Obgleich Glasmatrix-Verbundwerkstoffe seit mehr als 30 Jahren bekannt und erforscht sind, führen sie in der Praxis immer noch ein Nischendasein für Spezialanwendungen. Dies liegt nicht zuletzt am relativ geringen Bekanntheitsgrad. Grund genug, diese Werkstoffe ins Bewusstsein der Anwender zu rücken. Dieser Artikel spannt den Bogen von den faserverstärkten Werkstoffen allgemein bis zum faserverstärkten Glas mit herausragenden Eigenschaften etwa für verschleißfeste Bauteile.
Was sind faserverstärkte Verbundwerkstoffe?
Dabei unterscheiden sich die Materialeigenschaften der Komponenten von denen des Verbundes. Wie der Name schon sagt, sollen die eingelagerten Fasern den Werkstoff verstärken, also ihm mehr Festigkeit verleihen.
Im Belastungsfall erfolgt ein Lasttransfer von der Matrix auf die eingelagerten Fasern, die eine höhere Festigkeit als die Matrix aufweisen. Bekommt die Matrix gar Risse, so werden diese an den Fasern gestoppt oder umgeleitet und die Wahrscheinlichkeit für einen plötzlichen Bruch des Materials verringert.
Welche Fasern kommen zum Einsatz? Wie werden Fasern in die Matrix eingebunden?
Die Fasern werden als Endlosfasern auf Spulen angeboten. Sie liegen in Form von Fasersträngen von mehreren Tausend Einzelfasern vor, wobei der Durchmesser einer Einzelfaser circa 10 µm beträgt. Einzelfasern nennt man auch Filamente, gebündelt Roving. Die Anzahl der Filamente im Roving wird je 1000 Stück mit 1K bezeichnet. Ein 6K Roving enthält demnach 6000 Einzelfilamente. Die Faserstränge müssen vor dem Einbringen in die Matrix vereinzelt werden. Dabei können die Fasern kurz geschnitten und ungeordnet im Werkstoff verteilt sein. Der daraus resultierende Verbund zeigt demnach in alle Raumrichtungen annähernd gleiche Eigenschaften, die auch als isotrop bezeichnet werden.
Zeigen die Langfasern alle in eine Richtung, spricht man von unidirektionaler Faserorientierung. Die Verbunde können aber auch schichtweise aufgebaut sein, wobei sich die Orientierung der Fasern in den Schichten abwechselnd unterscheidet. So gibt es etwa Verbunde mit 0°/90°-Orientierung, in denen die Schichten abwechselnd rechtwinklig zueinander liegen. Bekannt sind auch 0°/45°/90°-Verbunde. Beispiele für Verbundwerkstoffe mit Faserausrichtung sind Profile, Stäbe und Rohre aus Glasfaserverstärkten Kunststoffen.
Die Relevanz der Faserausrichtung
Die Ausrichtung der Fasern im Verbund wird durch den späteren Einsatzzweck bestimmt. Wird das Bauteil später ausschließlich rechtwinklig zur Faserrichtung belastet, bieten unidirektionale Gelege die optimale Verstärkung. Dadurch können die Bauteile im Vergleich zum unverstärkten Material dünner und leichter ausgelegt werden. Die Masseersparnis bei gleicher Festigkeit führt zu kostengünstiger und umweltschonender Technologie.
Die Fasern lassen sich auch zu textilen Geweben verarbeiten, welche mit Matrixmaterial infiltriert und geschichtet zu Verbunden verarbeitet werden können. Die einzelnen Schichten werden Gelege genannt.
Die Herstellungstechnologie richtet sich nach den Eigenschaften des Matrixmaterials. Dieses muss in der Regel aufgeschmolzen werden, um die Verstärkungskomponenten gleichmäßig zu umhüllen. Im Bereich der Kunststoffe liegen Matrixmaterialien auch als Mono- oder Oligomere vor, die im Verlauf des Fügeprozesses polymerisieren und sich zu Duroplasten verfestigen.
Wo werden faserverstärkte Werkstoffe eingesetzt?
Bekannte Faserverbundwerkstoffe sind glasfaserverstärkte Kunststoffe (GFK), auch unter dem Namen „Fiberglas“ geläufig, kohlefaserverstärkte Kunststoffe (CFK) oder auch glasfaserverstärkter Beton (GFRC), in den statt Stahlarmierungen Glasfasermatten oder Kurzglasfasern eingearbeitet sind.
Die Anwendungen sind vielfältig und reichen von der Architektur über den Bootsbau, die Herstellung von Sportgeräten und den Fahrzeugbau bis hin zu Hochtechnologieanwendungen wie Windkraftanlagen und Flugzeugen. In Laboranwendungen finden sich glasfaserverstärkte Erzeugnisse als Befestigungselemente wie etwa Gewindestangen oder Bügelgriffe ebenso wie als Kunststoffrohre, Profile, Isolierstützer oder Rundfilter.
Können glasfaserverstärkte Kunststoffe recycelt werden?
So interessant und innovativ faserverstärkte Werkstoffe sind, so problematisch ist trotz jahrelanger Anwendung das Recycling.
Glas als Werkstoff: Alleinstellungsmerkmale und Einsatzgrenzen
Der Werkstoff Glas ist eng mit der Kulturgeschichte des Menschen verknüpft. Vom Luxusgegenstand der Antike in Form von Trinkgefäßen und Schmuck hat sich Glas Anwendungsfelder in der Architektur, dem Fahrzeugbau und der Hochtechnologie im Bereich der Optik und Mikrosystemtechnik erschlossen.
Neben einer hohen Festigkeit sowie guter thermischer und chemischer Beständigkeit ist das wohl bedeutendste Merkmal des Glases seine Durchsichtigkeit, das heißt die Transparenz für sichtbares Licht. Mit Blick darauf können Kunststoffe heute mit Gläsern konkurrieren, erreichen aber niemals deren Festigkeit und Dauerbeständigkeit.
Der limitierende Faktor beim Einsatz des Werkstoffs Glas ist jedoch unverändert sein sprödes und katastrophales Bruchverhalten. Der Ausdruck spröde bedeutet dabei unelastisches Verhalten und ist umgangssprachlich schon ein Synonym für Glas. Glas kann mechanischen Belastungen nur gering durch plastisches Verformen ausweichen und der Bruch erfolgt plötzlich, also katastrophal. Dies gilt im Prinzip auch für Keramiken, die sich vom Glas durch ihren atomaren Aufbau unterscheiden, aber ein ähnliches Bruchverhalten zeigen.
Während Glas, das durch einen Schmelzprozess aus dem Hauptbestandteil Siliziumdioxid mit unterschiedlichen Beimengungen gewonnen wird, den Charakter einer erstarrten Schmelze und eine nahezu regellose Struktur der atomaren Bausteine aufweist, sind gebrannte Keramiken durch einen regelmäßigen atomaren Aufbau gekennzeichnet. Glas ist ein amorpher (griechisch: a morphe = ohne Gestalt) und Keramik ein kristalliner Festkörper.
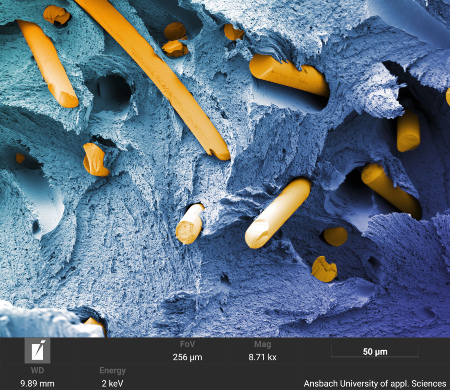
Somit wird das Einsatzspektrum sowohl von Gläsern als auch von Keramiken durch ihr sprödes Bruchverhalten entscheidend eingeschränkt. Gleichwohl sind Keramiken vielseitig einsetzbar. So lassen sich etwa mit Schrauben, Mutter und Unterlegscheiben aus Keramik technische Probleme lösen, bei denen aus anderen Werkstoffen gefertigte Verbindungs- und Befestigungselemente an ihre Grenzen kommen.
Das Konzept faserverstärkter, anorganischer „Sprödmatrix“-Verbunde: Gläser und Keramiken als Matrizes
Werkstoffwissenschaftler haben ausgehend von faserverstärkten Kunststoffen ein neues Konzept zur Faserverstärkung von spröden Werkstoffen entwickelt. Bei faserverstärkten Kunststoffen reagiert der Matrixwerkstoff elastisch respektive plastisch. Ein Lasttransfer von der mechanisch belasteten Matrix auf die Fasern setzt eine feste Haftung der Fasern in der Matrix voraus. Dazu müssen anorganische Glasfasern als Verstärkungskomponente häufig mit einem „Haftvermittler“ beschichtet werden, da sie die kohlenwasserstoffbasierte Kunststoffmatrix abstoßen, ähnlich wie Wasser ein Öl abstößt. Der „Mittler“ übernimmt praktisch die Rolle eines Spülmittels beim Abwaschen fettigen Geschirrs. Da die Kunststoffmatrix während der Verbundherstellung schrumpft, werden die Fasern praktisch in der Matrix eingeklemmt.
Ganz anders muss das Konzept für spröde brechende Matrizes aussehen. Das Fügen der Verbunde erfolgt bei relativ hoher Temperatur um +1000 °C oder höher durch Heißpressen. Dazu werden mit Matrixpulver infiltrierte Fasern oder Fasergelege in eine Form geschichtet und unter Druck erhitzt. Dementsprechend thermisch stabil müssen die verwendeten Verstärkungsfasern sein. Geeignete Fasern für Glasmatrixverbunde sind Keramik- oder Glasfasern.
Für Keramikmatrixverbunde eignen sich Keramikfasern. Bei diesen unterscheidet man oxidische und nichtoxidische Keramikfasern. Oxidische Fasern sind gegen Luftsauerstoff unempfindlich, während nichtoxidische gerade bei hohen Fügetemperaturen durch Luftsauerstoff oxidiert werden können. Lösen lässt sich das Problem, indem die Verbundherstellung im Vakuum oder unter Inertgasbedingungen, also in Edelgas- oder Stickstoffatmosphäre, erfolgt. Die Prozessführung im Vakuum bietet den Vorteil, dass Gaseinschlüsse im Verbund, welche die Verbundeigenschaften nachteilig beeinflussen, minimiert werden.
Die am Markt verfügbaren oxidischen Fasern basieren alle auf Aluminiumsilikat mit unterschiedlichen Beimengungen und sind polykristallin, bestehen also aus vielen kleinen Einzelkristallen, die durch Korngrenzen voneinander getrennt sind. Nichtoxidische Fasern sind zum Beispiel Kohlenstofffasern oder auch Siliciumcarbidfasern. Glasfasern, die nicht zu den keramischen Fasern zählen, werden aus einer Glasschmelze durch Düsen gezogen und sind amorph. Keramikfasern werden durch Pyrolyse von polymeren Vorstufen erzeugt und sind entweder amorph, wie Siliciumcarbid und Kohlefasern, oder polykristallin, wie Fasern auf Basis von Aluminiumsilikat.
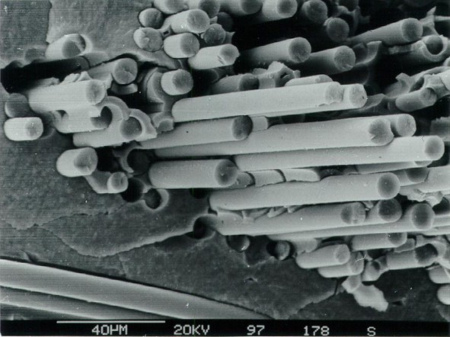
Die chemische Ähnlichkeit von Matrix und Verstärkungsfasern und die hohen Temperaturen führen dazu, dass Fasern und Matrix bei der Verbundherstellung miteinander verschmelzen. Dadurch würde zwar die Festigkeit des Verbundes im Vergleich zur Matrix erhöht, aber der Verbund weiterhin spröde brechen. Damit ein Riss im Matrixmaterial an der Matrix-Faser-Grenze gestoppt werden kann, darf keine stoffschlüssige Verbindung zwischen Faser und Matrix bestehen. Die Fasern müssen in der Matrix beweglich sein, aber trotzdem so festsitzen, dass bei mechanischer Belastung des Verbundes die Last von der Matrix auf die Faser übertragen werden kann. Man spricht von einer kraftschlüssigen Verbindung.
Dies wird erreicht, indem die Fasern mit einem thermisch stabilen Material beschichtet werden, das sich unter Fügebedingungen nicht mit der Matrix verbindet. Praktikable Lösungen dafür sind zum Beispiel Schichten aus hexagonalem Bornitrid oder Kohlenstoff mit einer Stärke von einigen Hundertstel Mikrometern. Wird die Last bis zum Bruch des Matrixmaterials erhöht, wandern die Risse in der Matrix bis zur nächsten Faser und anschließend an der Faser-Matrix-Grenze entlang, ohne die Faser zu zerstören. Beim weiteren Bruch der spröden Matrix werden die Fasern nach und nach aus der brechenden Matrix herausgezogen. Das Bauteil aus reiner spröder Matrix wäre in diesem Fall bereits zerstört, während die Fasern im Verbund, trotz brechender Matrix, den totalen Bauteilbruch durch ein „pseudoplastisches“ Verhalten verhindern.
Im Falle der Gläser stellt sich die Frage, ob durch hochschmelzende Glasfasern als Verstärkungskomponente für Matrixglas die Eigenschaft der Durchsichtigkeit auch für die Verbunde zumindest zum Teil erhalten werden kann. Neben der Abstimmung der optischen Eigenschaften von Glasfasern und Matrixglas aufeinander ist eine wesentliche Voraussetzung, dass Einschlüsse, wie Gasblasen und Verunreinigungen, während des Fügeprozesses minimiert werden. Zudem muss die Beschichtung der Verstärkungsglasfasern so gewählt werden, dass optische Störeffekte, wie Brechung und Reflexion, an den Grenzflächen möglichst minimiert werden. Werden diese Punkte beachtet, gelingt es, glasfaserverstärkte Glasmatrixverbunde herzustellen, die 30 bis 40 % des sichtbaren Lichtes im Vergleich zu reinem Glas passieren lassen und optisch durchscheinend sind.
Werkstoffprüfung, Charakterisierung und Anwendungsaspekte faserverstärkter Gläser
Um faserverstärkte Gläser zu charakterisieren, werden standardisierte materialwissenschaftliche Prüfverfahren eingesetzt. Dazu zählen quasistatische Biege-, Zug- und Scherversuche, die bei sehr kleinen Prüfgeschwindigkeiten durchgeführt werden.
Die Temperaturabhängigkeit der Materialeigenschaften spielt hinsichtlich der Anwendung eine wesentliche Rolle. Die Faser-Matrix-Grenzfläche wird durch die maximale Ablösekraft zum Herausziehen der Fasern aus der Matrix und die beim Gleiten der Fasern in der Matrix auftretende Grenzflächenreibspannung charakterisiert. Strukturelle Aspekte über den Aufbau werden durch Schallemissionsanalyse und Gefügeanalysen von polierten Schliffproben unter dem optischen Mikroskop untersucht. Dadurch erhält man Aussagen über das tatsächliche Mengenverhältnis von Matrix- zu Verstärkungskomponente, eventuelle Einschlüsse und den Kontakt zwischen Faser und Matrix, der die Qualität des Fügeprozesses widerspiegelt.
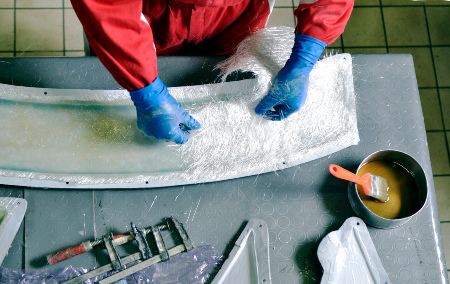
Die Bruchflächen geprüfter Probekörper werden mittels Rasterelektronenmikroskopie untersucht, da hier im Vergleich zur Lichtmikroskopie der Kontrast und die Tiefenschärfe besser sind. Im Idealfall zeigen diese den Bruch der Matrix, aus der unterschiedlich lange Faserbruchstücke, ähnlich einer „Bürste“, herausragen.
Bedeutsam für die Anwendung faserverstärkter Sprödmatrixverbunde ist auch ihre Fähigkeit, Stoß- oder Schlagenergie zu absorbieren. Diese Eigenschaft wird durch die Schlagzähigkeit oder – im Falle von standardmäßig gekerbten Proben und hohen Verformungsgeschwindigkeiten – die Kerbschlagzähigkeit beschrieben. Man spannt einen länglichen Quader der Materialprobe ein und lässt einen Pendelhammer mit einer definierten kinetischen Energie auf die Probe auftreffen, sodass die Probe durchschlagen wird. Der Hammer schwingt nach Durchschlagen der Probe bis zu einer bestimmten Höhe nach. Je geringer die Nachschwinghöhe, desto mehr Energie hat die Probe absorbiert. Daraufhin wird die Schlag- oder Kerbschlagarbeit berechnet. In der Praxis hat sich gezeigt, dass Zähigkeit und Sprödigkeit eines Werkstoffes nicht nur vom Werkstoff, sondern auch von den Beanspruchungsbedingungen abhängen. Dem trägt der Schlag- oder Kerbschlagversuch Rechnung.
Im Falle von Verbundwerkstoffen, bei denen in einem ausgewählten Spektralbereich Transparenz angestrebt wird, werden Transmissionsmessungen durchgeführt, das heißt, es wird die Schwächung der Strahlung beim Durchgang durch eine Materialprobe definierter Dicke bestimmt.
Durch die eingebetteten Fasern eröffnen sich Möglichkeiten der Schadensdetektion. Sind die Fasern elektrisch leitfähig, können unidirektional eingebettete Langfasern an den Stirnflächen des Bauteils kontaktiert werden. Die elektrische Leitfähigkeit oder der Ohmsche Widerstand gibt dann Aufschluss über die Menge an gebrochenen Fasern, da durch den Faserbruch der Ohmsche Widerstand zunimmt, die elektrische Leitfähigkeit aber abnimmt. Im Falle transluzenter Verbunde kann die Verschlechterung der optischen Transmission, das heißt die Verschlechterung des Verhältnisses von einfallender zu austretender Strahlungsintensität, zur Schadensdetektion herangezogen werden. Aus diesen „Online-Überwachungsmethoden“ ergibt sich die Möglichkeit zur Versagensprognose. Vorgeschädigte Bauteile können rechtzeitig ausgetauscht werden.
Die Fa. Schott Glaswerke hat Anfang der 1990er Jahre in Zusammenarbeit mit der Universität Karlsruhe und TU Berlin ein mit Kohlenstofflangfasern oder Siliziumcarbidfasern verstärktes Glas unter dem Namen Fortadur® auf den Markt gebracht. Das Material ist aufgrund der schwarzen Verstärkungsfasern schwarz gefärbt. Die Matrix bildet in der Regel ein Borosilikatglas, das eine hohe Temperaturwechselbeständigkeit aufweist. Borosilikatglas ist auch als Jenaer Glas® für seine Hitze- und Thermoschockbeständigkeit im Küchen- und Laborbereich bekannt, wo es beispielsweise zur Herstellung von Glasfiltern, Filterscheiben oder Magnetrührstäbe verwendet wird.
Fortadur® wird als schlag-, bruch- und verschleißfest, thermisch stabil bis +1200 °C und chemikalienbeständig beworben. Es weist eine geringe Dichte und einen hohen Elastizitätsmodul auf. Als Anwendungen werden maschinenbautypisch stark beanspruchte Elemente, wie Umlenkfinger und Abstreifplatten, genannt. Die mechanische Abriebfestigkeit soll mit der von stahlbewehrtem Beton vergleichbar sein. Es eignet sich als Konstruktionswerkstoff im Maschinenbau, Automobilbau, Bauwesen und der Chemieindustrie für Spezialanwendungen. Aufgrund seiner geringen Wärmeleitfähigkeit werden daraus zum Beispiel Greifer für heiße Teile in der Glasherstellung, Flaschenindustrie oder im Hüttenwesen hergestellt. Auch Gehäuse für optische Komponenten und Bremsbeläge können daraus gefertigt werden. Transluzente, also für sichtbares Licht durchscheinende Verbundwerkstoffe, erweitern die mögliche Anwendungspalette im Bereich des Architekturleichtbaus durch Reduzierung der Bauteildicke bei gleichbleibender Festigkeit und Bruchtoleranz. Auch als ballistischer Schutz gegen Geschosse oder im Bereich Arbeitssicherheit kann das Material eingesetzt werden. Bearbeiten lässt es sich mit diamantbewehrten Werkzeugen durch Sägen, Drehen oder Schleifen.
Faserverstärkte Werkstoffe – ein breites Feld mit Zukunftspotenzial
Faserverstärktes Glas schließt die Lücke zwischen faserverstärkten Kunststoffen, deren Einsatzgrenze auf Temperaturen unter +300 °C beschränkt ist, und faserverstärkten Keramiken, die in der Herstellung vergleichsweise teuer und aufgrund ihrer höheren Dichte auch relativ schwer sind. Die herausragenden Eigenschaften ermöglichen den Einsatz für Spezialanwendungen, bei denen es auf hohe Festigkeit in zum Teil extremen Temperaturbereichen ankommt.
Ausgezeichnete Thermoschockbeständigkeit und Abriebfestigkeit ermöglichen verschleißfeste Bauteile. Durch Einbringen von Sensoren kann die Bauteilfunktion online überwacht und Wartungsintervalle dementsprechend ausgerichtet werden. Zudem lässt sich die Transparenz zumindest teilweise erhalten, indem die optischen Eigenschaften der Faser- und Glasmatrixkomponente abgestimmt werden in Verbindung mit geeigneten Faserbeschichtungen. Dies erweitert nochmals das Einsatzspektrum.
Bild-Quellen: Beitragsbild | © Mahlebashieva – stock.adobe.com REM-Aufnahme der Bruchkante eines glasfaserverstärkten Kunststoffs | © HaefnerP, CC BY-SA 4.0 <https://creativecommons.org/licenses/by-sa/4.0>, via Wikimedia Commons Faserverstärkte Keramik mit Siliciumcarbid-Fasern | © MT Aerospace AG, Augsburg, CC BY-SA 4.0 <https://creativecommons.org/licenses/by-sa/4.0>, via Wikimedia Commons In Epoxidharz eingebundene Glasfasern im Automobilbereich | © fabrus – stock.adobe.com