Keramikbeschichtungen sind aus unserem Alltag nicht mehr wegzudenken. Viele Haushaltsgegenstände wie Backöfen, Pfannen, Lockenstab aber auch Haustüren oder Autolackierungen sind mit einer keramischen Schicht versehen. Damit werden die hervorragenden Eigenschaften von Keramiken, wie Korrosionsbeständigkeit, Verschleißfestigkeit, hohe Härte sowie elektrische und thermische Isolation, genutzt, um das Grundmaterial zu veredeln. In der Industrie wird die keramische Beschichtung oft zur Standzeitverlängerung von Werkzeugen und Anlagen und damit zur Kostensenkung eingesetzt.
Für die Abscheidung keramischer Schichten stehen verschiedene Verfahren zur Verfügung. Die Wahl des geeigneten Beschichtungsverfahrens hängt von der gewünschten Funktionalität der keramischen Schicht, des Beschichtungswerkstoffs, der Bauteilgeometrie sowie der Schichtdicke ab.
Zu den Vakuumbeschichtungsverfahren zählen die physikalische Gasphasenabscheidung (Physical Vapour Deposition, PVD) und die chemische Gasphasenabscheidung (Chemical Vapour Deposition, CVD) sowie die Beschichtung mit dem Sol-Gel-Verfahren. Als Spezialfall der Keramikbeschichtung kann die anodische Oxidation betrachtet werden.
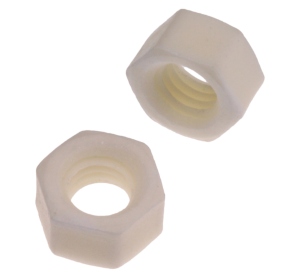
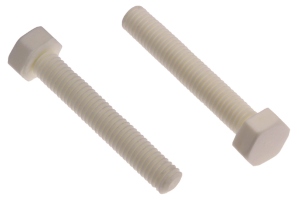
Neben Bauteilen mit keramischer Beschichtung werden heute auch zahlreiche Konstruktionselemente aus Keramik-Vollmaterialen angeboten, die im Industrieofenbau, in Medizingeräten sowie in der Luft- und Raumfahrttechnik Anwendung finden. Keramikhülsen, Keramikschrauben, Keramikmuttern und Keramikscheiben zeichnen sich durch eine besonders hohe Reinheit und Temperaturbeständigkeit aus.
Thermische Spritzverfahren
Thermische Spritzverfahren beruhen auf dem Prinzip, dass der Beschichtungswerkstoff aufgeschmolzen wird und sich die geschmolzenen Partikel mit hoher Geschwindigkeit auf der zu beschichtenden Oberfläche abscheiden. Die Einteilung der verschiedenen Spritzverfahren erfolgt nach der verwendeten Energiequelle.
Wird die Energie durch ein brennbares Gas oder Flüssigtreibstoff bereitgestellt, spricht man von Flammspritzen. Dabei wird das keramische Pulver in die Flamme transportiert, aufgeschmolzen und auf der zu beschichtenden Oberfläche abgeschieden.
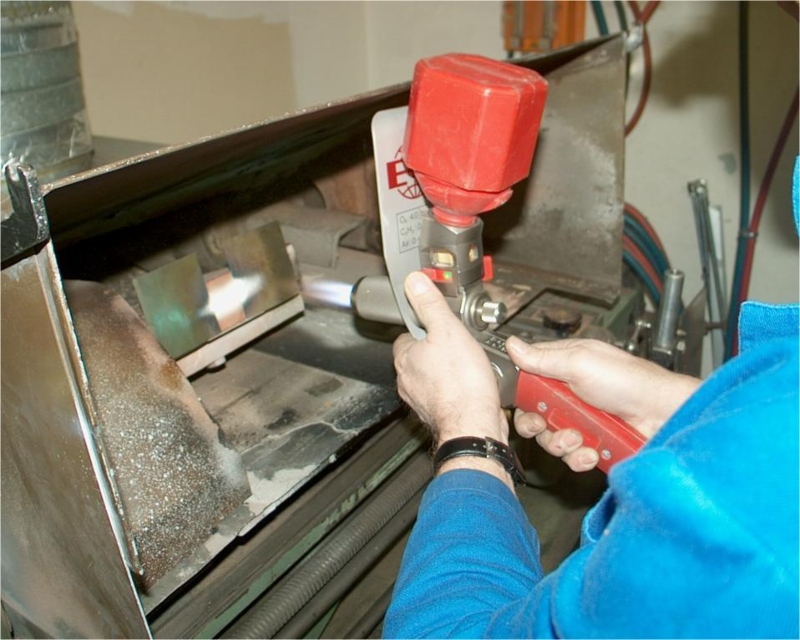
Beim Lichtbogenspritzverfahren wird durch Anlegen einer Spannung ein Lichtbogen gezündet und dabei durchströmendes Gas ionisiert. Das keramische Pulver wird in die Plasmaflamme eingespritzt, darin geschmolzen und durch den Plasmastrahl auf die Substratoberfläche transportiert.
Beim Laserspritzen treffen Laserstrahl und das pulverförmige Beschichtungsmaterial gleichzeitig auf der zu beschichtenden Oberfläche auf. Dabei wird sowohl das Pulver als auch die Bauteiloberfläche aufgeschmolzen, wodurch eine gute Schichtanbindung an die Oberfläche gewährleistet wird.
Mit Spritzverfahren können oxidische Keramiken wie Aluminiumoxid (Al2O3), Chromoxid (Cr2O3), Titandioxid (TiO2), Zirkonoxid (ZrO₂) oder Yttriumoxid (Y2O3) oder eine Mischung aus diesen abgeschieden werden.
Anwendung finden diese Schichten deshalb zum Beispiel in Kesselanlagen von Kraftwerken, Stahlwerken und der chemischen Industrie sowie bei Turbinenschaufeln, Flugzeugtriebwerken, Kolbenstangen und Kurbelwellen.
PVD-Beschichtung
Bei der PVD-Beschichtung werden das zu beschichtende Werkstück, auch Substrat genannt, und das abzuscheidende Material, auch als Target bezeichnet, in eine Vakuumkammer eingebaut. Durch Energieeintrag wird das Target verdampft und die Atome und Ionen bewegen sich ballistisch oder durch elektrische Felder gerichtet durch die Beschichtungskammer.
Als Energiequelle können Elektronenstrahl, Ionenstrahl, Laser oder ein Plasma genutzt werden. Damit das verdampfte Material die Substratoberfläche erreichen kann und nicht durch Streuung an Gasteilchen abgelenkt wird, muss die Keramikbeschichtung im Vakuum durchgeführt werden. Typische Druckbereiche während des Beschichtungsprozesses sind 10-4 bis 10-2 mbar (0,0001 bis 0,01 mbar).
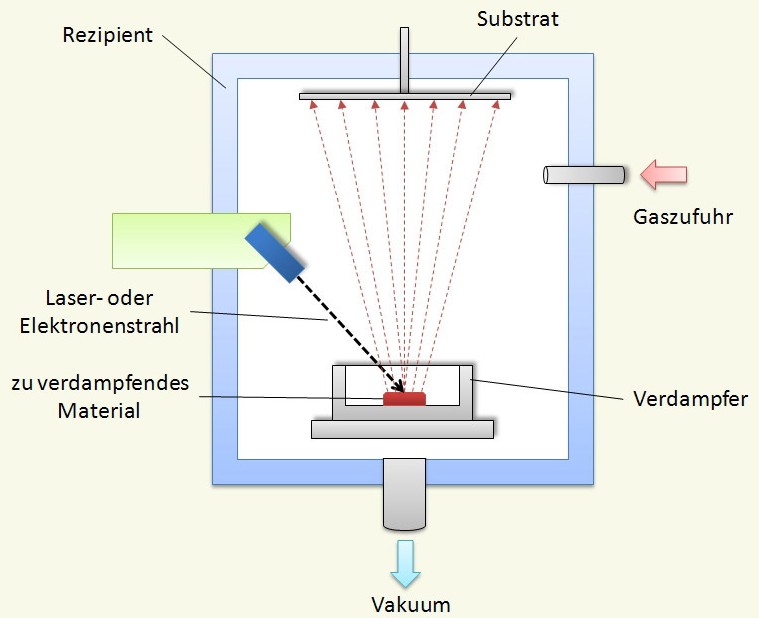
Die keramische Beschichtung wird entweder durch Verdampfen von Keramiken erhalten oder durch Verdampfen von Metallen und dem gleichzeitigen Einlass eines Reaktivgases. Beim Einlass von Sauerstoff können Oxide, bei der Anwesenheit von Stickstoff Nitride und bei der Verwendung von Kohlenwasserstoffen Carbide abgeschieden werden.
Durch die Notwendigkeit, die Werkstücke in eine Vakuumkammer zu bringen, ist der Einsatz hinsichtlich Größe und Durchsatz begrenzt und die Kosten im Vergleich zu Spritzverfahren höher. Weiterhin sind nicht alle Geometrien geeignet, da Abschattungen zu einer inhomogenen Schichtdickenverteilung führen können. So wird bei der Beschichtung eines Gewindes auf den Flanken, die dem Target zugewandt sind, eine dickere Schicht abgeschieden als auf den Flanken, die dem Target abgewandt sind.
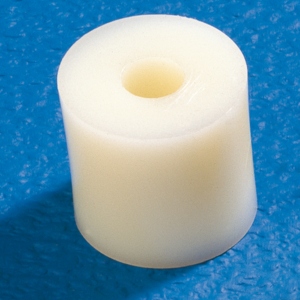
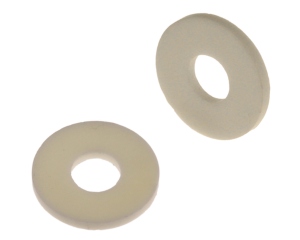
Vorteile liegen in der großen Auswahl an Beschichtungsmaterialien, wie Metalle, Legierungen, Halbleiter, Metalloxide, Nitride und Carbide, sowie in der Vielfalt der zu beschichtenden Substratmaterialien wie Metalle, Keramiken, Kunststoffe und Glas. Mit diesem Prozess können oxidische, nitridische sowie karbidische Keramikschichten abgeschiedenen werden. Typische PVD-Schichten sind Titannitrid, Titancarbonitrid, Titanaluminiumnitrid, Chromnitrid sowie Zirkonnitrid.
Diese Keramikschichten werden aufgrund ihrer Eigenschaften, wie gute Verschleißfestigkeit, sehr hohe Härte und geringer Reibungskoeffizient, zur Oberflächenbeschichtung von Zerspanungs- und Umformwerkzeugen eingesetzt.
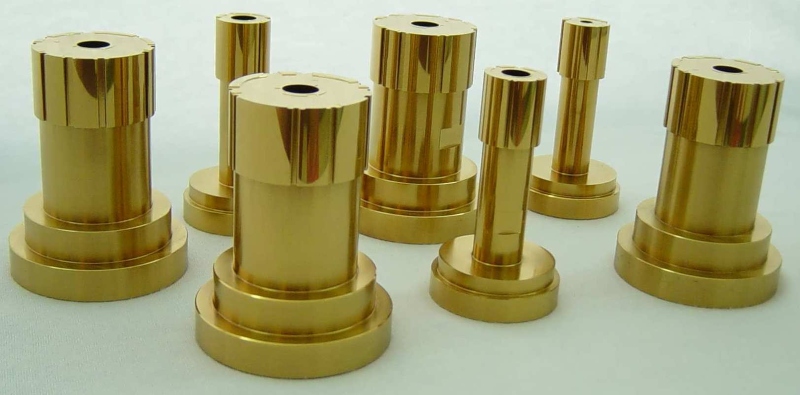
Am Bekanntesten sind die gelb-goldenen Titannitrid-Schichten. Als Verschleißschutzschicht wird sie auf Werkzeugen, Schmuck, Brillen und Bestecke aufgebracht. Aufgrund ihrer Biokompatibilität werden auch chirurgische Instrumente und Implantate mit Titannitrid beschichtet.
CVD-Beschichtung
Die CVD-Beschichtung beruht auf der chemischen Reaktion gasförmiger Ausgangsmaterialien, auch Präkursoren genannt, mit einer heißen Oberfläche. Dabei scheidet sich an der Oberfläche ein Feststoff ab. Um Gasphasenreaktionen zu unterdrücken, muss in Druckbereichen von 10-3 bis 1 mbar (0,001 bis 1 mbar) gearbeitet werden.
Bei der thermischen CVD muss das Substrat auf Temperaturen zwischen +700 und +1200 °C, je nach Schichtsystem, aufgeheizt werden. Deshalb ist die thermische CVD nur für die Beschichtung temperaturbeständiger Materialien geeignet. Beispiele für die Keramikbeschichtung mit dem thermischen CVD-Prozess sind Aluminiumoxid aus Aluminiumchlorid, Kohlendioxid und Wasserstoff, Bornitrid aus Borchlorid und Ammoniak, Siliziumnitrid aus Siliziumchlorid, Ammoniak und Wasserstoff, Titancarbid aus Titanchlorid und Methan.
Wegen ihrer hohen Härte werden Titancarbid-Schichten zur Veredelung von Sägeblättern, Umformwerkzeugen, Schneidwerkzeugen und Fräswerkzeugen eingesetzt.
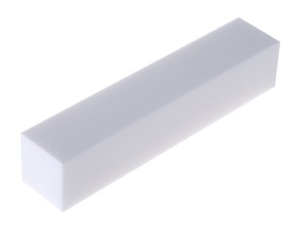

Die plasmagestützte CVD (plasma-enhanced, PECVD) nutzt die Plasmaenergie zur Aufheizung und chemischen Reaktion der Präkursoren. Dadurch kann die Keramikbeschichtung bei einer Substrattemperatur von weniger als +300 °C erfolgen und hat damit einen größeren Einsatzbereich als die thermische CVD. Anwendung findet die PECVD vor allem bei der Abscheidung von Siliziumnitrid und Siliziumdioxid in der Halbleiterindustrie und diamantartigen (diamond like carbon, DLC) Schichten.
Nachteile der Keramikbeschichtung mit dem CVD-Prozess sind Kosten, die mit dem Vakuumprozess verbunden sind und die Verfügbarkeit leicht flüchtiger Präkursoren, die in die Gasphase gebracht werden können. Vorteil ist die homogene Oberflächenbeschichtung komplexer Formen und dreidimensionaler Oberflächen.
Keramikbeschichtung mit dem Sol-Gel-Verfahren
Bei dem Sol-Gel-Prozess werden als Präkursoren oft Alkoxide und Alkoholate von Metallen oder Halbmetallen eingesetzt. Beispiele dafür sind: Tetraethylorthosilicat , Aluminium-(2-propylat), Titan-(2-propylat) und Zirkonpropylat. Die Präkursoren werden in einem Lösungsmittel gelöst und hydrolysieren durch Zugabe einer Säure oder Lauge zu einem Sol. Die hydrolysierten Produkte kondensieren und bilden ein polymeres Netzwerk, das Gel.
Durch Trocknung dampft das Lösungsmittel ab und reaktive Gruppen kondensieren. Infolge der einhergehenden Schrumpfung zeigt das resultierende Xerogel unterschiedliche Struktur und Porosität verglichen mit dem Ausgangsmaterial.
Aus diesem Xerogel entsteht durch Sintern oder Laserhärtung eine keramische Schicht. Schichtdicken liegen bei diesem Verfahren zwischen zehn Nanometern und einigen Mikrometern, wobei für größere Schichtdicken der Beschichtungsvorgang mehrmals wiederholt werden muss.
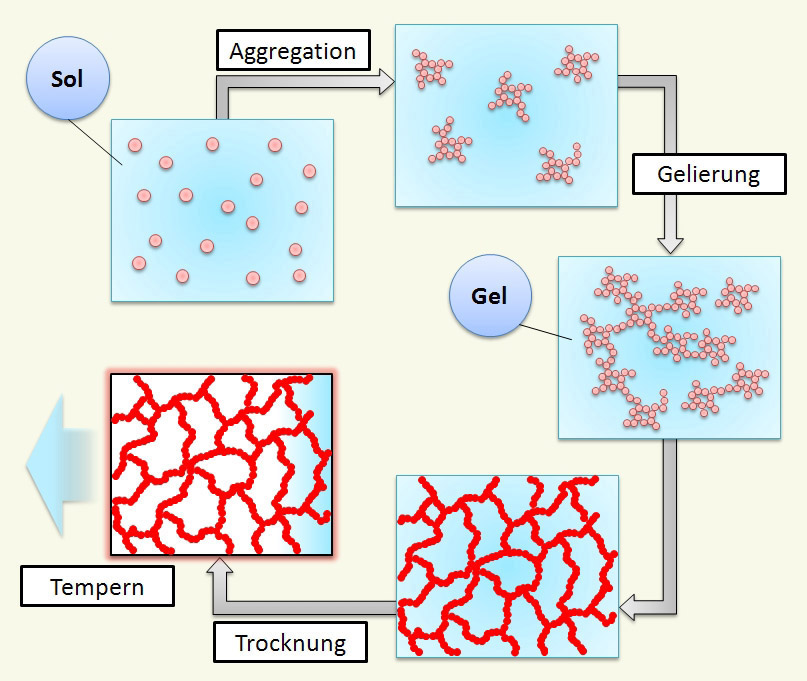
Nachteile der Sol-Gel-Keramikbeschichtung sind mögliche Rissbildungen während des Trocknungs- und Sinterprozesses und die hohe Temperatur beim Sintern (über +400 °C) sowie die Verfügbarkeit einiger Edukte. Ein Vorteil liegt in der homogenen Schichtdicke über die gesamte Oberfläche, auch bei komplexer dreidimensionaler Geometrie.
Anwendung findet das Sol-Gel-Verfahren bei der Beschichtung von Fassaden und Solarzellen. In der Automobilindustrie können Innenraumarmaturen, Felgen und Zierleisten durch Sol-Gel-Schichten veredelt werden, in der Kosmetikindustrie Verpackungen von Kosmetika.
Anodische Oxidation
Bei der anodischen Oxidation wird das zu beschichtende Bauteil in einem geeigneten Elektrolyten als Anode geschaltet. Unter definierten Prozessbedingungen wie Stromdichte, Temperatur, Elektrolyt und Kathodenmaterial bildet sich auf der Oberfläche eine Oxidschicht.
Bei dem Eloxal-Verfahren (elektrolytische Oxidation von Aluminium) wird auf Aluminiumoberflächen eine 5 bis 25 µm dicke Aluminiumoxidschicht als Korrosionsschutz gebildet. Bei der anodischen Oxidation von Titanoberflächen wird eine dünne (unter 1 µm) Oxidschicht gebildet, die als Interferenzfilter wirkt. In Abhängigkeit von der Schichtstärke können verschiedene Farben erzeugt werden. Diese dünnen Titanoxidschichten werden zur Farbkodierung von Dentalimplantaten und medizinischen Instrumenten eingesetzt.
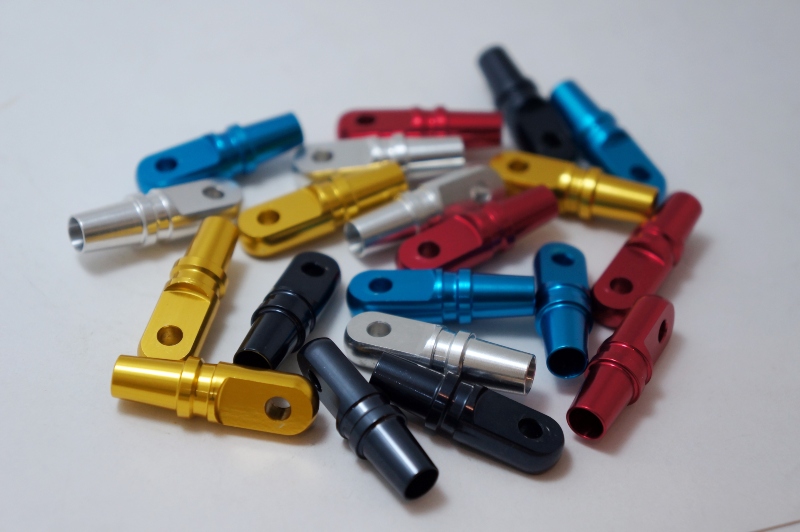
Durch die Auswahl eines geeigneten Beschichtungsverfahrens und Schichtmaterials können für die meisten Anwendungen kostengünstige keramische Beschichtungen auf verschiedenen Grundmaterialien realisiert werden.
Quellenangaben: 1) http://www.langlet.de/wp-content/uploads/2019/11/keramische_Werkstoffe.pdf 2) Bach, Duda: „Moderne Beschichtungsverfahren“, Wiley-VCH, Weinheim, 1998 3) https://www.chemie.de/lexikon/Eloxal-Verfahren.html
Bildquellen: Beitragsbild | © chaiwat – stock.adobe.com Flammspritzverfahren | © Ruppex - Aufnahme aus Spritzlabor, CC BY-SA 3.0, https://commons.wikimedia.org/w/index.php?curid=11774201 Physikalische Gasphasenabscheidung (PVD) | © Dipl-ing-metaller, CC BY-SA 3.0, https://commons.wikimedia.org/w/index.php?curid=11396783 Mit Titannitrid beschichte Stanzwerkzeuge | © Sunyataburus, CC BY-SA 3.0, https://commons.wikimedia.org/w/index.php?curid=8905197 Schematische Darstellung des Sol-Gel-Verfahrens | © Dipl-ing-metaller, CC BY-SA 3.0, https://commons.wikimedia.org/w/index.php?curid=11396797 Eloxierte Aluminium-Bauteile in verschiedenen Farben | © Shinpanu – stock.adobe.com