Polyethylene (PE) is one of the plastics that, thanks to its favourable material properties, has found a wide range of applications and become an indispensable mass-market material.
Polyethylene – The Most Commonly Used Plastic
Abbreviated as PE, Polyethylene is the most commonly used plastic. In Europe alone, millions of tonnes are produced every year and processed into plastic products such as hoses, semi-finished products, films, sheets, rods, and profiles. Additional quantities are used for manufacturing coatings, adhesives, fibres, or are exported in smaller amounts.
PE is especially used in the packaging industry, as the material is physiologically safe, neutral in taste, and odorless. Large quantities of polyethylene are also used for plastic bags.
According to a 2015 report by the German Federal Environment Agency, each EU citizen uses at least 200 plastic bags made of polyethylene and other plastics per year—bags that sooner or later become waste and often end up uncontrolled in the environment. To counter this, many retailers have been charging fees for plastic bags since 2018. The free distribution of plastic bags has been restricted across the EU, with numerous member states introducing bans or mandatory charges. In the coming years, plastic bags are expected to disappear completely from retail—this includes even the once-beloved polyethylene shopping bags.
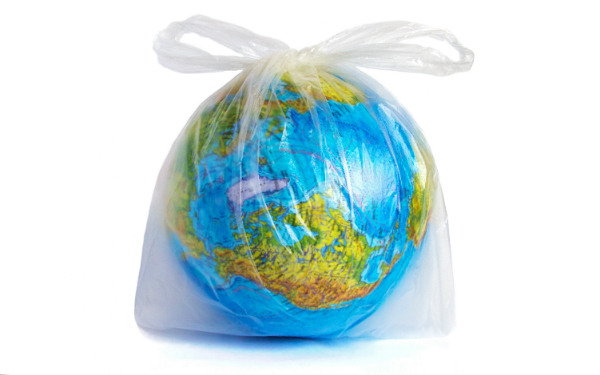
An amendment to the European Packaging Directive (94/62/EC) required member states to either limit the consumption of single-use plastic bags with a wall thickness of less than 50 μm to a maximum of 40 pieces per inhabitant per year by the end of 2025, or to ensure that these are not provided free of charge.
In Germany, the use of such plastic bags has already been declining for several years: As early as 2021, the EU requirements were met with 39 plastic carrier bags per inhabitant per year. Since January 1, 2022, the placing on the market of plastic bags with a wall thickness of less than 50 μm that are intended for filling goods at points of sale has been prohibited. Exempt from this are so-called “shirt bags” with a wall thickness of less than 15 μm, which are intended for hygienic reasons as packaging for loose food items such as fruits and vegetables.
Polyethylene Is a Versatile Plastic
Since the 1950s, polyethylene has become a leading mass-market plastic. It combines many positive properties and can be tailored to specific applications through the manufacturing process or the addition of functional additives. As a thermoplastic that softens at temperatures above +80 °C, PE is easy to process. It is resistant to most acids and alkalis, as well as to oils, fats, petrol, and aliphatic hydrocarbons. This chemical resistance, combined with mechanical robustness, makes PE tubing indispensable in hose technology. However, it is not resistant to strong oxidising acids such as nitric acid, for which alternative materials must be chosen.
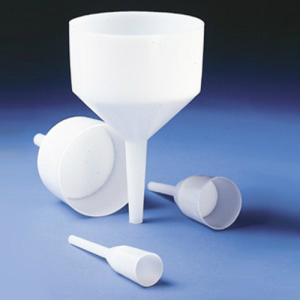
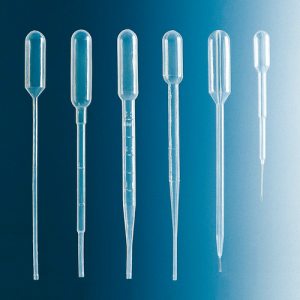
While PE’s UV resistance is naturally low, it can be significantly improved by adding carbon black as an additive. In the food industry, polyethylene films are favoured because the material is safe for health, offers moderate gas permeability compared to other plastics, and absorbs very little moisture overall. Polyethylene is also an excellent electrical insulator, making it ideal for cable coatings and non-conductive components in the electrical industry. Another advantage: polyethylene can be produced with varying degrees of transparency — from almost completely clear to fully opaque. Other properties such as density, strength, or hardness can also be modified through the choice of manufacturing process.
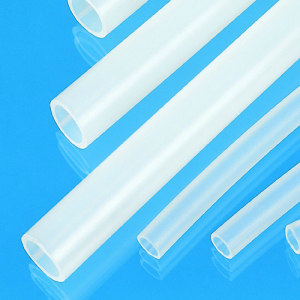
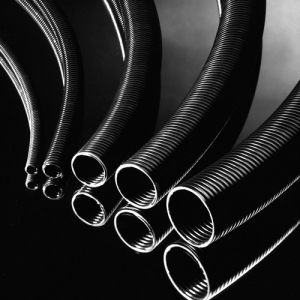
Different Manufacturing Methods, Different Properties
LDPE
As early as 1898, German chemist Hans von Pechstein (1850–1902) described the polymerisation of ethylene into polyethylene, though the discovery initially had no industrial significance. In 1935, chemist Michael W. Perrin (1905–1988) of British company Imperial Chemical Industries (ICI) developed an industrially viable process for producing polyethylene from ethanol (C₂H₅OH).
However, it was only after further chemical-technical improvements — and especially the use of ethylene (CH₂=CH₂) from petroleum refining instead of ethanol — that ICI began large-scale polyethylene production in 1940.
The radical polymerisation of ethylene takes place at high pressures (150 to 300 bar) and temperatures around 300 °C, resulting in a polymer with highly branched chains. Due to its low density of 0.92–0.93 g/cm³, this high-pressure polyethylene is known as LDPE (low-density polyethylene). It is characterised by a low melting point and a soft consistency in its virgin (unfilled) form.
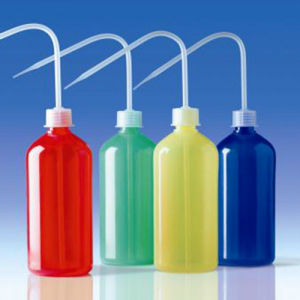
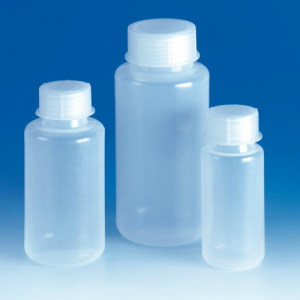
HDPE
In the 1950s, German chemist Karl Ziegler (1898–1973) and Italian chemist Giulio Natta (1903–1979) made a decisive breakthrough in catalyst research. They developed organometallic catalysts that enabled polyethylene production at much lower temperatures and pressures compared to the ICI process. This polymer features minimally branched chains and a higher density of 0.94 to 0.97 g/cm³, earning it the name HDPE (high-density polyethylene).
Compared to LDPE, HDPE is stiffer, harder, and has greater abrasion resistance due to its higher crystallinity.
Today, in addition to the classic Ziegler-Natta catalysts, newer catalyst systems such as Kaminsky catalysts based on metallocenes — developed by German chemists Walter Kaminsky (1941 – 2024) and Hansjörg Sinn (*1929) — are also used.
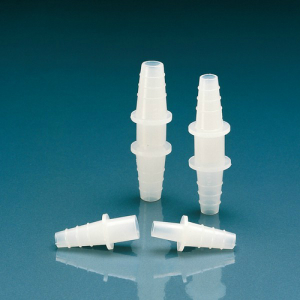
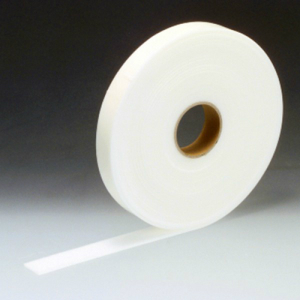
Flexible Processing
Besides the economical production methods, polyethylene offers cost-effective downstream processing into semi-finished or finished goods. Unprocessed polyethylene, available as powder or granules, can be processed using nearly all conventional thermoplastic methods, including injection moulding, blow moulding, extrusion, and calendering. Polyethylene is used to manufacture not only sheets and rods but also films, hoses, and pipes, as well as tanks, tank linings, bottles, small components, and disposable articles for the medical and laboratory sectors.
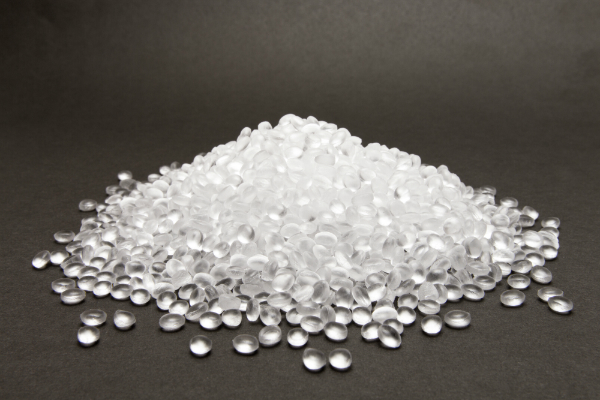
In many cases, these items replace equivalent glass products, significantly improving occupational safety. Additionally, polyethylene is used to make countless everyday household items — so common that they are often taken for granted.
Tailor-Made Polymers
Beyond manufacturing methods, the properties of polyethylene can be modified by additives, copolymers, or chemical post-treatments. For outdoor applications, PE materials are typically enhanced with around 2% carbon black to improve UV resistance. “Foamed polyethylene” is produced by adding blowing agents to the polymer melt and is used for insulation purposes. Other refinement methods include chemical treatments:
The chlorosulfonation of PE with elemental chlorine (Cl₂) and sulfur dioxide (SO₂) yields an elastic material used, for example, in durable floor coverings.
Through copolymerization, it is possible to expand the spectrum of tailor-made polymers based on polyethylene, for example through copolymerization of ethylene and vinyl acetate. Thus, copolymerization of ethylene and vinyl acetate produces a copolymer that is very impact-resistant and is used for paper coatings or processed further into specialized adhesives. Finally, highly crosslinked polymers with higher acid resistance can be obtained through UV radiation or with peroxide-based chemical radical initiators.
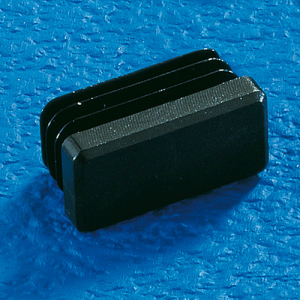
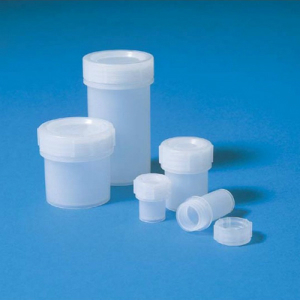
Renewable Resources and Recycling
In recent years, there has been increasing interest in producing polymers from renewable resources. In Brazil, for example, bio-based polyethylene is produced from sugarcane-derived ethanol — essentially reviving Perrin’s 1930s approach with modern technology. Given the widespread use of polyethylene — in hoses, pipes, films, and many other semi-finished and finished products — the question of end-of-life management becomes critical.
In principle, recycling the material itself is the primary goal for thermoplastic materials and therefore also for polyethylene.
PE can be melted and reprocessed almost 100%, and can typically be recycled four to five times with acceptable material properties. This gives polyethylene a relatively positive environmental balance compared to many other plastics. However, effective recycling requires clean, sorted streams — separated into LDPE and HDPE and free from foreign materials — a challenge that remains unresolved for many types of recyclable plastics.