Pneumatik in der Steuerungs- und Antriebstechnik
Die Pneumatik nutzt Druckluft als Medium, um mechanische Arbeit zu verrichten. Die Grundlagen dafür waren schon in der Antike bekannt. Bereits im 3. Jahrhundert vor Christus konstruierte der griechische Mathematiker und Erfinder Ktesibios (285 – 222 v. Chr.) eine Pumpe, die mithilfe von Druckluft Wasser aus der Tiefe heben konnte, um Brunnen und Badebecken damit zu speisen. Seine Erfindung ging als „Ktesibische Pumpe“ in die Industriegeschichte ein. Die vermeintlich alte Technik ist noch immer aktuell: Ihr Prinzip findet sich in vielen Typen heutiger Wasserpumpen wieder.
Der Begriff „Pneumatik“ leitet sich von dem altgriechischen Wort „pneuma“ (πνεῦμα) ab, das am treffendsten mit dem deutschen Wort „Wind“ zu übersetzen und in dem Zusammenhang mit den heute technisch geläufigen Begriffen „Druckluft“ oder „Pressluft“ gleichzusetzen ist.
Druckluft ist die Voraussetzung für die pneumatische Steuerungs- und Antriebstechnik
Die pneumatische Steuerungs- und Antriebstechnik benötigt Druckluft als Steuermedium. Die Erzeugung der Druck- oder Pressluft erfolgt in Druckluftanlagen mit Kompressoren. Im technischen Sprachgebrauch werden sie auch Verdichter genannt.
Die verdichtete und gereinigte Luft wird in einem nachgeschalteten Reservoir, dem sogenannten Windkessel, gespeichert. Je nach Größe des Verdichters und der zu steuernden Anlagen reicht sein Volumen von wenigen Litern bis zu mehreren hundert Litern.
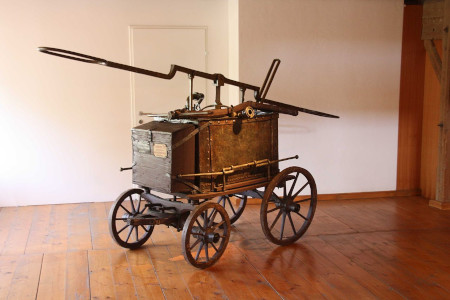
Dem Windkessel kommt insbesondere die Aufgabe zu, einen gleichmäßigen Arbeitsdruck zu gewährleisten und Druckspitzen zu glätten. Er ist grundsätzlich mit einem Regelventil ausgerüstet, das bei Erreichen des zulässigen Höchstdrucks den Kompressor abschaltet. Der maximale Druck für den Betrieb pneumatisch gesteuerter Anlagen beträgt üblicherweise 6 bar, für hochruckgesteuerte Systeme sind je nach Auslegung Drucke von 16 bar oder auch 40 bar erforderlich.
Die anschließende Verteilung der komprimierten Luft zu den jeweiligen Abnehmern erfolgt über Pneumatikrohre und Pneumatikschläuche. Das sind flexible Druckluftschläuche aus Polyvinylchlorid (PVC), Polyethylen (PE), Polyurethan (PUR), Polyamid (PA) oder Doppelmantel-Druckschläuche, wie EPDM-Doppelmantelschläuche.
Auch harte Kunststoffschläuche sowie PVC-U-Druckrohre und PP-Druckrohre kommen als feste Rohrleitungen in der Pneumatik zum Einsatz, ebenso wie Rohre aus Messing, Kupfer und Edelstahl.
Viele technische Prozesse und Verfahren benötigen komprimierte Luft
Die beiden wichtigen Anwendungsgebiete der Pneumatik sind die Steuerungstechnik und die pneumatische Antriebstechnik. Beide nutzen die beim Entspannen von Druckluft in Druckluftzylindern freigesetzte kinetische Energie, um mechanische Bewegungsvorgänge zu initiieren.
Pneumatische Steuerungstechnik
Im Bereich der Steuerungstechnik werden mittels Druckluftzylindern Ventile, meist Membranventile, geöffnet oder geschlossen oder Mehrweghähne, meist pneumatische Kugelhähne, geschaltet, um Flüssigkeits- oder Gasströme abzusperren oder zu leiten.
Davon abgewandelte Systeme dienen zum Einspannen, Auswerfen oder Zuführen von Teilen in automatischen Produktionsanlagen, die in der Automobilindustrie längst zum Standard gehören. Schließlich ist die Rohrpost eines der älteren Beispiele für die Nutzung von komprimierter Luft für lineare Bewegungsvorgänge, die für die Automatisierungstechnik zunehmend wieder in das Blickfeld der Entwickler fällt.
Pneumatische Antriebstechnik
Die pneumatische Antriebstechnik bietet für die Praxis zwei technische Möglichkeiten: den Lamellen-Motor und den Pressluft-Motor. Beide sind Gasexpansionsmotoren.
Der Aufbau von Lamellenmotoren ähnelt dem von Drehschieber-Pumpen. Im Gegensatz zur Drehschieberpumpe wird der mit beweglichen Lamellen ausgestatte Rotor jedoch durch die in den Stator einströmende und darin expandierende Druckluft unmittelbar in Rotation versetzt.
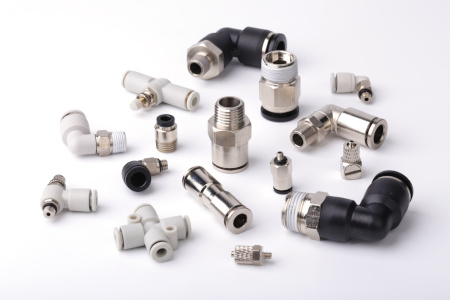
Der Pressluft-Motor ist hingegen eine Kolbenmaschine, bei der die komprimierte Luft in einem Druckzylinder expandiert. Die dabei durch den Kolben primär erzeugte Längsbewegung muss mechanisch in eine Drehbewegung umgewandelt werden, beispielsweise über einen Exzenter.
Gasexpansionsmotoren sind explosionssicher, da die bei Elektromotoren unvermeidbare Funkenbildung hier ausgeschlossen ist. Sie können deshalb auch in explosionsgefährdeten Bereichen eingesetzt werden. Gasexpansionsmotoren werden in Drucklufthämmern, Bohrmaschinen und pneumatischen Drehmoment-Schraubern erfolgreich verbaut.
Davon übrig geblieben sind einige wenige Nischenentwicklungen, etwa die von Grubenloks und von Zugmaschinen für Werksverkehre der Chemieindustrie. Sie werden von mitgeführter Druckluft angetrieben und haben demzufolge auch nur geringe Aktionsradien.
Druckluft ist jedoch bei zahlreichen Produktions- und Arbeitsabläufen unverzichtbar geworden, wenngleich ihr Einsatz mit Pneumatik im eigentlichen Sinn nur noch wenig zu tun hat. Dazu zählen das Blasformen von Kunststoffen, das Spritzlackieren in der Automobilindustrie und im Maschinenbau, das Reinigen von Gussformen durch Ausblasen und das Sauberblasen von Formteilen vor ihrer Weiterverarbeitung sowie Schnell-Trocknungsprozesse.
Wie funktioniert die pneumatische Steuerung?
Eine pneumatische Steuerung ist immer aus zwei Einheiten aufgebaut: einem Steuersystem sowie einem oder mehreren Antriebssystemen. Hierbei kann es sich um einen der bereits erwähnten Gasexpansionsmotoren handeln. Um diese anzusteuern, wird ein Steuerelement vorgeschaltet. Dabei handelt es sich meistens um Ventile, die die Luft in vorgegebener Weise durch Mehrwegeventile, Sperrventile oder Druckventile weiterleiten. Diese Steuerelemente können wiederum pneumatische, elektrische und mechanische Signale registrieren, weiterverarbeiten und damit das Antriebselement steuern. Dementsprechend unterscheidet man zwischen der vollpneumatischen Steuerung, der elektropneumatischen, der hydraulisch-pneumatischen und der mechanisch-pneumatischen Steuerung.
Bei der vollpneumatischen Steuerung werden Pneumatikventile als Steuerelement eingesetzt, die selber über Druckluft betätigt werden. Dieses Signal geben sie dann an das Antriebselement weiter. Je nach Konstruktion können pneumatische Ventile mit 2-Wegehahn oder Mehrwegehahn für die pneumatische Steuerung eingesetzt werden. Am häufigsten werden elektropneumatische Steuerungen eingesetzt, bei denen die Ventile elektrisch angesteuert werden. Mechanische Steuerelemente sind zum Beispiel Federn, die sich selbst im Antriebselement befinden. Sie sorgen dann beispielsweise dafür, dass das System nach der pneumatischen Ansteuerung wieder in seine Ausgangslage zurückfährt.
Welche Vorteile hat die pneumatische Steuerungstechnik
Pneumatische Systeme sind robust und vor allem gegenüber Umwelteinflüssen, Schmutz, Schwingungen und Stöße oder auch Temperaturschwankungen weitgehend unempfindlich. Pneumatische Steuerungen sind auch in explosionsgefährdeten Bereichen einsetzbar.
Eine pneumatische Steuerung ist zudem wartungsarm, sowie kostengünstig und technisch einfach zu realisieren. Sie erlauben hohe Arbeitsgeschwindigkeiten. Vor allem aber sind auf geringem Raum hohe Kräfte damit realisierbar und stufenlos einstellbar.
Nachteile der pneumatischen Steuerungstechnik
Der Einsatz anderer Steuerungstechniken, wie der elektrischen, wird vor allem mit dem hohen Energieverbrauch der pneumatischen Technik begründet, denn in den Druckluftanlagen arbeiten energieintensive Kompressoren.
Ein weiterer Nachteil ist das schwere Auffinden von Leckagen in Druckluftanlagen, was einerseits die technische Sicherheit mindert und andererseits Einfluss auf den Energieverbrauch hat und diesen gegebenenfalls weiter erhöht, wenn die Druckluftanlage den Druckschwund durch die unerkannte Undichtigkeiten auszugleichen sucht. Zudem sind diese Anlagen sehr laut.
Vergleicht man pneumatische mit hydraulischen Systemen, so sind die Kräfte, die mit hydraulischen Systemen erzeugt werden können, um einiges höher, da Flüssigkeiten praktisch inkompressibel sind. Schließlich kühlt ausströmende Luft bei schneller Expansion stark ab. In einigen Anwendungen ist dies erwünscht, bei Druckluftmotoren kann dies aber zu Problemen, wie der Vereisung der Motoren, führen.
Verbesserung der Energieeffizienz in Druckluftanlagen
Der hohe Energieverbrauch bei der Drucklufterzeugung ist einer der größten Nachteile der Pneumatik. In den letzten Jahren konnte durch Wärmerückgewinnung der arbeitenden Kompressoren deren Energieeffizienz aber erhöht werden. Besonderes Augenmerk muss auf die Wartung des Verteilungsnetz gelegt werden sowie deren sachgerechte Dimensionierung. Durch die richtige Auslegung einer pneumatischen Anlage können Energieeinsparpotentiale realisiert und die Anlage effizient genutzt werden.
Die Pneumatik bleibt eine moderne Technik
Industriebereiche, wie Maschinenbau, Verfahrenstechnik, chemische Industrie oder Wasserversorgung, nutzen die Steuerungstechnik der Pneumatik, um Prozesse zu steuern. Dabei gilt die pneumatische Steuerungstechnik als kostengünstig und einfach in der Bedienung. Vor allem zeichnet sie sich durch ihre Robustheit aus.
Zwar werden immer mehr elektrische Antriebe eingesetzt, aber auch eine pneumatische Lösung oder die Kombination von beiden kann in vielen Fällen sinnvoll sein. Die Grundlagen der Pneumatik zu kennen und sie zweckvoll anzuwenden ist damit auch mehr als zweitausend Jahre nach ihrer Entdeckung in vielen Bereichen von Bedeutung.
Bild-Quellen: Beitragsbild | © Temir – stock.adobe.com Alte Feuerspritze zur Brandbekämpfung | @ papa1234 - Eigenes Werk, CC BY 3.0, https://commons.wikimedia.org/w/index.php?curid=11301549 Steckverbinder für Anschluss von Pneumatikschläuchen | @ christianchan - stock.adobe.com