In puncto Wirtschaftlichkeit ist die Kalandriertechnik nicht nur beim Herstellen von Stoffen, Textilien und Papier sowie deren Oberflächengüten alternativlos. Auch bei der Formgebung von Platten und Folien aus PVC und anderen Polymeren in großen Produktionslosen spielt das Walzverfahren seine Vorteile aus. Wie alles begann, wann die großen Entwicklungssprünge einsetzten und was diese Verarbeitungstechnik heute leistet, beschreibt dieser Beitrag kurz und prägnant.
Die Bezeichnung dafür kommt, mit einem Umweg über das Französische calandre, aus dem Griechischen κύλινδρος/kylindros, mit der ursprünglichen Bedeutung „Rolle”. Die Zylinder genannte geometrische Form erhielt ihren Namen aus der gleichen Wortwurzel, mit einem Kalender hat dies aber so gut wie nichts zu tun.
Stoffe und Textilien – die Anfänge des Kalanders
Verfahren, die als Vorläufer der Kalandrierung bezeichnet werden könnten, gehen zurück auf die Textil- und Papierherstellung vor sehr langer Zeit. Im alten China wurden zum Beispiel große Steine abgerundet und deren Oberfläche glattgeschliffen, um damit gewebte Stoffe zu pressen. So konnten die Gewebe geglättet, gegen Wind und Wasser abgedichtet werden und erhielten eine Oberfläche von besonderem Glanz. Einer der bekanntesten mit dieser Technik veredelten Stoffe ist das Satin, das seinen Namen von dem damaligen Herstellungs- oder Handelsort Tsen-Tung, heute Quanzhou, erhalten hat.
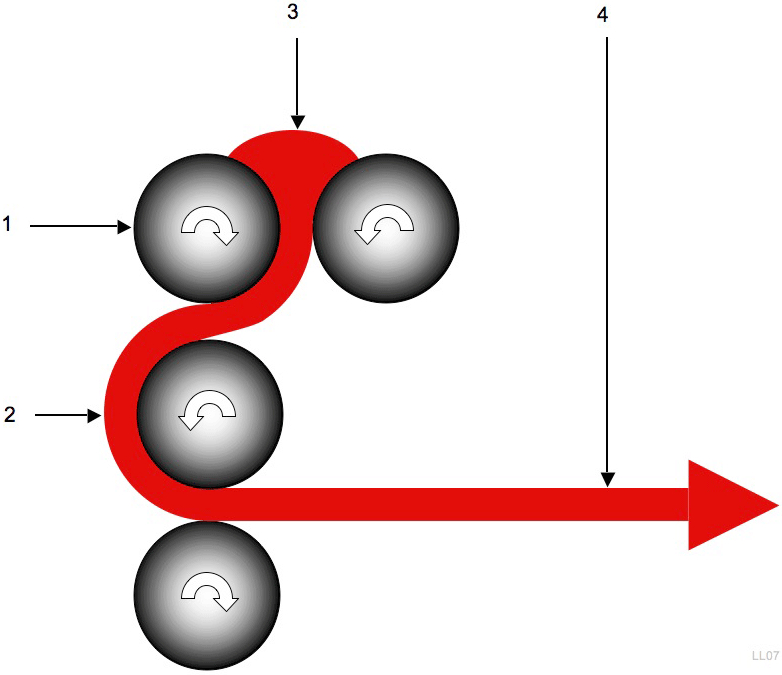
Die ersten bekannten Kalander, also Maschinen, in denen der Druck auf das Werkstück durch mehrere rotierenden Rollen ausgeübt wird, wurden im 16. und 17. Jahrhundert bei der Herstellung der damals weltberühmten flämischen Stoffe eingesetzt.
Kalander bestehen meist aus zwei bis vier Rollen, je nach Bauart können es aber auch wesentlich mehr sein. Die rotierenden Rollen des Kalanders bestehen je nach Verwendungszweck meist aus Stahl oder Schalenhartguss mit großer Härte und Zähigkeit und sind je nach Verwendung in unterschiedlichen Konfigurationen angeordnet. Übliche Bauformen sind I-, F-, L und Z-Kalander. Die Bezeichnung der Bauformen resultiert aus der Positionierung der einzelnen Rollen in der Seitenansicht der Maschine und der Materialzuführung.
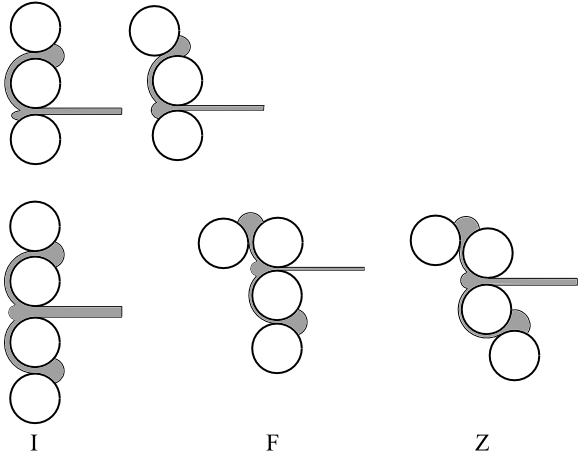
Abstand und Material der beheizten und polierten Rollen wird durch das zu verarbeitende Material (Gewebe, Papier, Kunststoffschmelze, Gummi und Metalle) und dessen angestrebte Dicke oder Struktur bestimmt. Auch wenn der Name es suggeriert, sind die Rollen nicht völlig zylindrisch. Vielmehr sind sie in der Mitte leicht verdickt, um zu kompensieren, dass sie sich unter ihrem eigenen Gewicht durchbiegen, und haben somit eine leichte Fass-Form. Diese Verdickung wird alternativ als Bombage bezeichnet. Um den Lauf der Rollen zu beruhigen, wird oft ein Anti-Vibrations-Compound in die Innenseite der Rolle gegeben.
Papierherstellung
Wie bereits die satinierten Stoffe, wurde auch Papier zuerst in China hergestellt, laut historischen Quellen vor etwa 2.000 Jahren. Dabei wurde ein Brei aus verschiedenen pflanzlichen Fasern und Leim und Wasser erzeugt, die festen Bestandteile abgeschöpft und zwischen Platten gepresst oder gehämmert.
Als das Papier im späten Mittelalter über die arabische Welt nach Europa gelangte, galt es gegenüber dem Pergament als minderwertiges Material, das nicht für handgeschriebene Urkunden verwendet wurden durfte. Als um 1450 durch Johannes Gutenberg der Buchdruck in Europa erfunden wurde – in Ostasien gab es diesen im kleinerem Maßstab schon Jahrhunderte vorher – änderte sich aber schlagartig der Bedarf an Papier, und auch hier ermöglichte das Kalandrieren die Massenproduktion von Papier und damit auch die Verbreitung von Informationen.
Der Kalander glättet das Papier und stellt eine einheitliche Dicke sicher, wie es zum Beispiel für den Buchdruck erforderlich ist, aber auch bei der Herstellung von Papierkondensatoren für die Elektrotechnik historisch von Bedeutung war.
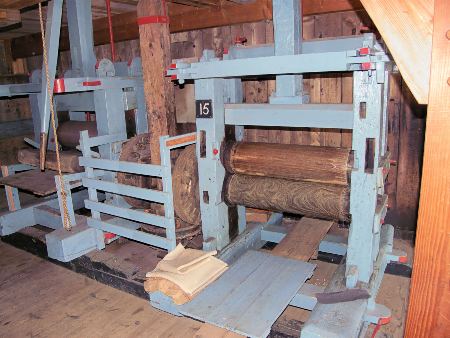
Je nach Anforderung kann das Papier noch weiter kalandriert werden. Zur Herstellung von maschinengestrichenem (MF) Papier wird auf das maschinengeglättete Papier noch Bindemittel, „Strich“ genannt, aufgetragen, um dessen Bedruckbarkeit zu verbessern. Eine Form des MF-Papiers ist das Hochglanzpapier, bei dem eine zusätzliche Schicht aus Pigmenten und Bindemitteln auf das Papier aufgebracht wird, um ihm Glanz zu geben. Eine aus mehreren Kalandern bestehende Maschine, die im nachfolgenden Prozess der Papierveredelung arbeitet, wird auch als Superkalander bezeichnet. Eine der Techniken, um die Oberflächenqualität von Papier zu verbessern, ist die Satinage, bei der mehrere beheizte Glättwalzen aus Stahl die Papieroberfläche noch weiter glätten.
Beschichtete Gewebe und Laminierung von Textilien
Eine der ersten praktischen Anwendungen des Kalandrierens von Kunststoffen war die Herstellung von laminierten Geweben, um die Stabilität des tragenden Gewebes mit der Dichtigkeit und den chemischen Eigenschaften des Kunststoffs zu verbinden.
In Büros, Schulen oder zuhause wird mit einem Laminiergerät ein ähnliches Verfahren benutzt, in dem eine thermoplastische Folie auf Papier oder ähnliche Materialien aufgebracht wird.
Einer der ersten Kalander – er enthielt vier Rollen – wurde im Jahr 1836 von den US-amerikanischen Erfindern Edwin M. Chaffee und Charles Goodyear entwickelt, um wasserdichte, gummierte Postsäcke herzustellen. Da die Kautschuktechnik zu diesem Zeitpunkt aber noch nicht ausgereift war, war das aufgetragene Gummi oft noch klebrig und die Säcke dadurch unbrauchbar. Es dauerte daher noch mehrere Jahrzehnte, bis die Kautschuk-Herstellung reproduzierbar genug war, dass Gummi wirtschaftlich zur Laminierung von Textilien genutzt werden konnte.
Als dann 1874 der erste Kalander zur Beschichtung von Gewebe erfolgreich eingesetzt wurde, war dies der Startschuss für die Massenproduktion von beschichteten Geweben. Dazu gehörten Abdeckplanen, aber auch Fließbänder, was die industrielle Revolution noch einmal weiter beschleunigen sollte. Beschichtungs-Kalander sind heute meist in der Z-Form konstruiert.
Folienherstellung
Während Beschichtungskalander genutzt werden, um Gewebe zu beschichten, werden Schmelzkalander bei der Folienherstellung eingesetzt. Mit der Entwicklung der chemisch hergestellten Polymere und deren rapide wachsende Produktion in der ersten Hälfte des 20. Jahrhunderts waren kunststofftechnische Verfahren gefragt, um sie in großen Mengen weiterzuverarbeiten, etwa zu Folien für Sitzbezüge, Tischdecken, Abdeckplanen oder zur Innenausstattung für die Automobilindustrie. So bot sich das Kalandrieren als Prozess für die Massenherstellung von Folien, Trägermaterialien für Klebebänder und dünnen Platten aus Thermoplasten an.
Verschiedene deutsche und amerikanische Hersteller entwickelten in den 1930er Jahren Kalandrierverfahren, mit denen das bei +120 bis +150 °C gut verformbare Polyvinylchlorid (PVC) bearbeitet werden konnte. Auch heute noch ist PVC der am häufigsten verarbeitete Thermoplast in diesem Verfahren. Diese Methode zur Folienherstellung ist preisgünstiger als die Extrusion, mit der etwa Schläuche, Kunststoffrohre und Stäbe gefertigt werden, stellt aber besondere Anforderungen an den Werkstoff.
So können etwa Polymere mit einer zu dünnflüssigen Schmelze, wie beispielsweise manche Formen des Polyethylens (PE), nicht verarbeitet werden. Weitere gut zu verarbeitende Materialien sind Acrylnitril-Butadien-Styrol-Copolymer (ABS) und Polystyrol (PS). Auch manche Metallfolien können in einem Schmelzkalander hergestellt werden, wie etwa Stanniol, das historisch durch Kalandrieren von geschmolzenem Zinn erzeugt wurde. Heutzutage spielt diese Methode allerdings gegenüber der Herstellung im Walzwerk nur noch eine geringe Rolle.
Der Abstand zwischen den Rollen des PVC-Kalanders bestimmt die Dicke des Produkts, die bei PVC im Bereich zwischen 75 µm und 800 µm liegt, aber es lassen sich so auch PVC-Platten für Bodenbeläge mit einer Dicke von bis zu 5 mm herstellen.
Vor allem kalandrierte Platten aus Polystyrol auf Basis Styrol-Butadien zeichnen sich durch ihre außergewöhnliche Härte und Steifigkeit aus. Sehr dünne Plastikfolien dagegen werden zumeist im Blasextrusionsverfahren hergestellt, bei dem geschmolzener Kunststoff, meist Polyethylen, durch eine Düse geblasen und danach gewalzt und aufgewickelt wird. Je nach Gehalt an Weichmachern werden zur PVC-Verarbeitung F- oder L-Kalander benutzt. Dazu können die weiteren Produkteigenschaften durch Anpassung der Temperatur und der Geschwindigkeit des Kalandrierens sowie die Struktur der Rollen verändert werden.
Resümee
Auch wenn der Begriff Kalandrieren wenig geläufig ist, begegnen einem die Produkte des Kalandrierens überall – leider allzu oft auch in Form von Plastikmüll. Während das Kalandrieren dem Rohmaterial in der Papier- und Textilindustrie neue Oberflächeneigenschaften verleiht, verschafft es dem Kunststoff eine neue Form.
Auf diese Weise haben Produkte des Kalanders nicht nur weite Verbreitung gefunden, sondern haben in Form von Fließbändern und Endlospapier auch entscheidend beim Wachstum der industriellen Produktion und Verbreitung und Weitergabe von Informationen mitgeholfen.
Bild-Quellen: Beitragsbild | © hxdyl – stock.adobe.com Kalander-Prozess zur Folienherstellung | © Die Autorenschaft wurde nicht in einer maschinell lesbaren Form angegeben. Es wird LaurensvanLieshout als Autor angenommen (basierend auf den Rechteinhaber-Angaben)., Public domain, via Wikimedia Commons Beispiele für Rollenanordnungen bei Kalandern | © kifo, Public domain, via Wikimedia Commons Papiermühle "De Schoolmeester | © Rasbak, CC BY-SA 3.0 <http://creativecommons.org/licenses/by-sa/3.0/>, via Wikimedia Commons