Wir alle kennen Kunststoffe in den verschiedensten Formen. Sie begegnen uns täglich als Schläuche, Folien, Flaschen, Kanister, Dosen und andere Behältnisse, aber ebenso auch als stoßmindernde Formteile und Schaumstoffe für den Transport empfindlicher Güter, als elektrische Isoliermaterialien und als Halbzeuge, wie Rohre und Profile sowie Kunststoffplatten. Wie die Verarbeitung erfolgt, hängt vor allem davon ab, um welchen Kunststoff es sich handelt.
Der Kunststofftyp bestimmt die Verarbeitungsmöglichkeiten
Polymere können nach ihrer polymeren Struktur in drei Klassen eingeteilt werden. Je nach Klasse unterscheiden sich die Optionen zur Kunststoffverarbeitung.
Duroplaste
Duroplaste, seltener auch als Duromere oder Thermodure benannt, sind, wie schon die Bezeichnung ausdrückt (lat.: durus = hart), sehr feste, harte Werkstoffe. Nur vor ihrer Polymerisation, also noch vor der Aushärtung, können Duroplaste in die gewünschte Form gebracht werden. Eine spätere Umformung ist hingegen nicht mehr möglich. Die weitere Bearbeitung erfolgt dann durch spanabhebende Verfahren, wie Drehen, Bohren oder Fräsen. Die meisten Duroplaste lassen sich auch miteinander verkleben.
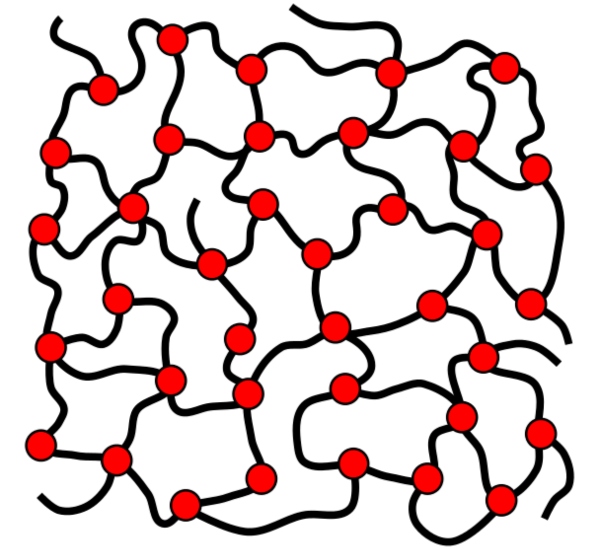
Zur Gruppe der Duroplaste zählen jene Kunststoffe, die allgemein als „Harze“ bezeichnet werden, wie Epoxidharze (EP) und Melamin-Phenolharze (MPF). Der erste duroplastische Werkstoff war das „Bakelit“, ein Phenol-Formaldehydharz (PF), das bereits im Jahre 1905 von dem belgischen Chemiker Leo Hendrik Baekeland (1863 – 1944) in den USA entwickelt wurde und noch heute weltweit produziert wird. Nach dieser Einteilung sind auch ungesättigte Polyesterharze (UP) den Duroplasten zuzuordnen. Sie alle zeichnen sich durch eine engmaschige, kovalente Vernetzung aus, die deren Härte und thermische Stabilität bedingt.
Elastomere
Elastomere sind gummiartige, elastische Kunststoffe. Auch hier verrät der Name bereits einiges über die Eigenschaften dieser Kunststoffgruppe, die in vielem denen des Naturkautschuks entsprechen. Elastomere sind formstabil. Da sie jedoch weniger stark vernetzt sind als Duroplaste, können sie unter Einwirken einer äußeren Zugkraft zwar gestreckt werden, kehren aber mit dem Nachlassen der angreifenden Kräfte wieder in ihre Ursprungsform zurück.
Das bedeutet: Einmal synthetisiert, ist die äußere Form eines elastomeren Werkstoffs nicht mehr dauerhaft veränderbar.
Sie sind auch deutlich weniger thermostabil als Duroplaste. Zu den Elastomeren gehören alle Synthesekautschuke, wie Chloroprenkautschuk (CR), Ethylen-Propylen-Dien-Kautschuk (EPDM) und Silikonkautschuk (SI). Fast alle Elastomere können jedoch durch Verkleben weiter verarbeitet werden.
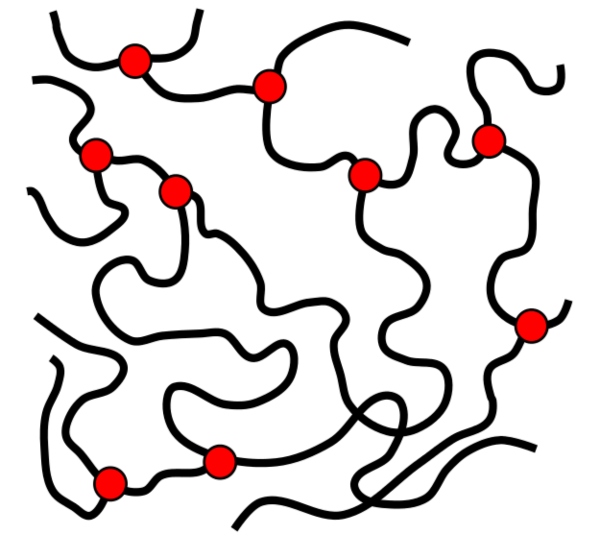
Thermoplaste
Ganz andere Eigenschaften zeichnet die Klasse der Thermoplaste aus. Die Bezeichnung lässt bereits auf einige ihrer wesentlichen Merkmale schließen: Sie erweichen bei Erwärmung und schmelzen, ohne sich dabei zu zersetzen. Die Ursache für diese bleibende Reversibilität zwischen fest und flüssig ist, dass die Polymerstränge im Makromolekül nicht zu einem dreidimensionalen und festen Verbund verknüpft sind, sondern allein durch intermolekulare Wechselwirkungen, den Van-der-Waals-Kräften, zusammengehalten werden. Da diese wesentlich schwächer ausgebildet sind als chemische Bindungen, können sie durch Zufuhr von Wärmeenergie gelöst werden. Thermoplaste sind daher im warmen Zustand plastisch und damit gut formbar und können auf gleiche Weise auch wieder umgeformt werden.
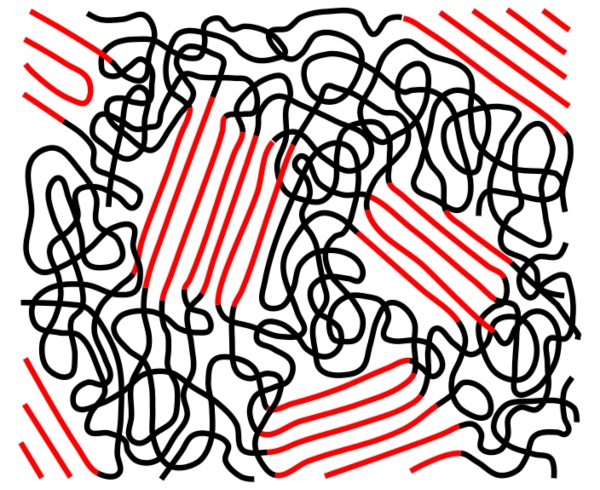
Spritzguss – ein Form-Verfahren für alle Kunststoffarten
Der Spritzguss ist neben der Extrusion eines der am häufigsten eingesetzten Verfahren für die Kunststoffverarbeitung. Sowohl Duroplaste als auch Elastomere und Thermoplaste können durch entsprechende, dem jeweiligen Kunststoff angepasste Spritzguss-Verfahren verarbeitet werden. Ihnen allen nach liegt ein gemeinsames Prinzip zugrunde: Die Ausgangsstoffe werden über einen Trichter in die Spritzeinheit gegeben, eine beheizte Schneckenpume, an deren Ende sich eine Düse befindet. Die erwärmte plastische Kunststoffmasse wird mit deren Hilfe unter hohem Druck in eine Hohlform eingespritzt, aus der nach dem Abkühlen das fertige Formteil entnommen werden kann. Auf diese Weise können Fertigteile auch komplizierterer Bauart auf einfache Weise in hohen Stückzahlen und ebenso Halbzeuge und Formteile zur Weiterverarbeitung hergestellt werden.
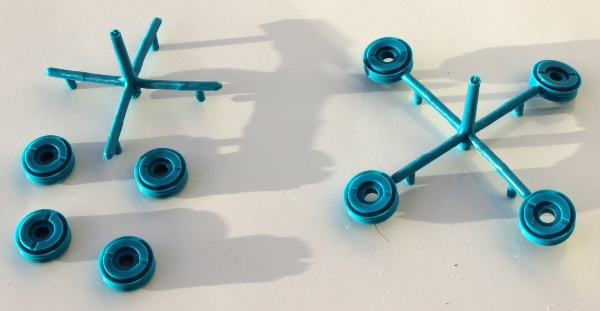
Schläuche und Rohre werden im Extrusionsverfahren hergestellt
Ein weiteres, sehr häufig eingesetztes Verfahren in der Kunststoffverarbeitung ist die Extrusion, das im Grunde ein modifiziertes, kontinuierlich arbeitendes Spritzguss-Verfahren darstellt. Im Gegensatz zum „klassischen“ Spritzguss-Verfahren ist es jedoch nur für Thermoplaste sinnvoll einsetzbar. Die aufgeschmolzene Kunststoffmasse wird mittels Schneckenpumpe durch eine entsprechend geformte Düse zu einem endlosen Strang gepresst. Auf diese Weise werden sowohl Halbzeuge, wie Stäbe, Rohre und Kunststoffschläuche als auch Kunststoffprofile mit komplizierterer Geometrie, zum Beispiel Bauteile für Fensterrahmen, hergestellt. Auch Folien können durch Extrudieren hergestellt werden.
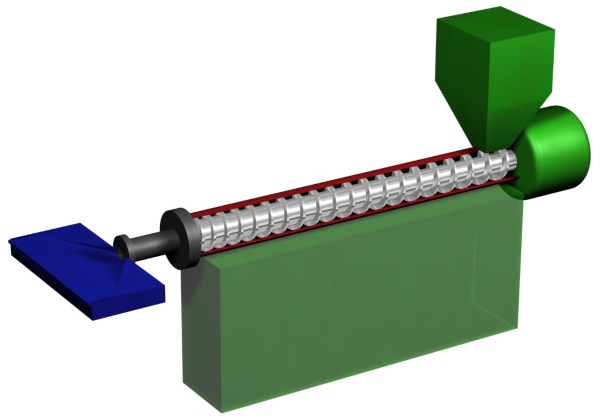
Zwei weitere, grundlegende Verfahren für die Verarbeitung von Kunststoffen sind das Blasformen und das Kalandrieren. Mit dem Blasform-Verfahren werden hauptsächlich Thermoplaste verarbeitet, wie Polyethylenterephthalat (PET), Polypropylen (PP), Polyamid (PA) oder Polyethylen (PE). Es ist eine Variante der Extrusion und stellt ein Verfahren der Kunststoffverarbeitung dar, das eingesetzt wird, um Hohlkörper, hauptsächlich Flaschen, aber auch Kanister, Kannen und ähnliche Behältnisse für Flüssigkeiten herzustellen. Bei dieser Methode wird ein durch Extrudieren vorgefertigter, schlauchförmiger Rohling in einer erwärmten Form mit Druckluft aufgeblasen, wobei er durch den daraufhin erfolgenden Andruck an die Wandung der Form das von ihr vorgegebene Profil annimmt, zum Beispiel das einer Getränkeflasche.
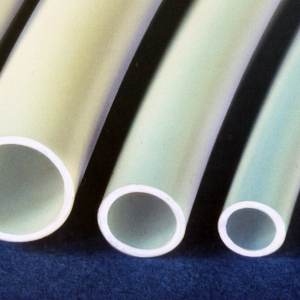
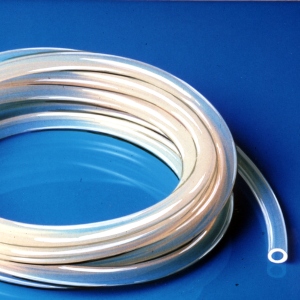
Werden größere oder auch spezielle Hohlformen gewünscht, steht mit dem Rotationsformen (engl.: Rotomolding) eine Verarbeitungsalternative zur Verfügung. Hierbei lagert sich der aufgeschmolzene Kunststoff an der inneren Wandung einer rotierenden Hohlform durch die Zentrifugalkräfte in mehreren Schichten ab. Es entstehen im Gegensatz zum „klassischen“ Blasformen dickwandige und vor allem spannungsfreie, nahtlose Hohlkörper, wie Kraftstofftanks mit Wanddicken bis zu fünfzehn Millimetern, Abfallbehälter und Fässer.

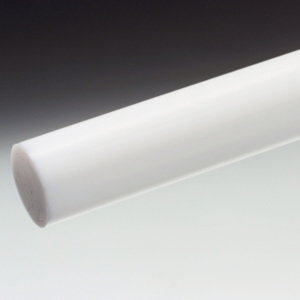
Das Kalandrieren wird sowohl für die Herstellung von Platten und Folien eingesetzt als auch zum Kaschieren und Beschichten von Materialien mit Kunststoffen mit dem Ziel, sie oberflächlich zu veredeln und kratzfest auszurüsten. Der Kunststoff wird zwischen mehreren beheizten Walzen aufgeschmolzen, um dann entweder zu Kunststoffplatten, Vliesen oder Folien ausgewalzt oder unter Druck auf Unterlagen, wie Holz oder Pappe, aufgebracht.
Während das Extrusionsverfahren sehr dünne Folien mit Stärken <0,1 mm liefert, die vorwiegend in der Lebensmittelindustrie und als Frischhaltefolie im Haushalt Verwendung finden, können durch Kalandrieren wesentlich stärkere Folien gewonnen werden.
Da Kunststoffe praktisch nicht verrotten, sind solche Kunststofffolien vor allem für das Bauwesen zur dauerhaften Isolierung gegen aufsteigende Feuchte und Nässe sowie im Gewächshausbau als robustes Abdeckmaterial von hohem Interesse.
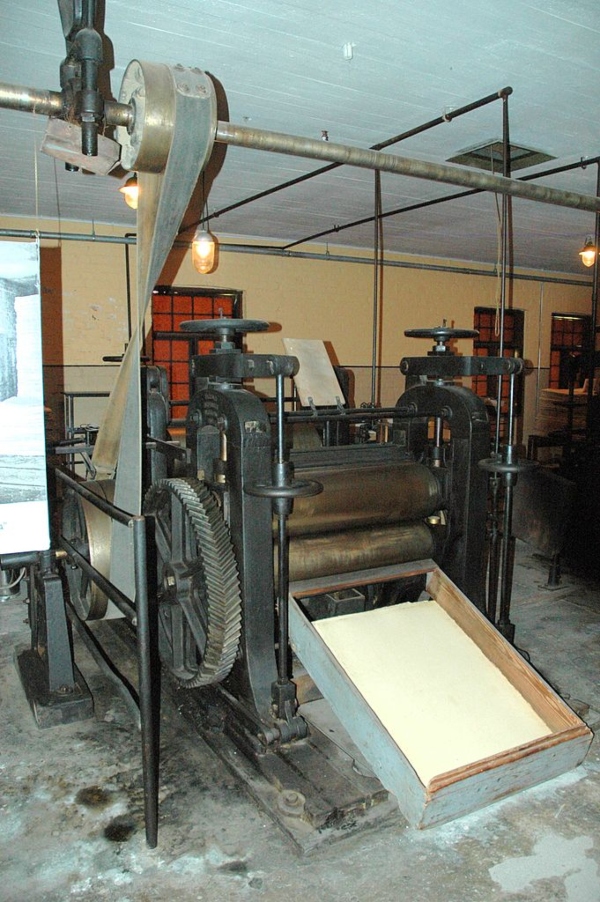
Oberflächenschutz von Metalloberflächen durch Wirbelsintern
Das Wirbelsintern ist ein Industrieverfahren zur Kunststoff-Beschichtung von Metalloberflächen, namentlich von rostgefährdeten Eisenblechen, um sie korrosionsfest auszurüsten. Hierfür eignen sich nur thermoplastische Kunststoffe.
Dazu wird das metallene Material auf Temperaturen zwischen 200 °C und 400 °C vorgewärmt und kurzzeitig, für wenige Sekunden, einem im Gasstrom verwirbelten Thermoplastpulver ausgesetzt, das dabei auf der Metalloberfläche aufschmilzt und einen porenfreien Überzug liefert.
In Frage kommen dafür Polyamid, Polyethylen, Polyester und thermoplastische Fluorpolymere, wie Ethylenchlortrifluorethylen (ECTFE). Das Wirbelsintern stellt eine wirtschaftlich effektivere Alternative zur gewöhnlichen Spritzlackierung dar, mit der insbesondere bei komplizierten Geometrien nicht immer das gesamte Material ausreichend erfassbar ist.
Geschäumte Kunststoffe – vielseitige Helfer
Geschäumte Kunststoffe sind dank ihrer Zellstruktur hervorragende Thermo-Isolierstoffe. Darüber hinaus wirken sie auch schall- und schwingungsdämpfend und zeichnen sich durch geringes Eigengewicht aus. Dabei wird zwischen „geschlossenzelligen“ und „offenzelligen“ Schaumstoffen unterschieden. In der Praxis hat man es jedoch meist mit „gemischtzelligen“ Materialien zu tun, wobei der die Anteile geschlossener und offener Zellen variabel ist und so der Schaumstoff dem jeweiligen Einsatzzweck gut angepasst werden kann.
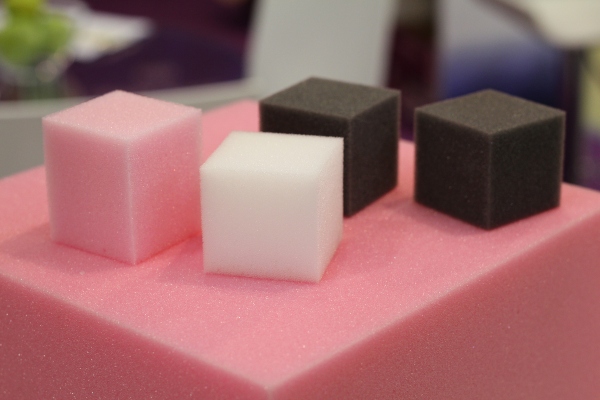
Grundsätzlich sind alle drei Kunststofftypen – Duroplaste, Elastomere und Thermoplaste – für die Gewinnung von Schaumstoffen geeignet. Dabei liefern Duroplaste und die meisten Thermoplaste harte Schäume, Elastomere hingegen Weichschäume. Allerdings lassen sich nur wenige aus der Vielzahl bekannter Kunststoffe zu wirtschaftlich verwertbaren Materialien verarbeiten. Hierzu gehören Polystyrol (PS) und Polyurethan (PUR). Letzteres kann je nach Reaktionsbedingungen sowohl zu Weichschaum, der beispielsweise als Moosgummi-Produkte in den Handel kommt, als auch zu Hartschaum verarbeitet werden. Geschäumte Kunststoffe stellen in Form von Platten, Profilen, Rundschnüren wie auch als speziell gefertigte Formteile für den Fahrzeugbau, für die Möbelindustrie, für den Bausektor und für Verpackungen wichtige, teilweise sogar unverzichtbare Werk- und Hilfsstoffe dar.
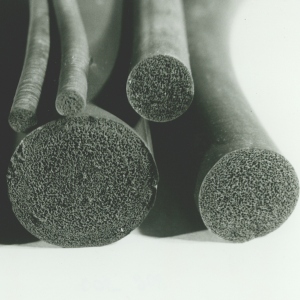
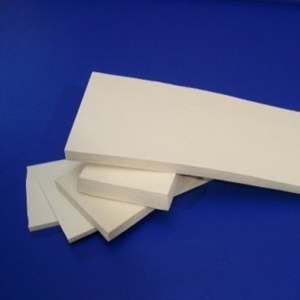
Die unterschiedlichen Kunststoffarten erfordern zum Teil sehr spezialisierte Verfahren für die Verarbeitung. Die grundlegenden, als Urformverfahren bekannten Möglichkeiten, um Kunststoffe zu Halbzeugen oder Fertigteilen zu verarbeiten, lassen die Vielfalt an Kunststoffprodukten zu, die uns im Alltag begleiten.