Stahl ist allgegenwärtig im Alltag: in Form von Schmuck oder Kochtöpfen, Werkzeugen oder Autofelgen, in Industrie und Gewerbe als Stahlbeton, Schiffsrumpf oder Autokarosserie und in der Entsorgung als wertvolles Gut zum Wiederverwenden. Die Stahlindustrie gilt als das Rückgrat der deutschen Wirtschaft. Doch was steckt hinter diesem Werkstoff und was macht ihn so besonders? Und was wird in Zeiten der Energiewende getan, um Stahl emissionsarm erzeugen zu können?
Ein Werkstoff mit maßgeschneiderten Eigenschaften und Anwendungen
Ohne Eisen kein Stahl, denn die begehrte Legierung besteht hauptsächlich aus dem Element Eisen. Der Unterschied, der Eisen zu Stahl macht, ist winzig, doch entscheidend.
Der Kohlenstoff sorgt dafür, dass die Legierung im Vergleich zu reinem Eisen veränderte Eigenschaften aufweist. Das Metall wird fester und härter, bleibt jedoch gleichzeitig zäh, wodurch sich der Werkstoff formen lässt. Er lässt sich schmieden, walzen, biegen und ziehen.
Außerdem korrodiert der Kohlenstoffstahl nicht mehr so schnell wie reines Eisen. Ausgehend von dieser Grundsubstanz lassen sich die Eigenschaften von Stahl weiter maßschneidern, was ihn zum vielseitigen Konstruktionswerkstoff in fast allen Bereichen der Technik macht. Dies geschieht durch Beimischen weiterer Metalle. Je nach gewünschter Stahlqualität und Einsatzzweck greifen die Hersteller zu verschiedenen Elementen. Legierter Stahl ist eine Wissenschaft für sich.
Stahl und seine unterschiedlichen Eigenschaften
Legierungsbestandteile Chrom und Nickel
Chrom ist das Element, das Stahl zu beinahe unverwüstlichem Edelstahl macht. Die Produkte mit der eisgrauen und rostfreien Oberfläche wie Schmuck, Töpfe, medizinische Geräte, ganze Produktionsanlagen in der Lebensmittelindustrie oder pharmazeutischen Produktion sowie vieler weiterer Spezialanwendungen enthalten mindestens 10,5 % Chrom. Der Anteil kann in manchen Fällen bis zu 18 % betragen.
In jedem Fall sorgt der Chromanteil dafür, dass der Stahl besonders korrosionsbeständig ist. Verantwortlich dafür ist eine dünne Oxidschicht, die das Chrom an der Oberfläche bildet und damit das Werkstück schützt. Ein Nickelanteil steigert ebenfalls die Korrosionsbeständigkeit, verändert jedoch auch die Konsistenz. Der Stahl wird zäher und formbarer.
Legierungsbestandteile Molybdän und Titan
Besonders hitzebeständige Stähle, wie sie etwa in Kraftwerken eingesetzt werden, enthalten Molybdän und teils Titan. Hitzebeständige Stähle werden beispielsweise zu Schlauchverbindern (Klemmringverschraubungen und Schneidringverschraubungen), Edelstahl-Schläuchen und Edelstahl-Kapillaren verarbeitet.
Werkzeugstähle und andere Ausführungen
Ausgesprochen vielfältig ist das Angebot an Werkzeugstählen.
Sollen die Werkzeuge besonders hart und haltbar sein und etwa auch bei höheren Temperaturen über +200 °C eingesetzt werden, kommen Vanadium, Wolfram, Mangan und Cobalt zum Einsatz.
Im Gegensatz zum Kohlenstoffstahl lässt sich der korrosions- sowie temperaturbeständige und zudem hygienische Edelstahl praktisch überall im produzierenden und technischen Umfeld verwenden: in Großküchen ebenso wie in Fertigungsstätten der Chemie- und Prozessindustrie, aber auch in Laboren. Um die Aufgaben in diesen Bereichen zu lösen, reicht die enorme Bandbreite der in Systemen und Subsystemen eingesetzten Komponenten von Hähnen und Ventilen über Antriebselemente, wie etwa Zahnräder oder Zahnstangen, und Verbinder bis hin zu Befestigungselementen, Schläuchen, Rohren und Kapillaren.
Wie werden die unterschiedlichen Stahl-Legierungen differenziert?
Um den Überblick über die Stahlqualitäten zu behalten, wie genau ein Stahl beschaffen ist, welche Eigenschaften er exakt hat und welche Legierung verwendet wird, erhält jeder Stahl eine sogenannte Werkstoffnummer.
Vergeben wird sie vom Stahlinstitut VDEh, der technisch-wissenschaftlichen Gemeinschaftsorganisation der deutschen Stahlindustrie. Die Abkürzung VDEh entstammt der Historie und steht für Verein Deutscher Eisenhüttenleute. Das Bundesministerium für Wirtschaft und Klimaschutz (BMWK) geht in einer Publikation von derzeit rund 2400 Stahlsorten aus, die in Deutschland produziert werden und unter einer jeweiligen Werkstoffnummer auffindbar sind.
Wie wird Stahl hergestellt?
Es gibt zwei Hauptverfahren, mit denen Stahl gewonnen wird. Die herkömmliche Methode nutzt Eisenerz, das mittlerweile in Deutschland vollständig importiert werden muss. Da Stahl jedoch zu 100 % und laut der Wirtschaftsvereinigung Stahl (WV Stahl) ohne jeden Qualitätsverlust recycelt werden kann, wird das Recycling von Stahl über einen Elektroofen industriell immer wertvoller. Das liegt auch daran, dass 1 t Stahl, die über die Hochofenroute gewonnen wird, ebenso für die Produktion von 1,7 t Kohlenstoffdioxid (CO2) sorgt. Im Stahlrecycling über den Elektroofen fällt nur ein Bruchteil davon an.
Die Hochofenroute für die Stahlerzeugung
Die Verhüttung von Eisenerzen im Hochofen ist ein Jonglieren mit Superlativen. Ein großer Hochofen misst im Durchmesser bis zu 15 m bei einer Höhe von bis zu 100 m. Bei diesen Abmessungen hat er ein Volumen von rund 6000 m³ und es entstehen Temperaturen von bis zu +2200 °C. Ein so dimensionierter Hochofen produziert laut WV Stahl rund 13.000 t Roheisen pro Tag oder mehr als 4 Mio. t pro Jahr.
Steinkohle fungiert zugleich als Brennstoff und als Reduktionsmittel, was bedeutet, dass der Sauerstoff aus der Bindung zum Eisen entweicht und an den Kohlenstoff gebunden über die Zwischenstufe Kohlenmonoxid (CO) als Kohlendioxid (CO2) den Prozess verlässt. Das Eisen sammelt sich als flüssiges Metall im unteren Bereich des Hochofens und fließt als Roheisen mit einer Temperatur von rund +1500 °C ab.
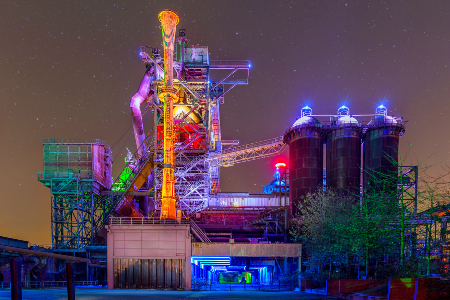
Damit der Prozess so stattfinden kann, sind zahlreiche Vorarbeiten notwendig. Das Erz wird zerkleinert oder in Pellets überführt. Zuschlagstoffe, die Verunreinigungen binden sollen, und weitere Hilfsstoffe werden zunächst gesintert und so von oben zusammen mit dem vorbereiteten Eisenerz in den Hochofen verfrachtet. Es ist typisch für die Funktionsweise eines Hochofens, dass der Temperaturgradient von oben nach unten zunimmt, also von oben nach unten immer heißer wird.
Stahlherstellung mit Wasserstoff
Weil die klassische Produktion von Stahl im Hochofen sehr viel Energie verbraucht und gleichzeitig sehr viel CO2 ausstößt, forscht die Industrie nach klimafreundlicheren Methoden. Die CO2-Produktion unter den Wert von 1,7 t Kohlendioxid pro Tonne Roheisen zu drücken, ist laut WV Stahl nur mit einem anderen Reduktionsmittel möglich.
Attraktiv ist der Einsatz von Wasserstoff. Dann entsteht Wasserdampf anstelle von Kohlendioxid. Für die CO2-Bilanz des Verfahrens ist in diesem Fall allerdings auch wichtig, dass der Wasserstoff zuvor klimaneutral gewonnen wurde.
Die Reduktion Eisenerz mit Wasserstoff statt mit Koks führt zu einem etwas anderen Produkt. Der Wasserstoff wird als Gas eingesetzt und der Reduktionsprozess bei vergleichsweise niedrigen Temperaturen geführt. Das Verfahren nennt sich wasserstoffbasierte Direktreduktion (engl. Direct Reduced Iron, DRI). Wegen der niedrigen Temperaturen entsteht kein flüssiges Roheisen, sondern ein festes Eisenprodukt: ein Roheisenschwamm. Der Eisenschwamm wird anschließend in einem Elektrolichtbogen- oder Schmelzofen zu Stahl weiterverarbeitet.
Stahlrecycling als Beispiel für gelungene Kreislaufwirtschaft
Laut WV Stahl werden derzeit 70 % des Stahls in integrierten Hüttenwerken (Hochofen, Stahl- und Walzwerke) gewonnen und 30 % über die sogenannte Sekundärroute. Letztere bedeutet, dass nicht Hochöfen, sondern Elektroöfen verwendet werden. Unter Elektroöfen verstehen die Stahlkocher sogenannte Lichtbogenöfen. Solche Öfen sind keine neuen Erfindungen, kommen aber aktuell besonders für das Stahlrecycling im Großmaßstab zum Einsatz.
Stahlherstellung im Lichtbogenofen ist eine beeindruckende Szenerie. Durch hohe Spannungen zwischen zwei Elektroden wird das Medium zwischen den Elektroden ionisiert. Es bildet sich ein Plasma, das durch den Stromfluss zum sichtbaren und sehr energiereichen Lichtbogen wird und es entstehen Temperaturen von rund +3500 °C. Typisch für Lichtbogenöfen ist allerdings auch ein immenser Lärm. Im Fall des Stahlrecyclings entstehen die Lichtbögen zwischen Graphitelektroden und dem zu schmelzenden Stahlgut oder Stahlschrott.
Stahl aus dem Lichtbogenofen
Die Hitze des Lichtbogens lässt den Stahlschrott schmelzen. Zudem laufen im Lichtbogenofen zwei weitere Prozesse ab: das Frischen und das Legieren. Beim Frischen wird dem Prozess Sauerstoff zugeführt, mit dem unerwünschte Stoffe Oxide bilden, die dann als Schlacke von der Schmelze abgezogen werden können.
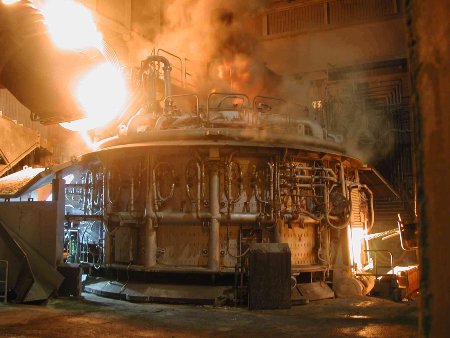
Beim Legieren werden dem flüssigen Stahl die gewünschten Elemente, etwa Chrom, Mangan oder Nickel, zugefügt, je nach Eigenschaft, die der Stahlkocher erhalten möchte. Der fertige Stahl wird meist zu sogenannten Brammen gegossen. Diese quaderförmigen Blöcke bilden als Halbzeug oft das Vormaterial für Platten, Bänder, Stangen, Schmiedeteile oder Drähte.
Da beim Elektroofenverfahren kein Koks eingesetzt wird, entsteht nur wenig Kohlendioxid. Allerdings frisst der Vorgang große Strommengen. Die Stahlindustrie setzt deswegen auf erneuerbare Energien und strebt so eine CO2-reduzierte Stahlproduktion an.
Die Recyclingquoten für Stahl sind weltweit sehr hoch, durchschnittlich liegen sie bei etwa 80 %. In Deutschland liegt die Quote sogar darüber. Von 100 t Stahl, die in Deutschland produziert werden, werden 93 t zurückgeführt ins Stahlrecycling. Insgesamt liegt die Jahresproduktion von Stahl bei 40 Mio. t Rohstahl.
Deutschland ist damit der größte Stahlproduzent in Europa und der achtgrößte weltweit. Die Baubranche, die Automobilindustrie, der Maschinenbau und die Energieerzeugung sind Hauptabnehmer. Stahl ist der am häufigsten verwendete und recycelte industrielle Werkstoff. Selbst private Haushalte haben einen gut bezifferten Stahlverbrauch. Laut dem Branchenverband WV Stahl werden jährlich in Deutschlands Haushalten 180 kg Stahl pro Kopf benötigt, um den privaten Konsum zu decken. Dazu gehören zum Beispiel 8 kg Stahl für die Produktion von Nahrungsmitteln oder knapp 2 kg allein rund um das Thema Körperpflege.
Ein Blick in die Geschichte
Die Verwendung von Eisen durch den Menschen war lange dadurch eingeschränkt, dass es keine Techniken gab, für die Verhüttung von Eisen ausreichend hohe Temperaturen erzeugen zu können. Das Eisen ließ sich nicht aus dem Erz gewinnen. Für erste Anwendungen wie beispielsweise Speerspitzen haben die Menschen auf gediegen aufgefundenes Eisen zurückgegriffen. Es stammte von Meteoriten. Diese Anwendungen werden von Wissenschaftlern auf etwa 4000 v. Chr. datiert.
Bis in Europa Gusseisen hergestellt und verwendet werden konnte, dauerte es noch bis ins 15. Jahrhundert. Dann aber verbreitete sich die Technik schnell mit der damaligen Kriegsindustrie, insbesondere um Geschützrohre und Kugeln gießen zu können. Diesen folgten Friedenswaren, etwa in Form von Kirchenglocken.
Eisen ist das zehnthäufigste Element im Universum und mit 4,7 % eines der häufigsten Elemente in der Erdkruste. Doch auch im Inneren ist Eisen ein wichtiges Element. Wissenschaftler halten es für den Hauptbestandteil des Erdkerns und gehen davon aus, dass flüssiges Eisen im Erdkern für das Magnetfeld des Planeten verantwortlich ist.
Bildquellen: Beitragsbild | © DedMityay – stock.adobe.com Hochofenanlage 2 im Landschaftspark Duisburg-Nord | © tobibambola – stock.adobe.com Lichtbogenofen der Georgsmarienhütte GmbH im Jahr 2005 | © GMH official, CC BY-SA 3.0 <https://creativecommons.org/licenses/by-sa/3.0>, via Wikimedia Commons