Thermoplastische Elastomere (TPE), weniger gebräuchlich ist die Bezeichnung „Elastoplaste“, sind durch Erwärmen verformbar. Gleichzeitig besitzen sie die elastischen, gummiartigen Eigenschaften der Elastomere. Doch welche Anwendungsmöglichkeiten können daraus erschlossen werden? Hier erfahren Sie mehr.
Thermoplastische Elastomere – eine Definition
Nach der DIN EN ISO 18064:2015-03 sind Thermoplastische Elastomere (TPE) eine eigene Klasse von Polymeren, die dadurch charakterisiert ist, dass sich diese Materialien im Gebrauchstemperaturbereich „entropie-elastisch“ verhalten. Doch was bedeutet das?
Die Entropie ist, vereinfacht ausgedrückt, ein Maß für die molekulare „Unordnung“. Die Ordnung ist bei Elastomeren niedrig, weil die Makromoleküle nicht gerichtet sondern verknäult vorliegen. Die molekulare Ordnung erhöht sich, wenn durch Zugbelastung des Elastomers die Makromoleküle gestreckt und damit gerichtet werden und sich dadurch die Verknäuelung verringert. Denn dieses bedeutet zugleich eine Erhöhung der molekularen Ordnung des Elastomers.
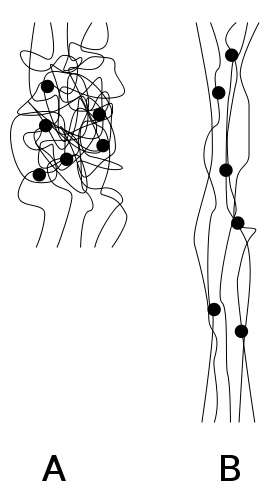
Beim Nachlassen der Zugbelastung gewinnt das entropie-elastische Polymer sowohl seine vorherige, geknäulte innere Form wie damit auch seine ursprüngliche, äußere Gestalt wieder zurück.
Außerhalb des Gebrauchstemperaturbereichs verliert der Kunststoff seine entropie-elastischen Eigenschaften. Bei Erwärmung oberhalb einer bestimmten Temperatur, die dem jeweiligen Thermoplastischen Elastomer eigen ist, schmilzt es; unterhalb einer bestimmten Temperatur ist das „Entknäueln“ nicht mehr möglich. Der Kunststoff verliert dann seine Elastizität, er wird hart und bricht bei Belastung.
Die vielseitige TPE-Kunststofffamilie
Viele Produkte, beispielsweise Soft-Touch-Griffe von Stiften, Werkzeugen oder Zahnbürsten, bestehen aus thermoplastischen Elastomeren. Kabelummantelungen, Gehäuse für Haushaltsgeräte oder Armaturen aus dem Sanitärbereich werden ebenfalls aus TPE hergestellt.
Die häufigsten Anwendungen finden sich jedoch im Automobilbereich. Allein ein Drittel der hergestellten TPE-Materialien wird in Radkappen, Innenverkleidungen oder Karosseriedichtungen verarbeitet.
Im Jahr 2015 wurden circa 6,5 Millionen Tonnen an Thermoplastischen Elastomeren hergestellt und die Tendenz ist steigend.
Geschickte Kombinationen aus zwei Polymerkomponenten
Typisch für Thermoplastische Elastomere ist ihre Zusammensetzung aus einer „weichen“ und einer „harten“ Komponente. Sie können auf unterschiedliche Weise miteinander kombiniert werden. Eine Verarbeitungsvariante besteht darin, Elastomere, wie Kautschuk, mit Thermoplasten, wie Polyamid (PA) oder Polypropylen (PP) zu Polymerblends zu vermischen.
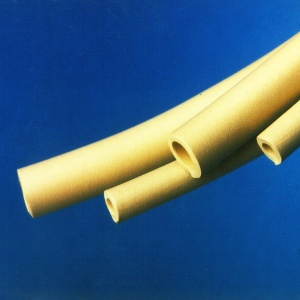
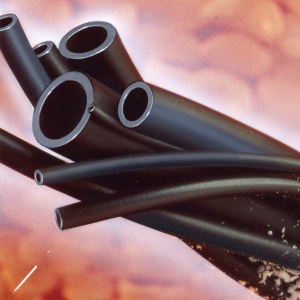
Solche Mischungen werden auch als Elastomer-Legierungen bezeichnet. Durch exakte Einstellung der Mischverhältnisse können maßgeschneiderte TPE-Werkstoffe mit sehr genau definierten Eigenschaften hergestellt werden. Die Zugabe von Additiven und Füllstoffen lässt zudem ein weiteres Feintuning zu.
Es ist aber ebenso möglich, verschiedene Monomereinheiten gemeinsam zu polymerisieren. In einem solchen als Copolymerisat bezeichneten Kunststoff wechseln sich thermoplastische und elastomere Monomeranteile ab. Dabei wird zwischen Block-Copolymeren, die aus Blöcken der harten sowie der weichen Polymerkomponenten bestehen, und Pfropf-Copolymeren unterschieden. Bei letzteren bildet eine Polymerkomponente die Hauptkette, die Ausgangspunkt für Seitenketten eines anderen Monomertyps darstellt.
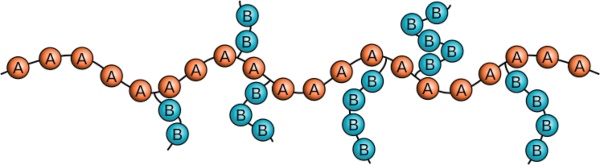
In beiden Varianten sind die thermoplastischen Bereiche durch physikalische Vernetzung reversibel miteinander verbunden. Bei Erwärmung wird die Vernetzung zwischen den Molekülketten aufgehoben, die Molekülketten selber bleiben jedoch erhalten. Makroskopisch gesehen erweicht das Material ohne sich zu zersetzen.
Daher ist auch eine einfache thermische Verarbeitbarkeit gegeben, so dass die Standardverfahren der Kunststoffverarbeitung genutzt werden können. Dazu gehören das Spritzgießen, das Extrudieren und das Blasformen, mit denen die Thermoplastischen Elastomere nach dem Erwärmen in eine bestimmte Form gebracht werden, die sie nach dem Abkühlen beibehalten.
Thermoplastische Elastomere vereinen unterschiedliche physikalische Eigenschaften
Generell zeichnen sich Thermoplastische Elastomere durch eine hohe Flexibilität sowie eine hohe reversible Dehnfähigkeit in einem sehr weiten Temperaturbereich aus. Weiterhin sind die hohe Festigkeit, Schlagzähigkeit und Kerbschlagzähigkeit charakteristisch, weshalb diese Werkstoffklasse im Vergleich zum reinen Elastomer oder reinen Thermoplast robuster ist.

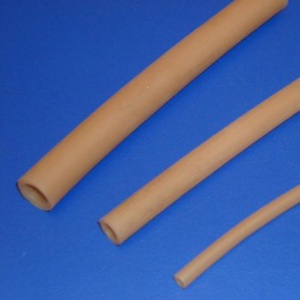
Neben der Festigkeit kann ein thermoplastischer Kunststoff durch einen hohen Elastomer-Anteil weicher werden, ohne dass ihm dafür Weichmacher zugesetzt werden müssten. Aus diesem Grund werden Schläuche für die Pharma- und Lebensmittelindustrie sowie Medizintechnik, die den hohen Anforderungen der FDA genügen müssen, aus weichmacherfreien Thermoplastischen Elastomeren gefertigt.
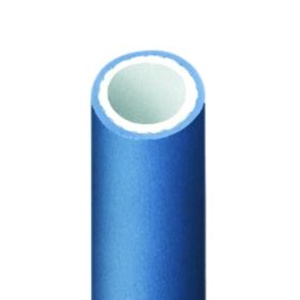
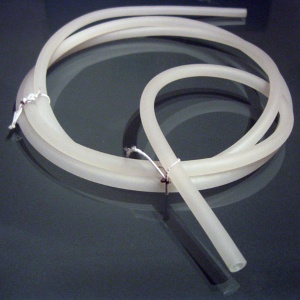
Die chemische Beständigkeit kann durch die Auswahl der Polymerkomponenten sehr spezifisch bestimmt werden. Ein weiterer großer Vorteil ist die einfache und damit auch wirtschaftliche Verarbeitbarkeit der aufgeschmolzenen Kunststoffe. Ein weiterer Pluspunkt, der die Verarbeitung betrifft, ist die Möglichkeit, diese Kunststoffe verschweißen zu können. Schließlich, und das macht den Einsatz Thermoplastischer Elastomere für Profile und Oberflächen beliebt, ist ihre Abriebfestigkeit sehr gut.
Gibt es Nachteile?
Neben den vielen Vorteilen gegenüber reinen Elastomeren haben Thermoplastische Elastomere auch Nachteile. So sind sie zwar reversibel dehnfähig, erreichen aber die Dehnfähigkeit von reinen Elastomeren, also gummiartigen Materialien, nicht.
Auch der Einsatz bei höheren Temperaturen ist begrenzt. Sie erweichen bereits bei Temperaturen oberhalb von 110 °C und verlieren ihre Elastizität.
Schließlich zeigen Thermoplastische Elastomere unter Belastung eine höhere Fließneigung auf als sie bei „gewöhnlichen“ Elastomeren zu beobachten ist. Ursache dafür sind die Verringerung oder das gänzliche Fehlen von intermolekularen Vernetzungsbrücken.
Die Vielfalt macht es
Durch die Kombination von verschiedenen Thermoplast-Komponenten entsteht eine große Vielfalt an Kunststoffen. Die DIN EN ISO 18064 teilt Thermoplastische Elastomere nach ihrem chemisch-morphologischen Aufbau in folgende Gruppen ein.
Thermoplastische Polyamid-Polymere (TPA)
Hinter diesen Kunststoffen mit dem Kürzel TPA verbergen sich thermoplastische Kunststoffe, deren harte Komponete aus Polyamid-6- oder Polyamid-12-Monomeren gebildet wird. Diese bilden Blöcke innerhalb der Polymerkette und wechseln sich mit Polyether- oder Polyester-Einheiten als weiche Komponente ab. Thermoplastische Polyamid-Polymere sind typische Vertreter der Block- Copolymerisate. Hieraus werden zum Beispiel Schläuche, aber auch Dichtungen und sogar Zahnräder hergestellt.
Thermoplastische Polyester-Polymere (TPC)
Thermoplastische Polyester-Polymere sind Multiblock-Co-Polymere. Hier wechseln sich entweder verschiedene Polyestereinheiten untereinander ab oder aber Polyester- und Polyethereinheiten. Typische TPC-Produkte sind O-Ringe, Rollen und Riemen oder auch Faltenbälge.
Thermoplastische Styrol-Polymere (TPS)
Bei Copolymeren aus Styrol-Butadien oder Styrol-Isopren-Einheiten bildet der Styrolanteil die weiche Komponente. Die Styrol-Butadien-Einheiten können dabei sowohl als Propf-Copolymere synthetisiert werden wie auch als Blockpolymere.
Durch Pfropf-Copolymerisation mit einem sehr hohen Anteil an Styrol entstehen extrem schlagzähe Kunststoffe. Die Härte von Styrol-Blockpolymeren kann über einen sehr weiten Bereich von weich bis hart eingestellt werden. Thermoplastische Styrol-Polymere werden für Unterlagen, Griffteile, aber auch Vibrationsdämpfer oder Dehnungsfugenbänder eingesetzt.
Thermoplastische Polyurethan-Polymere (TPU)
Thermoplastische Polyurethan-Polymere sind Co-Polymerisate, bei denen Urethane als harte Komponente mit Polyestern oder Polyethern verknüpft werden. Sie sind die Grundlage für Polyester-Urethan-Kautschuke, die vor allem von der Schuhindustrie für die Produktion von Sportschuhen abgenommen werden. Enthalten die Polyurethaneinheiten einen aromatischen Anteil, entstehen sehr harte Werkstoffe, die für Armaturen oder Zahnriemen eingesetzt werden.
Polymerblends (TPO und TPV)
Polymerblends sind Gemische von Kunststoffen, oft werden sie auch Polymerlegierungen genannt.
Zu den Polymerblends gehören die Polyolefin-Blends, die an den Kürzeln TPO oder TPV erkannt werden. TPO steht dabei für unvernetzte, thermoplastische Polymerblends, beispielsweise aus Ethylenvinylacetat (EVA) und Polyvinylidenchlorid (PVDC) oder auch Ethylen-Propylen-Dien-Kautschuk (EPDM) und Polypropylen (PP).
Mit dem Kürzel TPV werden hingegen vernetzte Blends aus Polyolefinen, wie Polyethylen und Polypropylen, gekennzeichnet. Polyolefin-Blends werden vorzugsweise im Fahrzeugbau für Innenverkleidungen, Stoßstangen und Zierleisten eingesetzt.
Vor allem ist die Härte entscheidend
Bei der Auswahl eines Thermoplastischen Kunststoffs ist nicht nur das chemische Verhalten, sondern vor allem die Härte ein entscheidendes Kriterium. Für Materialwissenschaftler und Praktiker ist die Einteilung nach der Härte auch sehr viel praxisnäher als die Einteilung nach der chemischen Struktur. Sie wird für Kunststoffe als „Shore-Härte“ angegeben, dem die Eindringtiefe von genormten, unterschiedlich geformten Prüfstiften bei 22 °C ± 2 °C unter bestimmten Belastungen zugrunde liegt. Sie wird mit den Buchstaben A bis D gekennzeichnet, wobei die B- und C-Härten heute keine technische Bedeutung mehr haben und kaum noch gemessen werden.
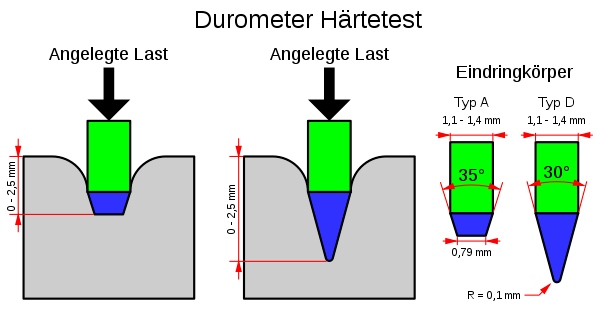
Das Härte-Messverfahren geht auf den US-amerikanischen Ingenieur Albert Ferdinand Shore (1876 – 1936) zurück, der es im Jahre 1915 als verbindliches Werkstoffprüfverfahren etablierte. Es ist bis heute weltweit gebräuchlich und wurde von den Normungen der DIN EN ISO 868, der DIN ISO 7619 (1) sowie der ASTM D2240-00 übernommen.
Die Härte-Skala überstreicht für Thermolastische Kunststoffe wegen der Vielzahl der möglichen Zusammensetzungen einen weiten Bereich, der von keiner anderen Kunststoffklasse erzielt wird.
Er reicht von „sehr weich“ mit der Härte von etwa 30 ° Shore A bis zu einer Härte von 75 ° Shore D und mehr, was sehr harten Kunststoffen entspricht.
Die Vielfalt macht das Recycling schwierig
Die Klasse der Thermoplastischen Elastomere ist eine interessante und sehr umfangreiche Kunststoffklasse. Die Eigenschaften von TPEs können in einem weiten Bereich anwendungsorientiert eingestellt werden.
Die praktisch unbegrenzten Möglichkeiten, ihre Zusammensetzungen zu variieren und sie so dem jeweiligen Zweck optimal anzupassen, führt jedoch zu Problemen beim Recycling von TPE-Materialien, ein Aspekt der bei aller Euphorie für den Einsatz von TPEs Beachtung verdient. Denn recycelbar sind nur sortenreine Kunststoffe. Die Zusammensetzungen von Thermoplastischen Elastomeren sind jedoch meist unbekannt. Vielmals enthalten sie auch noch Zuschlagstoffe, wie Farbpigmente oder Flammschutzmittel.
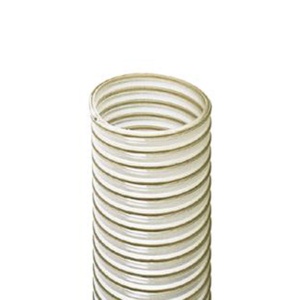
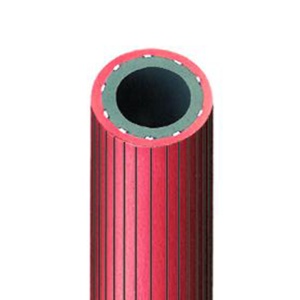
Die Zusammensetzungen analytisch-chemisch zu ermitteln, um TPE-Kunststoffe für ein industrielles Recycling sortenrein aufzubereiten, ist praktisch undurchführbar. Thermoplastische Elastomere unsortiert zusammenzuschmelzen wäre zwar möglich, die physikalisch-technischen Eigenschaften des Schmelzproduktes wären jedoch nicht vorhersehbar. So bleibt derzeit nur die thermische Verwertung, ihre Verbrennung am Ende der Nutzung, als einzig praktikable Lösung übrig.