Das älteste bekannte, von Menschenhand gefertigte Keramikprodukt ist eine figürliche Keramik, die » Venus von Dolní Věstonice «, die 1925 bei archäologischen Grabungen in Südmähren zu Tage gefördert wurde. Das Alter der nur 11 cm hohen, aus Lehm gebrannten Statuette wird auf etwa 25.000 Jahre geschätzt und diente vielleicht kultischen Zwecken. Die Geschichte der Gebrauchskeramik, die Töpferei zur Herstellung von Gefäßen, begann erst vor etwa 9000 Jahren, am Beginn der Jungsteinzeit, wahrscheinlich in Mesopotamien, dem Zweistromland zwischen Euphrat und Tigris. Die dort aufgefundenen Tongefäße waren noch handgeformt, denn die Töpferscheibe ist erst gute 3000 Jahre später erfunden worden. Sie eröffnete den Weg zur handwerklichen Produktion von keramischen Erzeugnissen in größeren Stückzahlen, mit denen nun auch andere versorgt werden konnten. Mit der Erfindung der Glasur, wahrscheinlich durch die Ägypter im 4. Jahrtausend v. Chr., erlebten die Keramiken schließlich einen bedeutenden Qualitätsschub.
Heutzutage sind Keramiken allgegenwärtig, nicht nur in Form des täglich gebrauchten Geschirrs oder als kunstvoll geformten und liebevoll in der Vitrine verwahrten Nippes. Keramiken sind auch zu einem wichtigen Industriewerkstoff geworden, ohne die viele technische Lösungen, die heute selbstverständlich sind, gar nicht möglich geworden wären. Doch was sind technische Keramiken, wofür werden sie eingesetzt und welche Vorteile bieten sie gegenüber Kunststoffen und Metallen?
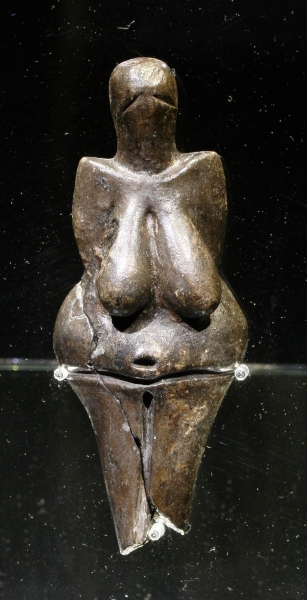
Keramik – was ist das?
Keramik ist ein Produkt aus feingemahlenen und mit Wasser zu einer breiartigen Masse eingesumpften Tonmineralen, das geformt und nach dem Trocknen durch starkes Erhitzen, dem Brennen, verfestigt worden ist. Die Herstellung von Keramik, wie sie heute noch gebräuchlich ist, begann hierzulande im 16. Jahrhundert, als sich Physik, Chemie und Mineralogie aus der Mystik des Mittelalters zu lösen begannen und sich frühwissenschaftliche Erkenntnisse sowohl auf die Auswahl der Ausgangsmaterialen wie auch auf die technologischen Prozesse, vor allem die Brenntechnik, niederschlugen.
Die ältesten, als „Irdengut“ bezeichneten Produkte wurden aus Tonen bei niedrigen Temperaturen von nicht mehr als 700 °C gebrannt. Die Produkte waren porös und wasserdurchlässig. Um vieles härter wurde das bei 1000 °C gebrannte „Steingut“, das aber auch noch porös war. Erst das „Steinzeug“, das sich während des Brennens bei 1200 °C bis 1400 °C durch Sintern verdichtet, war für Wasser undurchlässig. Steinzeug trägt daher noch den Beinamen „Sinterzeug“.
Seine Herstellung konnte erst erfolgen, als es möglich geworden war, derartig hohe Temperaturen zu erzeugen und sie auch über längere Zeit zu halten. Wegen der Beimengungen in den mineralischen Ausgangsstoffen, vor allem Schwermetalloxide, ist Steinzeug mehr oder minder farbig und nicht durchscheinend. So ist das historische „chinesische Porzellan“ nach heutigem Verständnis eher ein Steinzeug, als ein Porzellan, das weiß und durchscheinend ist.
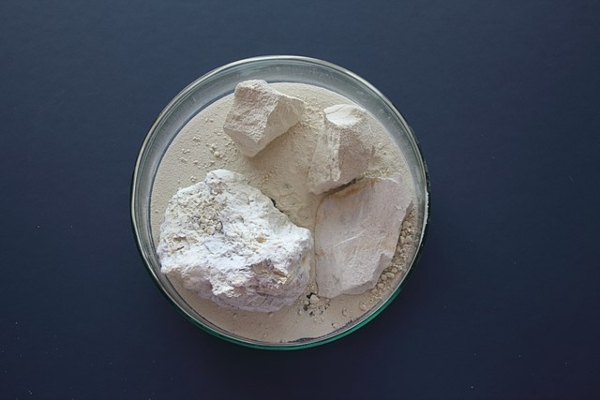
Das weiße Gold – Vom Kaolin zum Porzellan
Porzellan ist ein bei Temperaturen um 1400 °C gebranntes und glasiertes Keramikprodukt aus Kaolin und damit ein Sinterzeug. Seinen Namen „Kaolin“ verdankt das weiche Gestein der chinesischen Region Gao Ling, einem der frühen Fundorte für die „weiße Tonerde“, wie Kaolin auch genannt wird.
Es besteht aus Kaolinit, einem weißen Tonmineral aus hydratisiertem Aluminiumsilikat der formalen chemischen Zusammensetzung Al2Si2O5(OH)4, und enthält, abhängig vom Fundort, noch wechselnde Mengen weiterer Silikate, hauptsächlich Feldspäte sowie Glimmer- und Quarzminerale. Wegen seines hohen Siliziumanteils zählt Porzellan formal auch zu den Silikat-Keramiken.
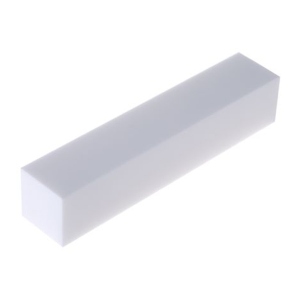
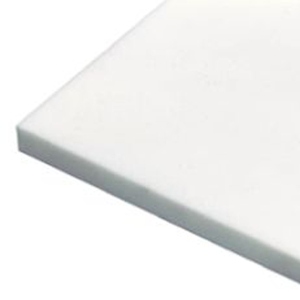
Eins der bekanntesten Porzellane ist das „Meissner-Porzellan“, das als das erste europäische Porzellan gilt und schon seit 1710 produziert wird. Es wurde zu Anfang des 18. Jahrhunderts mit dem wissenschaftlichen Beistand des Gelehrten am Dresdner Hof, Ehrenfried Walther von Tschirnhaus (1651 – 1708), von dem Apothekergehilfen Johann Friedrich Böttcher (1682 – 1719) bei seinen alchimistischen Versuchen erfunden, Gold zu machen.
Gut 50 Jahre später, im Jahre 1763, gründete Friedrich der Große (1712 – 1786) in Berlin die Königliche Porzellan-Manufaktur (KPM), die der Meißner Manufaktur in nichts nachstand und wie diese auch heute noch künstlerische Porzellane fertigt. Von den vielen weiteren Gründungen jener Zeit haben bis heute nur wenige Große überlebt, wie die Porzellanfabrik von Lorenz Hutschenreuther im bayrischen Selb, gegründet 1857, und die Porzellanfabrik von Philipp Rosenthal, gegründet 1879, die zunächst in Werl ansässig war und später nach Selb umsiedelte.
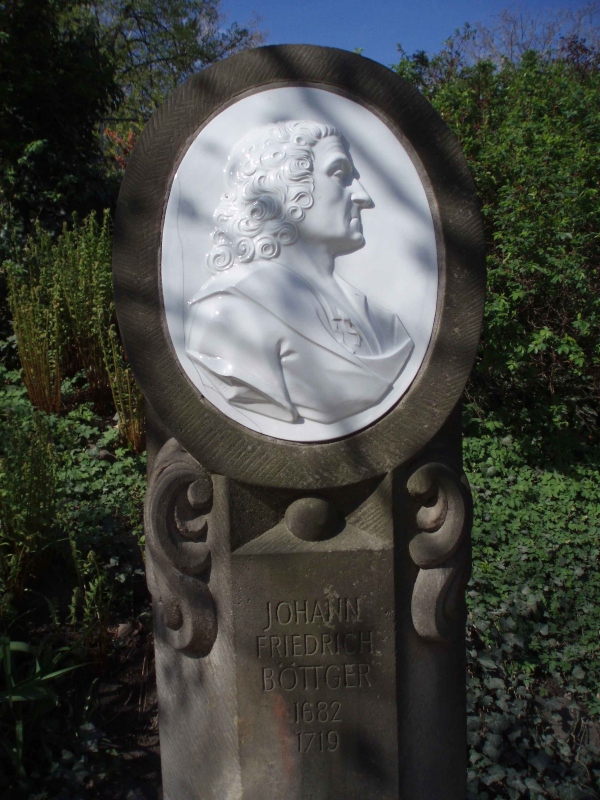
Porzellan – die erste technische Keramik
Porzellan war seit den Anfängen in China bis weit in seine europäische Neuzeit, die mit Böttchers Entdeckung begann, nur ein Material für den Luxus der gehobenen Gesellschaft, für figürliche Porzellane und andere Accessoires, aber auch für reich dekorierte Tafelgeschirre.
Doch die spätestens im 19. Jahrhundert schnell Platz greifende Massenfertigung von Porzellanen in vielen Manufakturen, vor allem in Sachsen, Thüringen und Bayern, und Verbesserungen der Produktionstechnologien, die Erfindung des „Segerkegels“ für die Kontrolle der Brenntemperatur durch den deutschen Chemiker Hermann August Seger (1839 – 1893) im Jahre 1885 ist eine davon, ließen nun auch den bürgerlichen Haushalt an der Schönheit des Porzellans teilhaben.
Dank seiner vielfältigen Eigenschaften fand Porzellan alsbald auch das Interesse der chemischen Industrie, die sich seit dem Ende des 18. Jahrhunderts zu etablieren begann. Denn Porzellan ist nahezu beliebig ausformbar, es ist weitgehend temperaturunempfindlich, glatt und säurefest und damit für Laborgeschirre, wie Schalen, Nutschen, Trichter und Tiegel wie auch für Gefäße zur Aufbewahrung von Chemikalien und für säurebelastete Rohrleitungen ein beinahe ideales Material.
Naheliegend war, dass Porzellan auch in die Sanitärtechnik Eingang fand, für Waschbecken und Waschtische, Bidets und Toiletten, und seither sehr viel für die Aufrechterhaltung häuslicher Hygiene und darüber hinaus im öffentlichen Raum beigetragen hat.
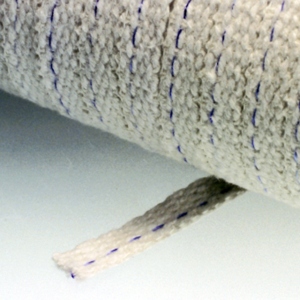

Da Porzellan den elektrischen Strom nicht leitet, war und ist es auch für elektrische Isolatoren gefragt, als temperaturfeste Elektro-Isolationskeramik in vielen elektrischen Geräten und als standfeste Isolierkörper für Hochspannungsanlagen und Freileitungen. Damit ist Porzellan nicht nur mehr Schmuck- und Gebrauchskeramik, sondern zugleich auch die erste Technische Keramik.
… weg vom Porzellan
Ein gewichtiger Nachteil von Porzellan ist die Abhängigkeit seiner Qualität und damit seiner technischen Leistungsparameter von der Zusammensetzung des jeweils verwendeten Kaolins.
Denn Kaolin ist ein natürliches Mineral mit dem Hauptbestanteil Kaolinit, aber mit Beimengungen, die sich in Zusammensetzung und Konzentration fundortabhängig erheblich unterscheiden können.
So war die Entwicklung von Keramiken auf der Basis von reinen Oxiden für die Industrie zunächst eine notwendige Konsequenz, um Kompatibilität der Produkte gewährleisten zu können.
Zugleich war damit aber auch die anwendungsorientierte Optimierung der Keramiken verbunden, die sich in der Vielfalt ihrer Benennungen widerspiegelt, wie Hochleistungskeramik, Strukturkeramik, Konstruktionskeramik, Industriekeramik, Ingenieurkeramik, Funktionskeramik, Schneidkeramik und Biokeramik.
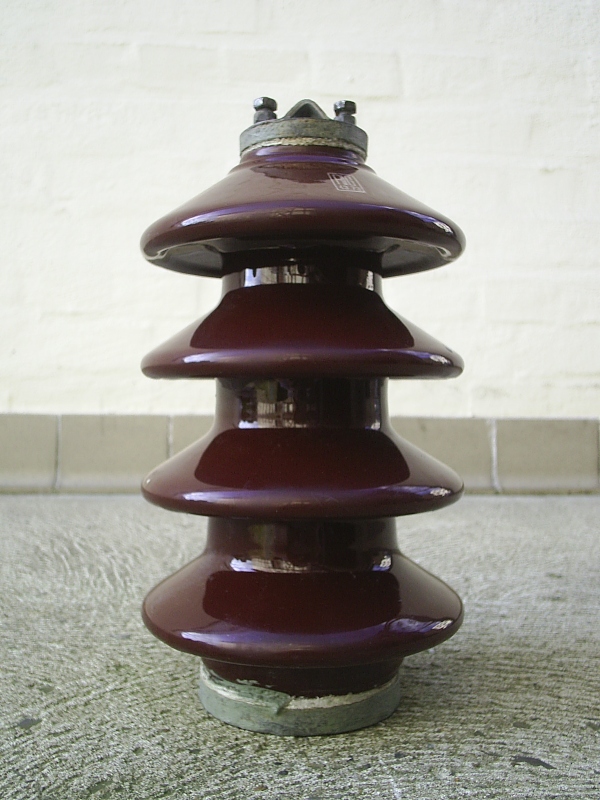
Technische Keramik wird häufig mit Hochleistungskeramik gleichgesetzt, die nach der DIN V ENV 12212 als „hochentwickelter, hochleistungsfähiger keramischer Werkstoff, der überwiegend nichtmetallisch und anorganisch ist und über bestimmte, zweckmäßige Eigenschaften verfügt“ definiert wird. Praktikabler und anschaulicher ist aber immer noch die chemisch-mineralogische Einteilung anhand der Ausgangsstoffe in Oxid-Keramiken und Nichtoxid-Keramiken.
Sintern – aus Pulvern werden Keramiken
Oxid-Keramiken werden durch Sintern von reinen Metalloxiden wie Aluminium-, Magnesium-, Zirkonium- oder Titanoxid (Al2O3, MgO, ZrO2,TiO2) hergestellt, wobei Korngröße der Oxide und Sinterbedingungen die technischen Eigenschaften bestimmen. Die Verwendung von Oxid-Keramik reicht vom Einsatz als Dichtungen für Wasserarmaturen und Zündkerzen für die Automobilindustrie über Formteile für die Elektronik bis zu hochtemperaturfesten Kleinteilen, wie Schrauben, Muttern und Unterlegscheiben für den Maschinen- und Apparatebau. Ihre Weiterentwicklungen sind die Dispersions-Keramiken aus synthetischen Mischoxiden, wie Aluminiumtitanat (Al2TiO5), oder aus Gemischen der reinen Metalloxide, wie Aluminiumoxid (Al2O3) mit Zirkoniumoxid (ZrO2) oder Yttriumoxid (YtO2).
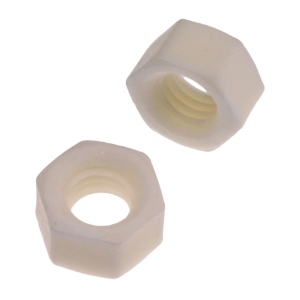
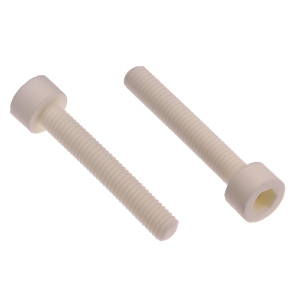
Wegen der hohen mechanischen Belastbarkeit und Abriebfestigkeit dieser Keramiken bei gleichzeitiger Biokompatibilität und Alterungsbeständigkeit werden sie vor allem als Struktur-Keramiken in der medizinischen Prothetik, für künstliche Gelenke, eingesetzt. Die Gruppe der technisch bedeutenden Nicht-Oxid-Keramiken umfasst zwei Stoffklassen: Carbide vom Typ MexCy, hauptsächlich mit Me = Hafnium, Silizium, Tantal, Vanadium oder Wolfram, und Nitride vom Typ MexNy, hauptsächlich mit Me = Bor, Silizium oder Titan. Sie unterscheiden sich in ihren physikalisch-technischen Parametern erheblich von denen der Oxid-Keramiken. Ursache dafür ist das Überwiegen von kovalenten Bindungen.
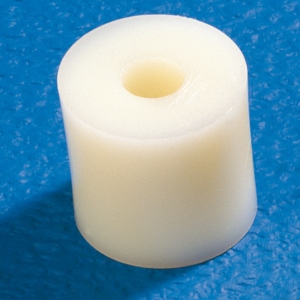
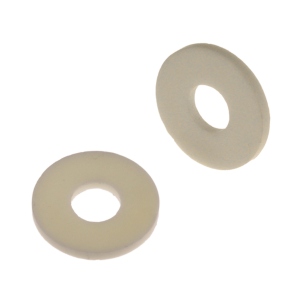
Nichtoxid-Keramiken sind deshalb sehr hart, viele vergleichbar mit Diamant, thermisch hochbelastbar und auch bei sehr hohen Temperaturen noch chemisch äußerst stabil. Dem gegenüber steht ihre geringe Duktilität, was geringer Dehn- und Verformbarkeit und hoher Sprödigkeit entspricht. Ihre Formgebung erfolgt ebenso wie bei Oxidkeramiken durch Sintern. Hierfür sind jedoch nicht nur Temperaturen oberhalb von 2000 °C erforderlich, sondern auch hohe Drucke und geringe Partikelgrößen des gepulverten Ausgangsmaterials.
Carbide und Nitride finden als Dichtungen, Lager, Schrauben und Muttern im Maschinen-Sonderbau ein weitreichendes Einsatzgebiet, ebenso als Schneidkeramiken für Bohrwerkzeuge. Nitride zeichnen sich zusätzlich durch höhere Druckfestigkeit aus.
… der Unterschied zu Kunststoffen und Metallen
Technische Keramiken unterscheiden sich von den „klassischen“ Werkstoffen, den Metallen und Kunststoffen, grundlegend. Sieht man von Edelmetallen ab, erliegen die meisten Metalle vor allem der chemischen Korrosion, können aber hohen Temperaturen meist gut widerstehen. Bei Kunststoffen ist die Thermostabiliät äußerst niedrig, sie erreicht mit PTFE kaum 300 °C. Dafür verhalten sich viele Kunststoffe gegenüber Chemikalien inert.
Für die meisten ingenieur-technischen Aufgaben lassen sich mit den Möglichkeiten, die klassische Werkstoffe heutzutage bieten, gangbare und auch ökonomisch tragbare Lösungen finden. Die klassischen Werkstoffe versagen aber unter extremen Bedingungen, wenn sehr unterschiedliche Anforderungen an das Material gestellt werden. Hier beginnt das Einsatzfeld technischer Keramiken, von denen viele als zweckoptimierte Leistungskomponenten für die Medizintechnik, für den Maschinen- und Chemieanlagenbau und für die Luft- und Raumfahrt bereits unverzichtbar geworden sind. Weitere werden sicherlich noch folgen.
Bildquellen: Venus von Dolní Věstonice | © Petr Novák – de.wikipedia.org Kaolinit | © Marion Halft – de.wikipedia.org Denkmal | © Hejkal – de.wikipedia.org Keramikisolator | © Chris320 – de.wikipedia.org