Plastics used in medical technology and pharmaceuticals are classified into six biocompatibility classes in the United States Pharmacopeia (USP), the US pharmacopoeia. To assign elastomers and other polymeric materials to one of these classes, they undergo various tests that determine biological reactivity in vivo – that is, in living organisms.
USP Class VI represents the strictest class and is considered equivalent to pharmaceutical approval for polymeric materials.
Plastics have long replaced materials such as metal, wood and glass in many areas of life and are therefore indispensable. It is not surprising that they have also found their way into medical technology.
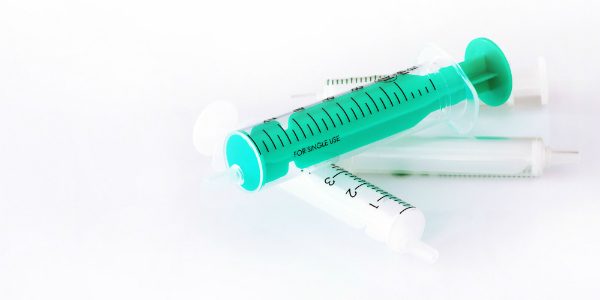
Plastics are used in diverse medical fields, both inside and outside the human body. Prostheses, implants, suture materials, tubing or disposable syringes are just a few examples that must meet specific material requirements. To ensure the best possible compatibility and thus safety for patients, a uniform classification system is essential. One of the most commonly used classifications is the USP classification, which will be explained in this article.
Who Is Behind the USP Classification?
USP is, as already mentioned, the abbreviation for the official US pharmacopoeia United States Pharmacopeia, which sets quality standards for medicines, but also for dietary supplements and food ingredients. It is published annually together with the National Formulary (NF). The publisher of the work is the non-profit, non-governmental organisation called the United States Pharmacopeial Convention (also usually abbreviated as USP), based in Rockville, Maryland, USA.
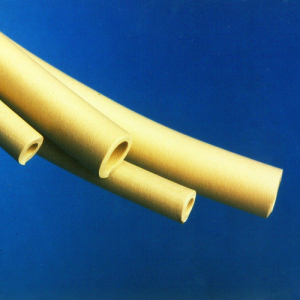
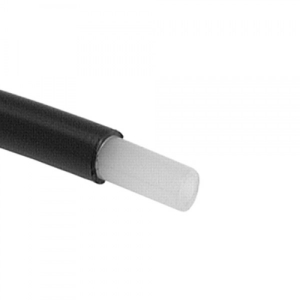
The primary goal of the USP is to maintain and improve human health. Through binding guidelines for the manufacture of medicines and medical products, the quality of examined substances is guaranteed. This increases the safety of patients and consumers. The correct identity of the active substance, active ingredient strength, quality, purity and composition are evaluated. Both manufacturers and regulatory authorities are guided by the established standards. Both prescription and non-prescription medicines must comply with USP-NF standards under US federal law.
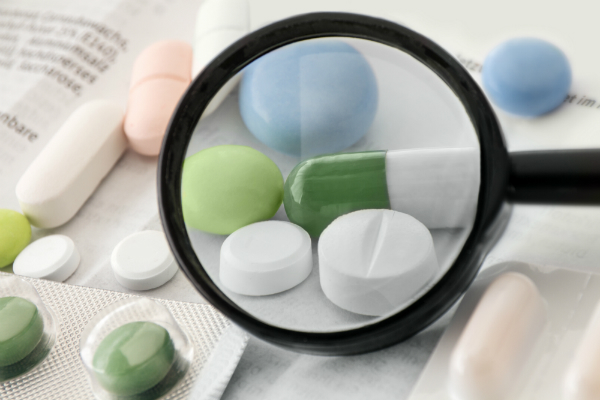
The Food and Drug Administration (FDA) is responsible for regulating compliance with the guidelines in the USA. In 1990, Article <88> of the USP pharmacopoeia first established test protocols and guidelines for medicine packaging, which were then transferred to plastics used in medicine and medical technology due to similar requirements.
The most important basic prerequisite for use in the living body or on humans is the biocompatibility of the material used.
Biocompatibility – What Is it?
Ideally, contact with the living system with which, for example, an implant is in contact produces no adverse effect whatsoever. According to IUPAC (International Union of Pure and Applied Chemistry), this is defined as biocompatibility. Adverse effects can include, for example, the release of toxic substances or rejection of the polymer by surrounding tissue. Therefore, USP classification represents a measure of the biocompatibility of a polymeric material.
How Does USP Class Classification Work?
Depending on the application, medical materials must meet specific requirements. For example, a USP Class I classification is sufficient for a product with skin contact, whilst USP Class VI is required for use as an implant or in contact with the bloodstream. Furthermore, contact duration is also an important criterion for deciding which guideline is necessary. For example, for contact with mucous membrane surfaces, Class I is prescribed for under 24 hours, Class III for 1 to 30 days, and Class V for application duration over 30 days.
To obtain a USP Class VI classification, the following tests of the material itself, as well as various extracts of this material, are carried out in external testing laboratories. The following three test areas can be broadly distinguished:
- Acute systemic toxicity: Determination of acute irritant effects on skin contact, inhalation and ingestion.
- Intracutaneous reactivity: The test material is brought into direct contact with the tissue for which it is intended in normal use.
- Implantation test: The tissue reaction after implantation into a living organism. The duration is typically five days.
These tests are carried out at fixed exposure times and temperatures to ensure comparability of results. Although biocompatibility testing must take place on the finished medical device, it is important for the manufacturer that all raw materials used are also tested and meet the requirements of the end product.
USP Class VI approval is applied and accepted for pharmaceutical and medical products in many countries worldwide.
Biocompatible Plastics with USP Class VI Certification
A variety of elastomers and thermoplastics are used in medical technology. They are used, for example, as manufacturing or coating materials for seals, O-rings and tubing for medical devices.
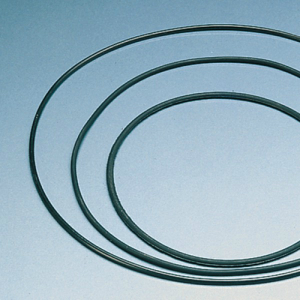
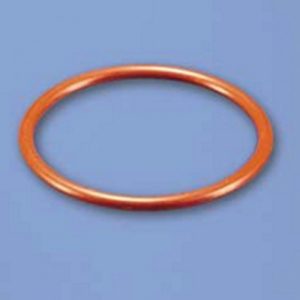
Biocompatible plastics such as polyethylene (PE), polystyrene (PS), polyvinyl chloride (PVC), polycarbonate (PC), polypropylene (PP) or polymethyl methacrylate (PMMA) are used as standard.
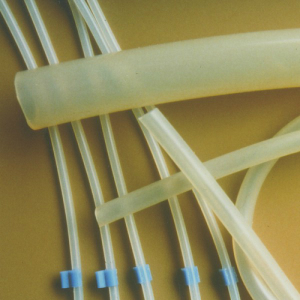
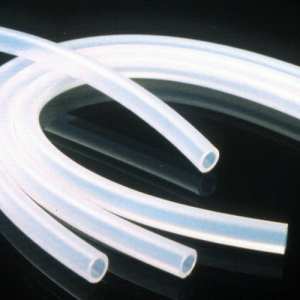
Medical tubing is often made from elastomers such as silicone or TYGON®. Fully fluorinated polymers are also often used because they are both biocompatible and chemically virtually inert. They also have a low coefficient of friction, can be easily sterilised and have advantageous dielectric properties.
Other materials that have a firm place in medical technology are polyvinylidene fluoride (PVDF) and polytetrafluoroethylene (PTFE). They are frequently used as materials for microporous filter membranes (0.01 to 10 μm) for sterile filtration and for the removal of fine particles.
In addition to these two plastics, many other fluoropolymers such as perfluoroalkoxy polymers (PFA), fluoroethylene propylene (FEP) and ethylene-tetrafluoroethylene copolymer (ETFE) are also used.
DIN-ISO-10993 Classification and FDA Conformity
Besides USP Class VI approval, which is actually often seen merely as a minimum requirement for biocompatibility, the DIN-ISO-10993 standard is gaining increasing importance. This test procedure is significantly more time-consuming and expensive. Even though the ISO-10993 standard is the stricter standard, it is still advisable to consider whether such certification is necessary for the intended use of the biocompatible material or finished product. For the majority of applications, a USP Class VI classification or even a lower USP Class certification is sufficient.
One also frequently reads about FDA-approved materials. FDA conformity is particularly important for use in the food sector.
Paragraph CFR 21.177.2600 of the FDA guidelines, for example, deals with “rubber articles intended for repeated use”.
It lists approved elastomers and substances used for their manufacture. FDA conformity is usually listed alongside USP Class VI certification.