat und -phosphat, die als Düngemittel verwendet werden, sowie für die Herstellung von Sprengstoffen und anderen stickstoffhaltigen Chemikalien. Damit war das Deutsche Reich nicht mehr auf Salpeterlieferungen aus chilenischen Minen angewiesen. Fritz Haber wurde 1918 „für die Synthese von Ammoniak aus dessen Elementen“ mit dem Nobelpreis ausgezeichnet.
Für ein Verfahren zur Herstellung von Kohlenwasserstoffen durch Hydrierung von Kohlenmonoxid an kobalt- oder eisenhaltigen Katalysatoroberflächen meldeten die deutschen Chemiker Franz Fischer (1877 – 1947) und Hans Tropsch (1889 – 1935) im Jahr 1925 ein Patent an. Während des Zweiten Weltkriegs war das nach ihnen benannte Fischer-Tropsch-Verfahren von großer wirtschaftlicher Bedeutung, da damit ein Teil der benötigten Kraftstoffe hergestellt werden konnte.
Wirkungsweise eines Katalysators
Die Funktion eines Katalysators beruht darauf, dass er einen neuen Reaktionsmechanismus ermöglicht. Er bildet mit einem Ausgangsstoff eine Zwischenverbindung, wodurch die Reaktionskinetik und die Aktivierungsenergie verändert werden. In Folgereaktionen bildet sich das Endprodukt, und der Katalysator wird freigesetzt. Die Funktionsweise der Katalyse kann durch folgende Reaktionsgleichungen beschrieben werden:
A + K → AK
AK + B → AB + K
Mit K als Katalysator, A und B als Edukte und AB als Produkt der Reaktion. Im Vergleich dazu steht die nicht-katalysierte Reaktion:
A + B → AB
Die Aktivierungsenergie der nicht-katalysierten Reaktion wird mit EU bezeichnet. Das folgende Schaubild zeigt den Vergleich einer katalysierten Reaktion (rot) und einer nicht-katalysierten Reaktion (schwarz). Die als EK bezeichnete Aktivierungsenergie der katalysierten Reaktion ist geringer.
Ziegler-Natta-Katalysatoren
In der Nachkriegszeit legten die Untersuchungen von katalytischen Prozessen den Grundstein für die petrochemische Kunststoffproduktion. Polyethylen wurde bereits 1939 industriell produziert, jedoch bei extrem hohen Drücken. Erst die Entwicklung der Ziegler-Natta-Katalysatoren auf der Basis von Titanhalogeniden und aluminiumorganischen Verbindungen und benannt nach ihren Entdeckern Karl Ziegler (1898 – 1973) und Giulio Natta (1903 – 1979) erlaubte die Herstellung von Polymeren unter milderen Bedingungen. Die beiden Chemiker erhielten 1963 „für ihre Entdeckungen auf dem Gebiet der Chemie und der Technologie der Hochpolymeren“ den Nobelpreis. Polyethylen ist heute ein Massenkunststoff und wird unter anderem zu Kunststoffschläuchen, Folien, Verpackungen oder Formteilen verarbeitet.
Zu Beginn verblieb aufgrund der geringen Katalysatoraktivität eine relativ große Katalysatormenge im Produkt, das deshalb aufbereitet werden musste. Durch ständige Weiterentwicklung der Katalysatoraktivität genügen heute 1 Gramm Titan in der Katalysatorzusammensetzung zur Herstellung von mehr als 1 Tonne Polymer.
Die nach ihnen benannte Ziegler-Natta-Polymerisation wird auch heute noch zur Herstellung von Polyolefinen und Ethylen-Propylen-Dien-Kautschuk (EPDM) eingesetzt. Zu den Polyolefinen zählen Polyethylen hoher und niedriger Dichte (HD-PE und LD-PE), Polypropylen (PP), Polybutylen (PB), Polyisobutylen (PIB) und Polymethylpenten (PMP). Sie haben den größten Anteil an der gesamten Kunststoffproduktion und werden auch als Standard- oder Massenkunststoffe bezeichnet. Diese Polymere dienen zur Herstellung von Folien, Verpackungen, Kunststoffbehälter, Haushaltswaren, Rohre sowie Boden- und Wandbeläge.
EPDM ist ein gummiartiger, weicher Synthesekautschuk und wichtiges Ausgangsmaterial für die Produktion von Dichtungen, Kühlschläuchen und anderen Gummischläuchen, Teichfolien und Abdichtungsbahnen.
Metallocen-Katalysatoren
Neben Ziegler-Natta-Katalysatoren haben sogenannte Metallocen-Katalysatoren an Bedeutung gewonnen. Metallocene sind Moleküle, die aus zwei flachen Ringen aus Kohlenstoffatomen und einem dazwischen liegenden Metallatom bestehen. Aufgrund ihrer Struktur werden sie auch als Sandwich-Komplexe oder Sandwich-Moleküle bezeichnet.
Metallocen-Katalysatoren erlauben ebenso wie Ziegler-Natta-Katalysatoren die Niederdruckpolymerisation von Ethylen und Propylen, zeichnen sich jedoch durch eine höhere Produktivität und Selektivität aus. Bei der Herstellung von Polypropylen lässt sich zusätzlich die Taktizität, die relative Lage der Methylgruppen, gezielt einstellen.
Andere Katalysatortypen
Auch bei der Herstellung von Phenoplasten, duroplastischen Kunststoffen, werden Katalysatoren verwendet. So werden zur Bildung von Phenolharzen aus Phenolen und Aldehyden Säurekatalysatoren wie Salzsäure, Oxalsäure oder Schwefelsäure eingesetzt. Die Phenolharze werden anschließend mit Härter und Zusatzstoffen wie Farb-, Füll- oder Verstärkungsstoffe gemischt, in eine Form gebracht und ausgehärtet.
Der bekannteste Vertreter dieses Kunststoffs ist Bakelit, das bereits 1905 von dem belgischen Chemiker Leo Hendrik Baekeland (1863 – 1944) erfunden wurde. Aus diesem Polymer wurden Haushalts- und Küchengegenstände, Gehäuse für Lichtschalter, Stecker, Steckdosen, Radios, Telefone, Isolatoren und Karosserieteile des Trabants produziert. Heute werden aus Phenol-Formaldehydharz Leiterplatten, Schleifscheiben, Isolationsmaterialien, Hitzeschilder und Reibbeläge gefertigt.
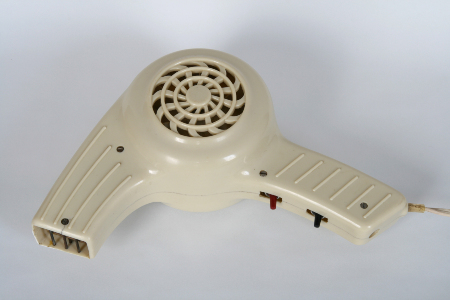
Aktuelle Entwicklungen und Ausblick: Bedeutung moderner Katalysatoren
Die Bedeutung der Katalyse lässt sich an der Anzahl der Nobelpreisträger, die sich mit diesem Thema beschäftigt haben und hier nicht vollständig aufgelistet sind, erahnen.
Die asymmetrische Organokatalyse verwendet organische Moleküle anstelle von Metallkatalysatoren und zeichnet sich durch eine hohe Sensitivität für die Chiralität, eine bestimmte Anordnung von Atomen in einem Molekül, aus. Die Chiralität ist besonders bei bioaktiven Substanzen wie Medikamenten von großer Bedeutung, bei denen of nur eine chirale Variante wirksam ist.
Katalysatoren bei der Kunststoffherstellung bieten mehrere Vorteile. Sie ermöglichen einen reduzierten Energiebedarf, der niedrigere Produktionskosten und einen geringeren CO2-Ausstoß zur Folge hat. So kann die Effizienz des Produktionsprozesses durch höhere Ausbeuten und Selektivität bei gleichzeitig reduziertem Abfall gesteigert werden. Mit ihrer Hilfe können Polymere mit spezifischen Eigenschaften wie hoher Festigkeit, Transparenz und Flexibilität hergestellt werden.
In der Vergangenheit wurden katalytische Prozesse hauptsächlich für die Kunststoffherstellung und die Abgasreinigung von Automobilen und Emissionen in der chemischen Industrie entwickelt. Als interdisziplinäre Technologie gewinnt die Katalyse auch zunehmend an Bedeutung beim Recycling von Kunststoffen, der nachhaltigen Synthese von Kraftstoffen aus Kohlendioxid oder von Funktionschemikalien aus nachwachsenden Rohstoffen sowie bei der katalytischen Wasserspaltung zur Herstellung von Wasserstoff aus erneuerbaren Energien.
Quellen: [1]: W. Ostwald: Referat zur Arbeit F. Strohmann: Über den Wärmegehalt der Bestandteile der Nahrungsmittel, Zeitschrift f. physik. Chemie (15), 1894, S. 705 f.
Bildquellen: Beitragsbild | © Sergey – stock.adobe.com Fotografie von Friedrich Wilhelm Ostwald | gemeinfreies Werk Schaubild: Vergleich einer katalysierten Reaktion und einer nicht-katalysierten Reaktion | © Sponk, Public domain, via Wikimedia Commons Bakelit-Haartrockner | © Till Niermann, CC BY-SA 3.0 <https://creativecommons.org/licenses/by-sa/3.0>, via Wikimedia Commons