The Food and Drug Administration, or FDA, is the United States’ federal authority responsible for overseeing the safety of all goods sold within the USA. This oversight includes not just domestically produced items but also all imports, which is why the agency’s guidelines and requirements are relevant far beyond the US. For any company exporting to the US, FDA standards are binding — a product approved in Europe is not automatically FDA-compliant. Manufacturers therefore increasingly align their quality standards with FDA requirements to remain competitive in international markets. A key area of responsibility is food safety — which includes the monitoring of all plastic products that come into contact with ingredients or consumables, such as production machinery, hoses and pipes, packaging, and much more. Here, we explain what this means in practice and what factors you need to consider.
FDA Approval in Food Production
The FDA sets extremely strict standards for any food produced in, or imported into, the United States. These measures are in place to prevent nationwide health crises caused by contaminated or unsafe food products. Only companies whose processes and materials are certified as FDA-compliant are permitted to supply the US market.
To meet these standards, materials must be highly durable and must not transfer any substances into the food. In processing, a wide range of plastics with different properties come into contact with food. Each material must be FDA-compliant and carefully selected for its intended use.
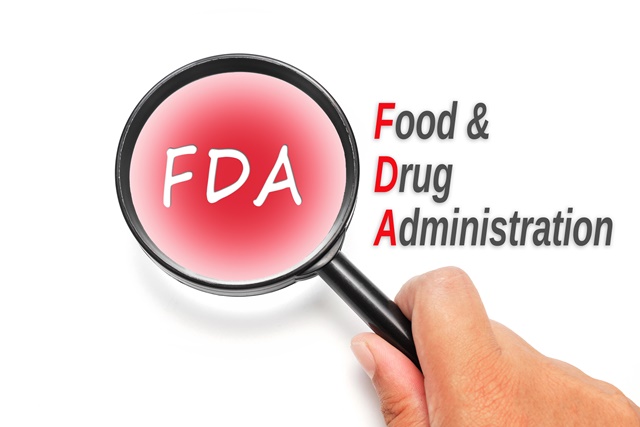
The Right Material — Materials in Food Processing
All materials that come into direct contact with edible goods must be exceptionally pure and resistant under the given process conditions — whether they are natural or synthetic. This applies to containers, pipes, seals and gaskets. In many cases, these components are made from plastics whose chemical composition is critical.
The requirements in this industry are far stricter than in other sectors. This is mainly because contamination in a single batch of food can affect thousands of people before the producer can act. Export shipments require an FDA certificate, which is granted only after detailed evidence of compliant production.
Hoses for Food Production — FDA-Approved and Certified
Tubes and hoses are mainly used to transport liquids and pastes in food production. The key factor is the material’s chemical resistance to ingredients — for example, fatty acids and oils. Food-grade hoses must also have smooth inner surfaces to allow thorough cleaning and to prevent germs from accumulating in porous areas.
Most materials are known by an abbreviation, a chemical name, and a trade name or brand name. For clarity, both the chemical and brand names are provided below.
NBR Food Hose
NBR (acrylonitrile butadiene rubber), sold under the brand name Perbunan®, is a synthetic rubber highly resistant to alcoholic solutions up to 15% and to both plant and animal fats. These NBR food hoses have smooth inner surfaces that allow complete drainage and can be steam-cleaned at 121 °C. This material is completely taste- and odor-neutral and resistant to aging and weathering.
A cover made from a combination of EPDM (ethylene propylene diene rubber) and NBR improves durability and boosts working pressure resistance up to 20 bar. FDA compliance is marked directly on the hose. Its operating temperature range is -25 °C to +90 °C, and it tolerates short-term cleaning at up to 120 °C.
PVC Food-Grade Pressure Hose
One of the best-known plastics is PVC (polyvinyl chloride), available under trade names such as Tygon® or THOMAVINYL. This hose is made from flexible PVC-P for transporting liquid food products. It contains no silicone, metals, or diethylhexyl phthalate (DEHP) plasticisers. This is crucial because DEHP and other phthalates pose significant health risks. Modern plasticisers based on citric acid or adipic acid esters, however, are considered harmless under strict FDA guidelines and are now used exclusively for PVC hoses in food applications.
The hose’s transparency allows for continuous visual monitoring of the product flow. Its operating temperature range is -10 °C to +60 °C; PVC should never be heated beyond this range to avoid the release of harmful substances into the food. The PVC food-grade pressure hose is FDA-compliant and also meets current European standards — and thanks to its polyester fabric reinforcement, it is pressure-resistant up to 20 bar.
Other Certified Materials for the Food Industry
Besides hoses for transferring liquids and pastes, various other components can come into contact with food during production, packaging, or storage. These must also be FDA-compliant if intended for export to the US. Examples include seals, films, liners, and power transmission elements.
PTFE Film
PTFE (polytetrafluoroethylene) is sold under various trade names, including TEFLON® PTFE, Hostaflon® TF, Chemfluor®, and THOMAFLON. Virgin PTFE is a biocompatible material widely used in this sector. Its non-porous surface is entirely hydrophobic, electrically insulating, resistant to chemicals, and free from any extractable substances or plasticisers.
PTFE foils and films are extremely durable and can be used at temperatures from -200 °C to +250 °C. It is easy to clean and can be sterilised using standard cleaning agents. Typical uses include work surfaces, linings, or coverings for containers and equipment.
Silicone Foam Plate
This plate is made from SI (silicone rubber) and is known under brand names like Versilic® or THOMASIL. It has high elasticity and is available in various thicknesses and sizes. Its resistance to heat and cold is impressive, with an optimal working temperature range of -45 °C to +220 °C. Platinum catalysts are used for crosslinking the silicone monomers — unlike conventional silicones that use peroxides — resulting in excellent biocompatibility and physiological safety. Platinum-cured silicone rubber is weather- and aging-resistant, mechanically robust, electrically insulating, and permeable to gases like carbon dioxide. Since it is FDA-compliant, it is widely used as sealing, packaging, or thermal insulation material in food applications.
TPE Round Cord
TPE (thermoplastic elastomer) softens at higher temperatures and can be reshaped, returning to its original elasticity upon cooling without losing its form. This makes it ideal for sealing applications, as it can adapt to almost any shape. Its operating temperature range is -50 °C to +95 °C.
Additional Approved Sealing Cords
EPDM/PP Round Cord — This thermoplastic composite of ethylene propylene diene (EPDM) and polypropylene (PP) offers excellent resistance to acids, alkalis, oxidising agents, and polar solvents — with the exception of fuels, mineral oils, hydraulic fluids, and hydrocarbons. It is also ozone-, aging-, UV- and weather-resistant, mechanically robust, and highly dimensionally stable.
Silicone Rubber Round Cord — This FDA-compliant material provides excellent resistance to synthetic, animal, and vegetable oils. It remains flexible at temperatures from -60 °C to +200 °C and tolerates short-term spikes up to +230 °C.
Natural Rubber Round Cord — Also FDA-approved, this natural material is resistant to acids and alkalis, very elastic, and tear-resistant. Its operating temperature range is -40 °C to +80 °C.
POM Round Bar
Polyoxymethylene (POM), sold under the trade name Delrin®, is primarily used to build power transmission components thanks to its high mechanical strength and tensile and compressive properties. The FDA-compliant POM is commonly machined into sliding bearings, rollers, and gears, where its excellent low-friction properties ensure minimal wear.
POM is easy to machine and retains its impact strength even at low temperatures. This weather-resistant and physiologically safe material operates reliably from -40 °C to +105 °C, with short-term exposure possible up to +140 °C.